
Coal mine shaft (well) type - Black King Kong broadcast
I. Introduction
In the field of mining engineering, shafts (tunnels) serve as crucial passageways connecting underground mining areas with the surface, their importance is self-evident. They are not only key routes for transporting personnel, equipment, materials, and mineral resources such as coal, but also undertake multiple important tasks in maintaining normal mine production, such as ventilation, drainage, and power supply, making them the "lifeline" of mine production. The choice of shaft (tunnel) type directly affects the cost of mine construction, the difficulty of construction, the length of the construction period, and the safety, efficiency, and economy of subsequent production and operation. From the perspective of construction costs, the differences in costs for excavation, support, and equipment are significant for different types of shafts (tunnels); in terms of construction difficulty, complex geological conditions may make the construction of certain shaft types extremely challenging; in terms of construction period, choosing a reasonable type can effectively shorten the construction period and quickly achieve mine production; and in the production and operation stage, a suitable shaft (tunnel) type can ensure stable and safe production, reduce operating costs, and improve production efficiency. Therefore, in-depth exploration of the selection of shaft (tunnel) types is of vital significance to the development of mining engineering.
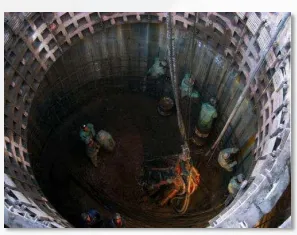
(Image from MOOC China University of Mining and Technology Mining Engineering Tu Shihao, Fang Zhijun, Zheng Xigui, Wang Xufeng, Peng Hongge, Yuan Yong)
II. Vertical Shaft
(I) Structure and Use of Vertical Shafts
As the "lifeline" connecting the mine production level and the ground industrial site, the vertical shaft plays a core role in the entire mine production system. Most vertical shafts in China's coal mines adopt a circular cross-section, which is based on considerations of multiple factors. From a mechanical point of view, the circular cross-section can evenly distribute the ground pressure, and compared to other shapes, it can withstand greater pressure, thus ensuring the stability of the shaft under complex geological conditions. During construction, the circular cross-section facilitates the use of standardized construction equipment and processes. Whether it is drilling and blasting, support operations, or subsequent shaft equipment installation, it can be carried out more efficiently, which helps to improve construction speed and quality. From a maintenance perspective, the circular cross-section does not have stress concentration points, reducing the probability of problems such as well wall cracking and deformation, and reducing maintenance costs and difficulty.
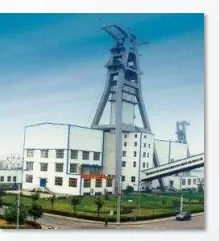
(Image from MOOC China University of Mining and Technology Mining Engineering Tu Shihao, Fang Zhijun, Zheng Xigui, Wang Xufeng, Peng Hongge, Yuan Yong)
According to different uses, vertical shafts can be divided into main shafts, auxiliary shafts, and ventilation shafts, each with its unique and indispensable mission. The main shaft mainly undertakes the heavy responsibility of coal hoisting. The coal mined underground is transported to the loading chamber and coal bin at the bottom of the main shaft through a series of transportation equipment, and then hoisted to the ground using the skip installed in the main shaft, realizing efficient transportation of coal from underground to the ground. The auxiliary shaft is like the "logistics support channel" of the mine, mainly responsible for transporting personnel, materials, and equipment. Personnel travel safely between the ground and underground in cages equipped with reliable safety devices such as fall arresters; various large-scale mining and excavation equipment, support materials, and small tools and materials are also transported to various work sites underground through the auxiliary shaft, providing material support for the normal production of the mine. At the same time, the auxiliary shaft is also an important part of the mine ventilation system and can be used as an intake shaft to transport fresh air from the ground to various operating areas underground, providing sufficient oxygen for underground personnel and maintaining normal production activities. The main function of the ventilation shaft is ventilation, specifically used to transport fresh air underground and exhaust the polluted air produced underground to the ground. In high-gas mines, effective ventilation of the ventilation shaft is crucial; it can control the gas concentration within a safe range, prevent serious accidents such as gas explosions, and ensure the safe production of the mine. In addition, the ventilation shaft can also adjust the temperature and humidity underground, creating a relatively comfortable working environment for the staff.
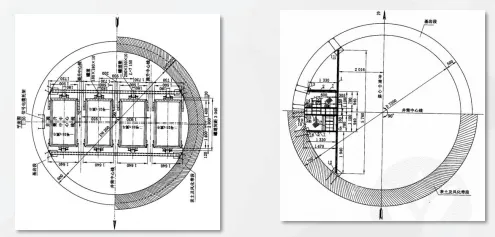
(Image from MOOC China University of Mining and Technology Mining Engineering Tu Shihao, Fang Zhijun, Zheng Xigui, Wang Xufeng, Peng Hongge, Yuan Yong)
(II) Advantages and Disadvantages of Vertical Shafts
Vertical shafts have significant advantages in mining engineering. In terms of hoisting efficiency, because the vertical shaft is relatively short, the hoisting container travels a shorter distance in the shaft, allowing for rapid hoisting. Especially in deep mining, the advantage of fast hoisting speed is more prominent, which can greatly improve the hoisting efficiency of coal and other mineral resources, reduce hoisting time, and thus increase mine output. Taking a deep coal mine as an example, using the vertical shaft hoisting method, the hoisting speed of coal has been significantly improved compared to other shaft types, and the daily output of the mine has also increased significantly. Vertical shafts have a high degree of mechanization and are easy to achieve automated control, which not only improves the safety and stability of hoisting but also reduces errors and risks caused by manual operation. In terms of ventilation, the shaft cross-section of a vertical shaft is larger, the ventilation resistance is small, and it can meet the ventilation requirements of large air volumes. For mines with high gas content and strict ventilation requirements, the ventilation advantages of vertical shafts can ensure the stable operation of the underground ventilation system, effectively dilute and discharge harmful gases, and ensure the safety of underground personnel. Moreover, vertical shafts are highly adaptable to geological conditions. Whether facing complex geological structures such as faults and folds, or different coal seam conditions such as changes in coal seam dip and thickness, vertical shafts can reliably construct and operate with their strong structure and mature construction technology.
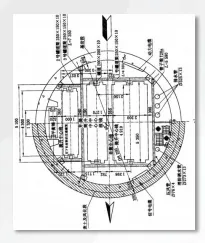
(Image from MOOC China University of Mining and Technology Mining Engineering Tu Shihao, Fang Zhijun, Zheng Xigui, Wang Xufeng, Peng Hongge, Yuan Yong)
However, vertical shafts also have some obvious disadvantages. Shaft construction is a complex and challenging project that requires a high level of technology and a large amount of advanced equipment. During construction, a series of operations such as precise measurement, drilling, blasting, and support are required. Any problem in any link may affect the progress and quality of the entire project. Moreover, the construction speed of vertical shafts is relatively slow, mainly because the construction process is complex, the construction quality needs to be strictly controlled, and various unexpected geological conditions, such as water inrush and rock fragmentation, need to be dealt with during construction, which increases the difficulty and time cost of construction. The infrastructure investment of vertical shafts is large, which is not only reflected in the cost of shaft excavation but also includes the cost of shaft equipment. Vertical shafts need to be equipped with hoisting equipment, ventilation equipment, drainage equipment, and a series of advanced equipment. The procurement, installation, and commissioning of these equipment require a large amount of capital investment. In addition, it is difficult to deepen the vertical shaft. When the mine needs to carry out deep mining and needs to deepen the shaft, due to the complex construction environment and limited construction space of the vertical shaft, many technical problems need to be overcome during the deepening process, such as how to ensure the stability of the shaft during deepening and how to solve ventilation and drainage problems, which increase the difficulty and cost of shaft deepening.
(III) Applicable Scenarios of Vertical Shafts
Vertical shafts have irreplaceable advantages under specific geological conditions. When coal seams are deeply buried, using vertical shafts can reduce the length of the shaft, lowering the difficulty and cost of coal hoisting. In some deep coal mine extractions, due to the significant depth of the coal seams, if inclined shafts are used, the shaft length will increase significantly, not only increasing construction costs but also reducing hoisting efficiency. Using vertical shafts can effectively shorten the shaft length, improving hoisting speed and efficiency. When the topsoil layer is thick or hydrological conditions are complex, the stability and adaptability of vertical shafts are better utilized. In areas with thicker topsoil layers, vertical shafts can pass through unstable topsoil layers using special construction methods such as freezing methods and drilling methods, ensuring safe shaft construction. For areas with complex hydrological conditions, such as high groundwater levels and large water inflow, vertical shafts can better perform drainage and waterproofing, ensuring normal mine production. When the extraction of coal seams is limited by dip angle, thickness, gas, and hydrological conditions, vertical shafts are also a more suitable choice. For steeply inclined coal seams, using vertical shafts can more easily arrange the extraction system, improving coal extraction efficiency; for coal seams with high gas content, the good ventilation performance of vertical shafts can effectively reduce gas concentration, ensuring safe production; for coal seams significantly affected by hydrological conditions, the drainage capacity of vertical shafts can ensure that extraction is not threatened by water damage.
III. Inclined Shafts
(I) Characteristics and Classification of Inclined Shafts
An inclined shaft is a shaft excavated downward from the ground at an angle, directly connected to the ground. Its function is the same as that of a vertical shaft and a horizontal adit. An inclined shaft that is not directly connected to the ground is called a blind inclined shaft. The slope of the inclined shaft is not arbitrarily determined but has strict range requirements, generally between 8° and 35°. This slope range is determined after comprehensively considering various factors, ensuring that vehicles and equipment can operate relatively safely and stably during construction and operation, while also controlling construction difficulty and cost to a certain extent. If the slope is too small, it will increase the length of the shaft, not only increasing construction costs but also potentially affecting transportation efficiency; if the slope is too large, it will put a greater load on the transportation equipment, increasing safety risks and posing a threat to personnel and equipment safety.
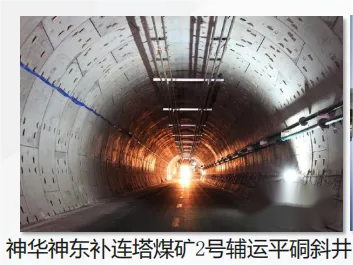
(Image from MOOC China University of Mining and Technology Mining Engineering Tu Shihao, Fang Zhijun, Zheng Xigui, Wang Xufeng, Peng Hongge, Yuan Yong)
According to different uses, inclined shafts are mainly divided into main inclined shafts, auxiliary inclined shafts, and return air inclined shafts. The main inclined shaft is responsible for transporting coal and is the key channel for transporting coal from underground to the ground. It usually has conveyor belts and other conveying equipment installed inside, enabling continuous coal transportation and significantly improving transportation efficiency. In some large coal mines, advanced belt conveyors are used in the main inclined shafts, with strong transportation capacity to meet the needs of large-scale mine production. Auxiliary inclined shafts are mainly used for transporting personnel and materials, serving as an important channel for material transportation in mining production. They also serve as intake shafts, supplying fresh air underground. Personnel use special personnel vehicles or other transportation tools to safely go up and down the shaft through the auxiliary inclined shaft, and various equipment and materials are also transported to various work sites underground through the auxiliary inclined shaft. The main function of the return air inclined shaft is to extract airflows from the entire mine or a mining area and multiple mining areas, discharging the polluted air produced underground to the ground, ensuring that the underground air quality meets safety standards and creating a good working environment for miners. In some high-gas mines, the ventilation capacity of the return air inclined shaft is directly related to the safe production of the mine, and its ventilation must be smooth to promptly discharge harmful gases such as methane.
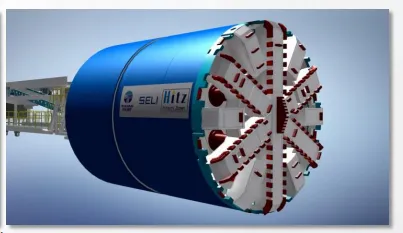
(Image from MOOC China University of Mining and Technology Mining Engineering Tu Shihao, Fang Zhijun, Zheng Xigui, Wang Xufeng, Peng Hongge, Yuan Yong)
(II) Advantages and Limitations of Inclined Shafts
Inclined shafts have many advantages in mining. From a construction perspective, the construction process of inclined shafts is relatively simple, and the required equipment and processes are not as complex as those of vertical shafts. During construction, complex vertical hoisting operations are not required as in vertical shafts, and the entry and exit of construction personnel and equipment are relatively convenient, making the excavation speed of inclined shafts relatively fast. Moreover, the excavation unit price of inclined shafts is usually lower, which can reduce construction costs to a certain extent. Considering ground facilities and equipment, the ground facilities and equipment of inclined shafts are relatively simple and do not require large hoisting equipment and complex derricks as in vertical shafts. This not only reduces equipment procurement and installation costs but also reduces equipment maintenance difficulty and cost. In terms of bottom-of-shaft yard facilities and equipment, inclined shafts are also relatively simple and do not require complex bottom-of-shaft yards as in vertical shafts, further reducing construction costs. In addition, inclined shafts have advantages in extension. When a mine needs deep mining, the extension of an inclined shaft is relatively convenient, with less interference to the existing production system, allowing for shaft extension without or with minimal impact on normal production. Main inclined shafts using belt conveyors perform exceptionally well in terms of transportation capacity, with large transportation capacity and no length limitations, meeting the coal transportation needs of large-scale mine production. In terms of initial investment, inclined shafts have obvious advantages over vertical shafts. Due to their simple construction process and relatively simple ground facilities and equipment, the initial investment of inclined shafts is less, which is very attractive to some mining enterprises with relatively tight funds.
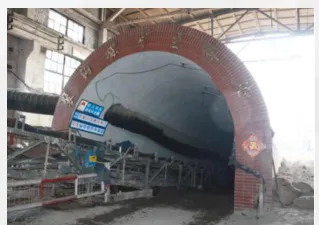
(Image from MOOC China University of Mining and Technology Mining Engineering Tu Shihao, Fang Zhijun, Zheng Xigui, Wang Xufeng, Peng Hongge, Yuan Yong)
However, inclined shafts also have some limitations. Due to the longer shaft body of inclined shafts, the hoisting capacity of winches (conveyor systems) will be limited. When using winches (conveyor systems) for hoisting, the amount of coal or materials hoisted at one time is limited, and the hoisting process is intermittent, which limits the hoisting capacity and cannot meet the needs of large-scale and high-efficiency transportation. As the shaft body of the inclined shaft extends, various pipelines through the shaft will also become longer, not only increasing the cost of pipeline laying but also leading to increased production and operation costs for ventilation, power supply, and drainage. In terms of ventilation, long-distance inclined shafts will increase ventilation resistance and reduce ventilation efficiency, requiring more ventilation equipment and energy to ensure underground ventilation needs; in terms of power supply, long pipelines will lead to increased energy loss, requiring higher supply voltage or additional power supply equipment to ensure stable power supply; in terms of drainage, long-distance drainage requires higher-power drainage equipment and higher energy consumption. The maintenance workload of inclined shaft shafts is large. Due to the relatively large ground pressure and friction force on the shaft walls of inclined shafts, problems such as shaft wall cracking and deformation are prone to occur, requiring regular maintenance and reinforcement, which increases maintenance costs and workload. Inclined shafts have poor adaptability to geological conditions. When encountering complex geological structures such as faults and quicksand layers, the construction and maintenance difficulty of inclined shafts will greatly increase, and construction may even be impossible, requiring special construction methods or changes in shaft form.
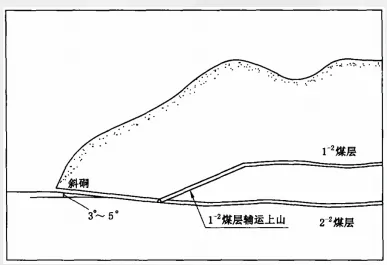
(Image from MOOC China University of Mining and Technology Mining Engineering Tu Shihao, Fang Zhijun, Zheng Xigui, Wang Xufeng, Peng Hongge, Yuan Yong)
(III) Applicable Conditions for Inclined Shafts
In specific geological conditions and mine scales, inclined shafts exhibit good applicability. Inclined shafts are widely suitable for large, medium, and small mines, and can be reasonably designed and arranged according to the needs of mines of different scales. For mines with shallow coal seams, the use of inclined shafts can fully utilize the advantages of shallow coal seams, reduce the excavation depth of the shaft, and lower construction costs. When the topsoil layer is not thick and the hydrogeological conditions are simple, the construction difficulty and risk of inclined shafts are relatively small, and construction and operation can proceed smoothly. In this case, special construction methods are not needed to pass through complex topsoil layers or deal with complex hydrogeological conditions, reducing construction costs and risks. For mines with gently sloping and inclined coal seams, the slope and strike of the inclined shaft can adapt to the occurrence conditions of the coal seam, facilitating the layout of the underground transportation system and mining roadways, and improving coal mining efficiency. In terms of the inclined length of the mining area, if belt conveyors are used for transportation, the length of the inclined shaft can be relatively long to meet the needs of long-distance transportation; however, if a skip hoist is used, to ensure hoisting efficiency and safety, the inclined length of the mining area should not exceed three hoisting sections, otherwise it will increase the difficulty and cost of hoisting, and reduce transportation efficiency.
IV. Adit
(1) Adit Development System
The adit development system demonstrates unique advantages in mining engineering. Its system is simple and construction is convenient, which stems from various reasons. From a construction process perspective, adit excavation is mainly carried out horizontally. Compared to the vertical downward construction of vertical shafts and the inclined construction of inclined shafts, the adit construction process does not require complex vertical hoisting equipment and inclined transportation equipment. Construction personnel and equipment can enter and exit the working face more conveniently, greatly reducing construction difficulty and risk. During construction, adit surveying and orientation are relatively simple, allowing for more accurate control of the excavation direction and slope of the roadway, improving construction accuracy. Moreover, the impact on the surrounding environment during adit construction is relatively small, and the layout of the construction site is more flexible. It does not require large-scale leveling and transformation of the ground, unlike vertical shafts and inclined shafts, to meet the layout requirements of hoisting equipment and wellhead facilities.
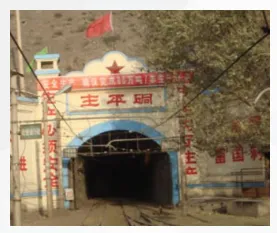
(Image from MOOC China University of Mining and Technology Mining Engineering Tu Shihao, Fang Zhijun, Zheng Xigui, Wang Xufeng, Peng Hongge, Yuan Yong)
Adits have obvious advantages in drainage; their drainage system is relatively simple. Because adits usually maintain a 3° - 5° outward slope, under the action of gravity, the underground water can naturally flow out along the ditches in the adit. Unlike vertical shafts and inclined shafts, it does not require complex drainage equipment and large water tanks. In some mines that use adit development, underground water flows naturally to the sedimentation pool on the ground through ditches, and after simple treatment, it can meet the standards for discharge. This not only saves the purchase, installation, and operation costs of drainage equipment, but also reduces the risk of water damage caused by drainage equipment failure. Moreover, the self-flowing drainage method is more energy-efficient and environmentally friendly, in line with the concept of sustainable development of modern mines.
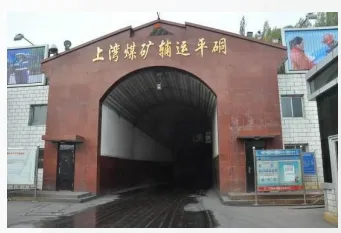
(Image from MOOC China University of Mining and Technology Mining Engineering Tu Shihao, Fang Zhijun, Zheng Xigui, Wang Xufeng, Peng Hongge, Yuan Yong)
Adit development does not require the setting up of a bottom-of-shaft yard, which is one of its important characteristics that distinguishes it from vertical shaft and inclined shaft development. The bottom-of-shaft yard is generally a group of roadways and chambers connecting the shaft and the main transportation roadways underground. It is the hub for underground transportation and shunting, and also the center for personnel access and material and equipment transfer. However, setting up a bottom-of-shaft yard requires a large amount of roadway excavation and chamber construction, which not only increases the complexity and construction cost of the project, but may also affect the efficiency of underground transportation due to unreasonable layout of the bottom-of-shaft yard. Adit development directly uses the adit as a transportation passage, reducing transportation links and equipment, making the underground transportation system simpler and more efficient. Coal or other ores mined underground can be transported directly from the working face to the ground via the adit using transportation equipment such as mine cars or belt conveyors, greatly improving transportation efficiency and reducing transportation costs.
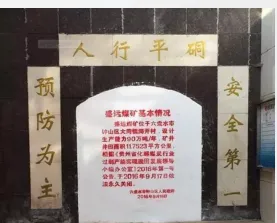
(Image from MOOC China University of Mining and Technology Mining Engineering Tu Shihao, Fang Zhijun, Zheng Xigui, Wang Xufeng, Peng Hongge, Yuan Yong)
(2) Unique Advantages of Adits
Adits have significant advantages in transportation, which is one of the important reasons for their widespread use in mining engineering. In mines using adit development, underground coal transportation can be directly transported out via the adit without transshipment. In some coal mines, coal mined from the underground coal mining face is directly transported to the main adit via scrapers and belt conveyors, and then transported to the coal preparation plant or coal storage area on the ground via belt conveyors or mine cars in the adit. This direct transportation method reduces the number of times coal is transshipped underground, avoiding problems such as coal spillage and accumulation that may occur during transshipment. This not only improves transportation efficiency but also reduces coal loss and wear and tear on transportation equipment. Moreover, reducing transportation links and equipment makes the transportation system simpler and more reliable, reducing equipment maintenance costs and failure rates, and improving the stability of mine production.
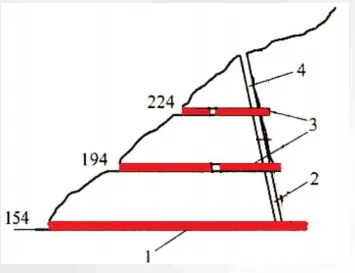
(Image from MOOC China University of Mining and Technology Mining Engineering Tu Shihao, Fang Zhijun, Zheng Xigui, Wang Xufeng, Peng Hongge, Yuan Yong)
The surface industrial facilities of adits are relatively simple, which is another prominent advantage compared to vertical shaft and inclined shaft development. Because adits do not need to set up tall and complex derricks, hoisting houses, and other hoisting equipment facilities like vertical shafts, nor do they need to set up special inclined shaft wellhead facilities and ground hoisting equipment like inclined shafts, the ground industrial facilities of adits mainly include the adit entrance bridge, receiving coal pit, belt conveyor corridor, etc. These facilities have simple structures and low construction costs. In some small mines, the ground facilities at the adit entrance only require a simple bridge and receiving coal pit to achieve rapid transfer and storage of coal, greatly reducing the initial investment in mine construction. Moreover, simple ground industrial facilities occupy a small area, have strong adaptability to terrain, and can be more flexibly arranged in mountainous or hilly areas with complex terrain, reducing land resource occupation and impact on the surrounding environment.
Adit development does not require leaving industrial square protection coal pillars, which to a certain extent improves the recovery rate of coal resources. In vertical shaft and inclined shaft development, in order to protect the safety of buildings and hoisting equipment in the industrial square, it is necessary to leave a certain range of protection coal pillars around the shaft. These protection coal pillars cannot be mined during mine production, resulting in the permanent loss of a large amount of coal resources. Because the ground facilities of adit development are simple and have a small impact on underground coal resources, large-scale protection coal pillars do not need to be left, thus reducing the waste of coal resources and improving the economic benefits of the mine. In areas with scarce coal resources, the use of adit development can maximize the recovery of coal resources, extend the service life of the mine, and is of great significance to ensuring energy supply and promoting regional economic development.
Adits have obvious advantages in terms of drainage costs. Because adits use self-flowing drainage, they do not need to set up high-power drainage equipment and large water tanks, nor do they need to consume a large amount of electricity for drainage operations, which greatly reduces the drainage costs of adits. In some mines with large water inflow, when using vertical shaft or inclined shaft development, the annual drainage costs may be as high as millions of yuan, while after using adit development, drainage costs can be reduced by more than 80%. Moreover, the self-flowing drainage method is more stable and reliable, reducing the risk of water damage caused by drainage equipment failure and ensuring safe mine production. The reduction in drainage costs directly reduces the production costs of the mine and improves the market competitiveness of the mine.
(3) Terrain Suitable for Adits
In mountainous and hilly areas, flat-entry development has unparalleled advantages and should be prioritized. These areas have significant topographic variations and relatively complex coal seam conditions, but they also offer favorable conditions for flat-entry development. In mountainous areas, due to the presence of mountains, flat entries can be directly excavated from one side of the mountain into the coal seam, eliminating the need for large-scale shaft excavation and surface infrastructure construction. Moreover, mountainous areas have significant elevation differences, allowing flat entries to utilize these differences for gravity drainage, further reducing drainage costs. In some mountain coal mines, flat entries are excavated from the mountainside into the coal seam, and underground water flows naturally through the flat entry to rivers or settling ponds at the foot of the mountain, achieving rational utilization of water resources and sustainable development of the mine.
In hilly areas, although the topographic variations are relatively small, appropriate flat entry locations and directions can still be selected through reasonable planning and design. Coal seams in hilly areas are often shallowly buried, and flat-entry development can fully utilize this advantage to reduce shaft excavation depth and construction costs. Moreover, hilly areas have relatively good transportation conditions, which are conducive to mine material transportation and product sales. In some small mines in hilly areas, flat-entry development not only has low construction costs but also allows for rapid production, making significant contributions to local economic development.
In mountainous and hilly areas, as long as the coal reserves in the uphill section meet the service life of similar well types, flat-entry development should be prioritized. This is because flat-entry development not only has advantages such as low construction costs, fast construction speed, high transportation efficiency, and low drainage costs, but it can also better adapt to the terrain and geological conditions of these areas, reducing environmental impact. Moreover, flat-entry development is conducive to the sustainable development of mines, improves the recovery rate of coal resources, reduces energy consumption and environmental pollution, and conforms to the trend of modern mine development.
V. Selection Principles
(1) Combining Surface Topography
Surface topography is one of the key factors to consider when selecting shaft (entry) types, and different topographic types have significantly different adaptability to shaft (entry) types. In mountainous terrain, flat-entry development often has unique advantages. Mountainous areas have significant topographic variations, and coal seams are usually buried within the mountains. Flat entries can cleverly utilize the mountain's topography, excavating directly into the coal seam from one side of the mountain, avoiding large-scale shaft excavation and surface infrastructure construction. In some mountain coal mines, flat entries cut into the coal seam from the mountainside, and coal can be transported directly to the surface through the flat entry, greatly reducing transportation links and costs. Moreover, flat-entry development in mountainous areas can fully utilize topographic differences to achieve gravity drainage, reducing the investment and operating costs of drainage equipment.
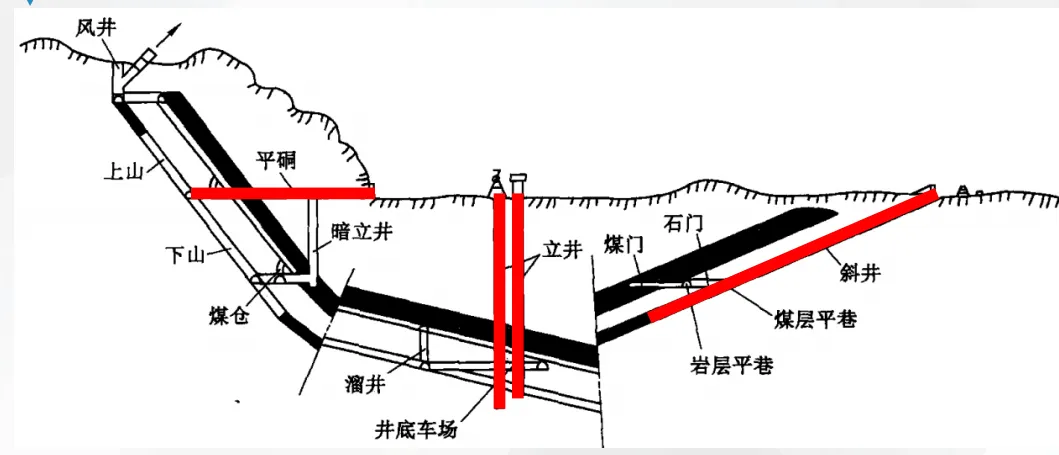
(Image from MOOC China University of Mining and Technology Mining Engineering Tu Shihao, Fang Zhijun, Zheng Xigui, Wang Xufeng, Peng Hongge, Yuan Yong)
In plain areas, due to the relatively flat terrain and lack of natural elevation differences to utilize, the advantages of flat-entry development are difficult to exploit. In this case, vertical shaft and inclined shaft development are more common. Vertical shaft development in plain areas can effectively exploit deep coal resources due to its wide adaptability to geological conditions and strong hoisting capacity. In some large coal mines in plain areas, due to the deep burial of coal seams, vertical shaft development can ensure efficient coal hoisting and transportation. Inclined shaft development also has certain applications in plain areas, especially when coal seams are shallowly buried, the topsoil layer is thin, and hydrogeological conditions are simple. Inclined shaft development can achieve cost-effective mining through reasonable design and layout. In some small coal mines, inclined shaft development has relatively simple construction processes and low initial investment, allowing for rapid coal mining and sales.
(2) Considering Coal Seam Conditions
Coal seam conditions play a decisive role in the selection of shaft (entry) types, with coal seam depth, thickness, and dip angle being particularly crucial. When the coal seam is deep, vertical shaft development is usually the preferred option. Vertical shafts are relatively short, reducing the distance and time for coal hoisting and improving hoisting efficiency. In deep coal mine mining, the rapid hoisting capacity of vertical shafts ensures timely coal transportation to the surface to meet production needs. Moreover, vertical shafts are more adaptable to complex deep geological conditions, ensuring shaft stability and safety.
Coal seam thickness also affects the choice of shaft (entry) type. For thick coal seams, it is necessary to consider how to efficiently mine and transport coal. If the coal seam is thick, inclined shaft development may require special hoisting equipment and transportation methods to meet coal transportation needs. In the mining of some thick coal seams, vertical shaft development can achieve efficient coal mining and transportation through reasonable shaft layout and hoisting equipment selection. In the mining of some extra-thick coal seams, vertical shaft development combined with fully mechanized mining and top coal caving technology can fully utilize the advantages of the large hoisting capacity of vertical shafts, improving the recovery rate of coal resources.
Coal seam dip angle is also an important factor to consider when selecting shaft (entry) types. For gently inclined coal seams, inclined shaft development has certain advantages. The slope of the inclined shaft can adapt to the coal seam dip angle, facilitating the layout of underground transportation systems and mining roadways, improving coal mining efficiency. In some coal mines with gently inclined coal seams, inclined shaft development can use continuous transportation equipment such as belt conveyors to achieve efficient coal transportation. For steeply inclined coal seams, vertical shaft development is more suitable. Vertical shafts can better adapt to the mining conditions of steeply inclined coal seams, facilitating the layout of mining systems and hoisting equipment to ensure safe coal mining and transportation.
VI. Comparative Analysis
Comparison Items | Vertical Shaft | Inclined Shaft | Flat Entry |
Construction Difficulty | Complex construction process, requiring professional technology and a large amount of equipment, such as special well-drilling equipment and ventilation equipment, resulting in slow construction speed. For example, when constructing a vertical shaft in a deep and thick topsoil layer, the freezing method is often used, which has a cumbersome construction process and high technical requirements. | The construction process is relatively simple, the equipment and procedures are not complex, and the advancing speed is relatively |
Simple construction, horizontal advancing, good construction conditions, fast advancing speed |
Investment Cost | High infrastructure investment, including shaft excavation, equipment procurement, and installation and commissioning costs. Shaft equipment such as hoisting equipment and ventilation equipment is expensive, and installation costs are high | Low initial investment, ground facilities and simple equipment, bottom hoisting station facilities and equipment are also relatively simple |
Low infrastructure investment, low cost per unit length of advance, low maintenance costs, no bottom hoisting station, simple shaft mouth facilities Operating costs |
Hoisting, drainage, power supply and other production and operation costs are low. Because the shaft is short, various pipelines are short, and energy loss is small. | Ventilation, power | supply, drainage and other production and operation costs are high. The shaft is long, the pipelines are long, and the energy loss is large. Low drainage costs, |
Generally self-flowing drainage, Low transportation costs, Simple system Applicable conditions |
The coal seam is buried deep, the topsoil is thick, or the hydrological conditions are complex, requiring special construction; the mining of coal seams is limited by dip angle, thickness, gas, and hydrological conditions; steeply inclined coal seams for multi-level mining; not suitable for inclined shafts, adits, and comprehensive development methods | Widely applicable to large, medium, and small mines; shallowly buried coal seams; thin topsoil layer, simple hydrogeological conditions, no special construction methods required for gently inclined and inclined coal seams; when using belt conveyors, the inclined length of the mining area can be longer, and the skip hoisting should not exceed three stages | Above the adit elevation | Sufficient reserves of Mountainous areas should be given priority to be used first, applicable to mountainous and hilly areas, the upper part of the mountain coal reserves are sufficient for the same type of well horizontal service life VII. Summary |
The selection of the type of coal mine shaft (adit) is a comprehensive and systematic work that requires consideration of multiple factors. Vertical shafts are suitable for conditions such as deep burial of coal seams, thick topsoil, or complex hydrological conditions. Although the construction is complex and the investment is large, the hoisting speed is fast and the ventilation resistance is small. Inclined shafts have advantages when the coal seams are shallowly buried, the topsoil layer is thin, and the hydrogeological conditions are simple. The construction process is simple and the initial investment is low, but the long shaft body brings challenges in transportation and maintenance. Adit development performs well in mountainous and hilly areas when suitable terrain and reserve conditions are available, with fewer transportation links and low drainage costs. In actual projects, the advantages and disadvantages of various shaft (adit) types should be comprehensively weighed in combination with surface topography, coal seam occurrence conditions, etc., to determine the most suitable scheme and achieve safe, efficient, and economical coal mining.
(This article refers to the courseware of Mining Engineering from China University of Mining and Technology on MOOC, by Tu Shihao, Fang Zhijun, Zheng Xigui, Wang Xufeng, Peng Hongge, and Yuan Yong.)
(文章参考了 慕课中国矿业大学 采矿学 屠世浩、方志军、郑西贵、王旭峰、彭洪阁、袁永的课件)
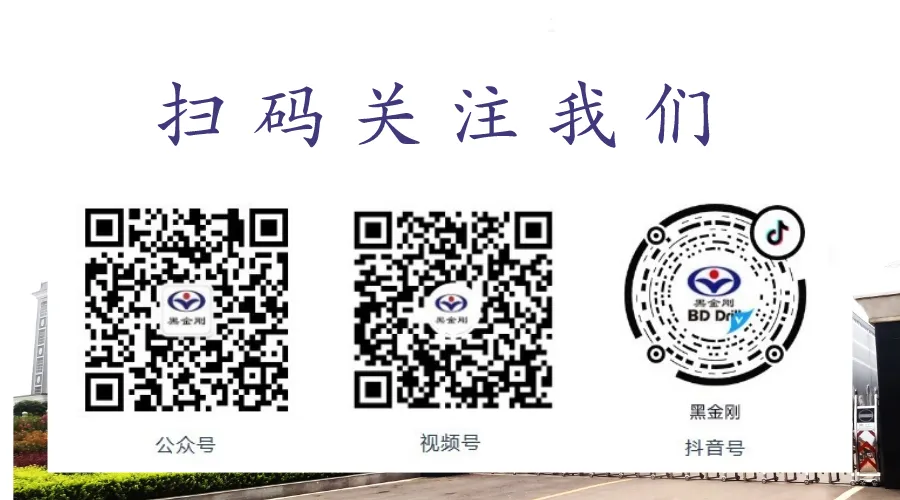
Previous Page