
Main roadway type selection - Black King Kong report
Preface
In the complex system of mining operations, the main access roadways are like the arteries of the human body, undertaking key tasks such as ore transportation, personnel passage, ventilation, and drainage. They are important channels connecting the surface and underground ore bodies, and the choice of their type directly affects the efficiency, cost, safety, and sustainability of mining operations. From the simple inclined shaft development in the early stages of relatively backward mining technology, to the widespread use of vertical shaft development with the improvement of mechanization and technology level, and to the current comprehensive consideration of various types of access roadways based on different mine conditions, this development process has witnessed the mining industry's continuous pursuit of efficient and safe mining. In today's mining field, how to scientifically and reasonably select the type of main access roadway based on factors such as mine topography, geological conditions, and ore body occurrence conditions has become an important issue facing mining engineers. This article will delve into the selection factors, development process, and application status of the main access roadway types, aiming to provide valuable references for mining operations.
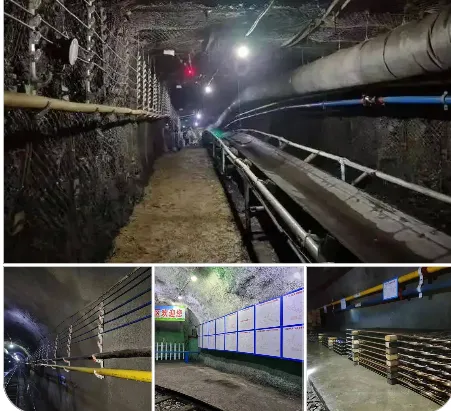
I. Key Factors Influencing the Selection of Access Roadway Types
(1) Basic Influence of Topography and Geology
Mine topography and geological conditions are like cornerstones, profoundly influencing the selection of access roadway types. In terms of topography, if the mine is located in a mountainous area with crisscrossing mountains and large undulations, adit development may be the preferred choice. When the ore body is located in a mountainous area and buried above the ground level of the surrounding plains, adit development has significant advantages such as short construction time, low cost, reliable production safety, and low operating costs. Through the adit, ore can be directly transported to the surface, reducing the hoisting process and improving transportation efficiency. In a certain mine in Sichuan, the ore body is located on a hillside, and adit development is adopted. The ore is directly transported to the concentrator through the adit, greatly reducing transportation costs and ensuring production safety.
In terms of geological conditions, rock properties play a key role. The hardness, stability, and degree of joint development of rocks will affect the construction difficulty and maintenance cost of access roadways. For rocks with high hardness and good stability, the excavation of vertical shafts and inclined shafts is relatively easy, and the maintenance cost of the shafts is relatively low; conversely, if the rocks are fragmented and jointed, collapses and other safety accidents are likely to occur during excavation. In this case, choosing vertical shaft development may be more appropriate, because vertical shafts have better pressure resistance and stability compared to inclined shafts when dealing with complex geological conditions. For example, in some mines with quicksand, faults, fractured zones, and strong aquifers, vertical shaft development can better ensure construction safety and the continuous progress of production.
(2) Guiding Role of Ore Body Occurrence
The occurrence conditions of the ore body are like a compass, guiding the direction of the selection of access roadway types. The depth of the ore body is an important factor. When the ore body is buried deep, vertical shaft development is often more advantageous. Vertical shafts have a large hoisting capacity, can meet the needs of deep ore body mining, and have relatively high safety and stability in deep mining. For example, in some gold mines in South Africa, the ore bodies are several kilometers deep, and vertical shaft development is used to effectively achieve the mining and hoisting of deep ore.
The shape and strike of the ore body also have an important impact on the type of access roadway. For vein-type deposits, if the ore body strike is relatively regular and adapts to the topographic conditions, adit development or along-vein inclined shaft development may be a better choice; for massive deposits, it is usually necessary to comprehensively consider various factors and choose the type of access roadway that can achieve efficient mining and transportation. When the ore body dip angle is greater than 45° or less than 15°, vertical shaft development is more common; when the ore body dip angle is between 15° and 45°, inclined shaft development is more applicable. For example, in a certain lead-zinc mine, the ore body dip angle is 30°, and inclined shaft development is adopted to achieve the smooth mining and transportation of ore.
II. Development Process of Access Roadway Type Selection
(1) Early Stage: Widespread Application of Inclined Shaft Development
In the early stages of the development of the mining industry, due to limitations in the degree of mechanization and technical level, the technical equipment required for excavating inclined shafts was relatively simple, and the construction technology requirements were lower than those for vertical shafts. This led to the widespread application of inclined shaft development in small and medium-sized mines. Inclined shaft development has the advantages of low initial investment and simple ground layout. For small and medium-sized mines with relatively small resource reserves and limited funds, it is an economical and feasible choice. At that time, manual labor and simple mechanical equipment could be used for inclined shaft excavation. Although the excavation speed was slow, it could meet the mining needs of small and medium-sized mines. A small lead-zinc mine used inclined shaft development in its early mining operations, using simple winches to hoist ore and transporting it to the surface through the inclined shaft, achieving the initial development of the mine. However, inclined shaft development also has some limitations, such as limited hoisting capacity and low transportation efficiency. As the mining scale expands and technology develops, these limitations gradually become apparent.
(2) Mid-term: Rise of Vertical Shaft Development
With the continuous improvement of mechanization and construction technology, vertical shaft development gradually emerged and became widely used. Vertical shafts have a large hoisting capacity, can meet the needs of large-scale mine mining, and their hoisting containers run at high speeds, which can greatly improve the efficiency of ore hoisting. At the same time, vertical shafts have obvious advantages in terms of safety, especially in deep mining, where vertical shafts are more stable and can effectively reduce safety risks during mining. In some large metal mines, such as copper mines and iron mines, as the mining depth increases and the mining scale expands, vertical shaft development has become the mainstream choice. Vertical shaft development requires a higher level of technology and more advanced equipment, such as large drilling rigs and hoists. The application of these equipment has significantly improved the excavation speed and construction quality of vertical shafts. The construction cost of vertical shaft development is relatively high, and the construction difficulty is also relatively large, but its advantages in hoisting capacity and safety make it irreplaceable in large mines and deep mining.
(3) Recent: Innovation and Development of Inclined Shaft Transportation Technology
In recent years, significant innovations and developments have been made in inclined shaft transportation technology, particularly with the use of conveyor belts and new skip systems, bringing new vitality to inclined shaft development. The application of conveyor belts in inclined shafts has enabled continuous ore transportation, significantly improving transportation efficiency. Compared to traditional skip hoisting, conveyor belts offer greater transport capacity, stable operation, and low energy consumption, making them suitable for the production needs of large-scale mines. The emergence of new skip systems has further enhanced the hoisting capacity of inclined shafts; their high degree of automated loading and unloading reduces manual operation, improving production efficiency and safety. A large coal mine using inclined shaft development installed high-powered conveyor belts in the inclined shaft, achieving continuous coal transportation, significantly increasing annual transportation volume while reducing transportation costs. The innovation in inclined shaft transportation technology has enabled inclined shaft development, under certain conditions, to rival vertical shaft development, even exhibiting unique advantages in some aspects, providing more possibilities for the selection of mine development roadway types.
III. Analysis of the Current Application Status of Development Roadway Types
(I) Domestic: A Site-Specific Selection Strategy
In China, the selection of development roadway types strictly follows a site-specific strategy. For vein-type deposits or the upper parts of deposits located above the ground level, adit development is widely used due to its unique advantages. Taking a lead-zinc mine in Yunnan as an example, the ore body is located in a mountainous area, above ground level. Adit development is used, directly transporting ore to the surface via the adit. This not only shortens the transportation distance and reduces transportation costs but also reduces investment in hoisting equipment, improving production efficiency. Adit development utilizes natural terrain conditions, enabling self-flowing ore transportation, reducing energy consumption, and providing good ventilation conditions to ensure the safety of underground personnel.
However, when the mine surface is hilly or relatively flat, and the deposit is located below ground level, vertical shaft development becomes the mainstream choice. A large iron mine in Liaoning, due to its deep ore body and relatively flat terrain, uses vertical shaft development. The vertical shaft uses a multi-rope friction hoisting system with high hoisting capacity, meeting the needs of large-scale mining. Vertical shaft development has advantages such as good stability and fast hoisting speed in deep mining, effectively hoisting deep ore to the surface and ensuring efficient mine production.
(II) International: The Auxiliary Role of Inclined Ramps
Domestically and internationally, there are few mines that use inclined ramps as the primary development roadway. Inclined ramps more often play an auxiliary role. This is mainly because inclined ramp development has some limitations. Inclined ramps require significant engineering; compared to vertical shafts of the same depth, the engineering volume is 3-6 times greater, meaning more manpower, material resources, and time are needed for construction. The development depth is constrained by excavation construction technology and economic factors. Currently, the climbing ability of trackless vehicles is generally below 20%, limiting the depth of inclined ramps. When the depth exceeds 200 meters, transportation costs are high. Trackless vehicles require high initial investment, significant maintenance, and high technical requirements. Currently, they mainly use diesel power, causing underground air pollution and increasing mine ventilation costs.
As auxiliary development roadways, inclined ramps have two common applications. In mines using vertical shaft development methods, inclined ramps are used for trackless vehicles to enter and exit the underground, transporting personnel, materials, and equipment, and also serving as ventilation passages, facilitating the operation of trackless equipment and the transportation of personnel and materials. In mines where trackless vehicles are frequently used, auxiliary inclined ramps will be set up between stages for vehicles to move work locations and serve as pedestrian, material transport, and ventilation passages, improving the flexibility and efficiency of mine production. For example, some mines in Australia, while using vertical shaft development, set up auxiliary inclined ramps, enabling efficient operation of trackless equipment and convenient transportation of personnel and materials, improving the overall production capacity of the mine.
IV. Summary
The selection of the main development roadway type is a complex and crucial task, closely related to the mine's topography, geological conditions, and ore body conditions. From a developmental perspective, early on, due to technological limitations, inclined shaft development was widely used in small and medium-sized mines. With technological advancements, vertical shaft development, with its high hoisting capacity and safety advantages, has become dominant in large-scale mines and deep mining. Recent innovations in inclined shaft transportation technology have brought new development opportunities for inclined shaft development. In terms of current applications, China uses adit development and vertical shaft development based on the location of the ore deposit; internationally, inclined ramps mainly serve as auxiliary development roadways.
Note: Part of the article refers to the courseware of "Underground Mining of Metal Deposits" by Xu Shuai and An Long from Northeastern University's online course.
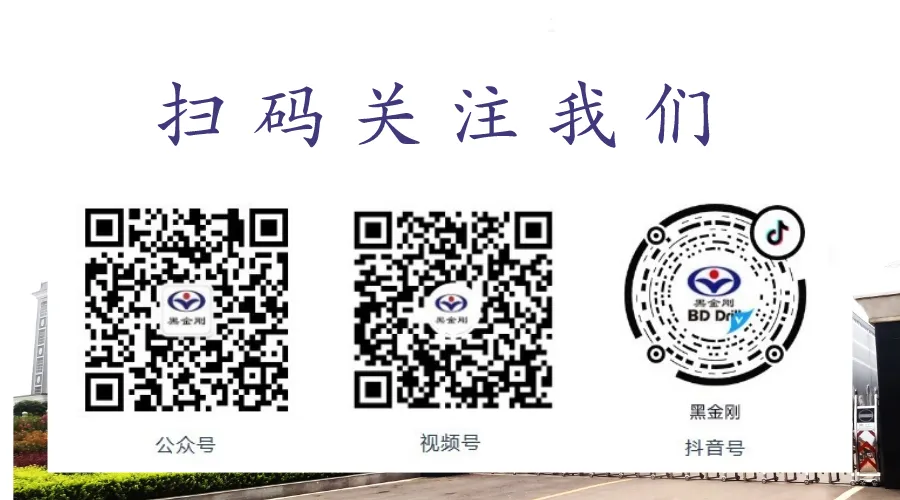
Previous Page