
Underground loading chamber and skip hoisting mining system - Black King Kong report
Introduction
In the mining engineering field, the ore hoisting system is a key link in ensuring the efficient and stable operation of mining operations, playing a decisive role in mining efficiency and cost. An efficient ore hoisting system can significantly improve ore transportation efficiency, reduce production costs, and enhance the economic benefits and market competitiveness of mining enterprises; conversely, if the hoisting system is inefficient or prone to frequent failures, it will not only lead to a significant decline in mining efficiency, but also cause a sharp increase in production costs, resulting in huge losses for the enterprise.
(Image from MOOC Northeastern University Underground Mining of Metal Deposits Xu Shuai, An Long )
The underground loading chamber and its skip hoisting and loading system play a crucial role in the entire ore hoisting system. As a key transfer point for ore transportation from underground to aboveground, the reasonable design and layout of the underground loading chamber, as well as its efficient and stable operation, are important prerequisites for ensuring smooth ore hoisting. The skip hoisting and loading system, as the core equipment for hoisting ore from the underground loading chamber to the ground, its performance directly affects the efficiency and cost of ore hoisting. Therefore, in-depth exploration of the underground loading chamber and its skip hoisting and loading system is of great significance to improving mining efficiency, reducing production costs, and promoting the progress of mining engineering technology.
(Image from MOOC Northeastern University Underground Mining of Metal Deposits Xu Shuai, An Long )
Fundamentals of Skip Hoisting and Loading System
In mining operations, when using skips to hoist ore, the setting of underground ore bins and loading chambers is extremely necessary. They are like key gears in the mining transportation chain, playing a crucial role in the smooth operation of the entire hoisting process. The underground ore bin is mainly used for temporary storage of ore transported from the underground mine, acting like a " reservoir ” ", which can effectively adjust the rhythm difference between ore mining and hoisting. In actual mining processes, the ore output speed of the underground mine is often difficult to keep consistent with the hoisting speed of the skip. With the underground ore bin, when the mine output is large and the skip cannot hoist it in time, the excess ore can be stored in the underground ore bin; when the mine output is small, the ore in the underground ore bin can be replenished in time to ensure the continuity of the skip hoisting operation, avoiding frequent starts and stops of the hoisting equipment due to unstable ore supply, effectively improving equipment operation efficiency, and reducing equipment wear and energy consumption.
(Image from MOOC Northeastern University Underground Mining of Metal Deposits Xu Shuai, An Long )
The loading chamber is the key place for ore transfer from the underground ore bin to the skip. It is equipped with a series of professional loading equipment, and is the " heart ” of the entire hoisting and loading system, precisely controlling the ore loading process, which is of great significance to ensuring the efficiency and safety of skip hoisting and loading. Taking a common large metal mine as an example, when this mine uses skips to hoist ore, the capacity of the underground ore bin is designed to be 5000 cubic meters, which can meet the ore storage needs of the mine for several hours during peak ore output periods. Its loading chamber uses advanced automated loading equipment, and through high-precision sensors and an intelligent control system, it can precisely control the ore loading amount and speed according to the position and capacity of the skip, completing 1000 tons of ore loading per hour, greatly improving ore hoisting efficiency and ensuring high and stable production in the mine.
Loading Characteristics of Different Types of Skips
Tilting Skip
In mining operations, tilting skips are a common type of hoisting container, often using metering hopper loading and fixed-point loading. Metering hopper loading, with its high-precision ore metering function, brings excellent accuracy and stability to the entire loading process. By precisely controlling the amount of ore loaded into the skip, it can not only effectively prevent overloading of the skip due to excessive loading, affecting hoisting safety and equipment life; it can also prevent insufficient loading, resulting in low hoisting efficiency, wasting energy and time costs. Taking a certain metal mine as an example, after using metering hopper loading, the loading error of each skip can be controlled within a very small range, greatly improving the stability and efficiency of hoisting operations.
Fixed-point loading is to load ore precisely into the skip according to a pre-set precise position. This loading method has significant advantages. It ensures that each time ore is loaded, it enters the skip at the same position and posture, effectively avoiding the problem of skip center of gravity offset caused by loading position deviation. Once the skip center of gravity is offset, it is easy to experience shaking and tilting during hoisting, which not only causes additional wear and stress on the hoisting equipment, but may also cause serious safety accidents. Fixed-point loading effectively avoids these risks, providing a strong guarantee for the safe and efficient operation of hoisting operations.
Bottom-Discharging Skip in Multi-Rope Hoisting
In multi-rope hoisting, bottom-discharging skips are widely used, often using metering skip loading. Metering skip loading uses high-precision metering devices on the skip to measure the weight of ore loaded into the skip in real time and accurately during the loading process, achieving precise control of the loading amount. This precise control is of great significance to the multi-rope hoisting system. The multi-rope hoisting system relies on multiple steel wire ropes to jointly bear the weight of the skip and ore. If the loading amount is uneven, the load borne by each steel wire rope will deviate. Under this unbalanced force state for a long time, the wear and tear of the steel wire ropes will increase, and the wear distribution will be uneven, which will not only shorten the service life of the steel wire ropes, increase equipment maintenance costs and replacement frequency, but may also cause breakage due to excessive wear of a certain steel wire rope, leading to serious safety accidents. Metering skip loading effectively avoids this problem. By precisely controlling the loading amount, the force on each steel wire rope is uniform, ensuring the safe and stable operation of the hoisting system. Taking the multi-rope hoisting system of a large coal mine as an example, after using metering skip loading, the average service life of the steel wire ropes has been extended 30% , maintenance costs have been significantly reduced, and the safety and stability of hoisting operations have been significantly improved.
With / Differences in Mine Loading with and without Underground Crushing Stations
With underground crushing stations
For mines with underground crushing stations, the ore loading process is usually more complex and refined. In such mines, electric vibrating feeders or plate feeders are often used as the initial stage of ore transportation. Electric vibrating feeders utilize the principle of electromagnetic vibration to uniformly and efficiently transport ore from the storage location to subsequent equipment. Its vibration frequency and amplitude can be precisely adjusted according to actual production needs, achieving precise control of the feeding rate and ensuring a stable supply of ore. Plate feeders, with their robust and durable chain plate structure, can withstand the weight and impact of larger ore pieces, transporting the ore smoothly. The running speed of its chain plates can also be flexibly adjusted to adapt to different production rhythms.
After being transported by electric vibrating feeders or plate feeders, the ore from the underground crushing station enters the belt conveyor. Belt conveyors, with their advantages of continuous conveying, large conveying capacity, and long conveying distance, are the ideal choice for long-distance ore transportation. Through the cyclical rotation of the conveyor belt, it quickly and efficiently transports the ore to the weighing hopper. During transportation, to ensure stable ore transportation and safe operation of the equipment, a series of auxiliary devices are usually equipped, such as conveyor belt tensioning devices and anti-deviation devices. These devices can adjust the state of the conveyor belt in time, preventing problems such as conveyor belt slackness and deviation, and ensuring smooth ore transportation.
The weighing hopper is a key metering link in the entire ore loading process. It uses advanced high-precision metering equipment such as pressure-magnetic force transducers to measure the weight of the ore entering it in real time and accurately. When the ore weight reaches the set skip loading capacity, the weighing hopper automatically controls the discharging device to accurately load the ore into the skip. This precise metering and loading method not only ensures that the amount of ore loaded in each skip meets the standard, avoiding overloading or underloading, but also effectively improves the efficiency and safety of ore hoisting. Taking a modern large-scale metal mine as an example, its underground crushing station uses an advanced automated ore loading system. The electric vibrating feeder, belt conveyor, and weighing hopper are seamlessly connected through an intelligent control system. The entire ore loading process is efficient and stable, capable of completing hundreds of tons of ore loading and hoisting operations per hour, greatly improving the mine's production capacity.
No underground crushing station
In mines without underground crushing stations, ore loading operations have different considerations and equipment choices. Since there is no underground crushing station to pre-crush the ore, to avoid ore blockage and equipment damage during transportation and loading, belt conveyors are usually avoided as much as possible. This is because belt conveyors have certain requirements for the size and shape of the ore. Larger or irregularly shaped ore may cause scratches and tears in the conveyor belt, or even cause equipment shutdown.
Plate feeders have become the main feeding equipment in this case. They have advantages such as simple structure, reliable operation, and strong adaptability. They can directly transport the ore mined from the mining area to the loading location. Even when facing larger ore pieces, plate feeders can smoothly transport the ore with their sturdy chain plates and powerful driving force, effectively avoiding transportation problems caused by excessively large ore pieces. Moreover, plate feeders are relatively easy to maintain. In the harsh working environment of mines, they can maintain high operational stability, reducing equipment maintenance costs and downtime, and ensuring the continuity of ore loading operations. For example, a small metal mine without an underground crushing station uses a plate feeder to directly transport ore from the mining area to the skip loading location. In years of production practice, the plate feeder has maintained a good operating state. Although the ore pieces are large, through reasonable operation and maintenance, it has successfully ensured the normal production of the mine, creating stable economic benefits for the enterprise.
Case study of a copper mine weighing hopper single skip ore loading system
Taking a copper mine weighing hopper single skip ore loading system as an example, the various components of this system work closely together to ensure efficient ore loading operations. The system diagram clearly shows that the layout of each equipment is compact and reasonable, taking into account both the ore transportation path and ensuring smooth collaborative operation between the equipment.
The gate in the system, as a control point for ore flow, plays a crucial role. It is like a precise flow control valve. By precisely controlling the opening degree, it can effectively control the ore flow rate and flow speed. When ore needs to be transported to the weighing hopper, the operator controls the opening angle of the gate remotely or manually on-site according to production needs, allowing the ore to flow into the weighing hopper at an appropriate speed and quantity. In actual operation, the operator will flexibly adjust the opening time and degree of the gate according to the loading situation of the weighing hopper and the production rhythm, ensuring that the weighing hopper can quickly and accurately complete the loading task. If the weighing hopper is about to be full, the operator will appropriately reduce the opening degree of the gate to prevent ore spillage; while if the ore loading speed of the weighing hopper is slow, the opening degree of the gate will be increased to increase the ore transportation volume.
The electric feeder is the power source for ore transportation. It uniformly and stably transports ore from the ore storage location to the chute through its own vibration or mechanical movement. Its working principle is based on electromagnetic vibration or mechanical transmission, and it can precisely control the feeding amount according to the set frequency and amplitude. In the ore loading system of a certain copper mine, the electric feeder uses advanced electromagnetic vibration technology. By adjusting the current size to change the vibration frequency and amplitude, precise control of the feeding amount is achieved. During the peak season of ore mining, in order to meet production needs, the operator will increase the vibration frequency and amplitude of the electric feeder to increase the feeding amount; while during the off-season or when equipment maintenance is needed, the working intensity of the feeder will be reduced to reduce the feeding amount. This flexible control method not only improves the ore loading efficiency but also reasonably adjusts the equipment operating status according to the actual production situation, reducing energy consumption and equipment wear and tear.
The chute, as a channel for ore transportation, uses gravity to guide the ore to smoothly flow towards the belt conveyor. Its design slope and surface smoothness are carefully calculated and processed to ensure that the ore can slide down quickly and stably under the action of gravity. In the chute design of a certain copper mine, the slope is precisely set to ensure that the ore slides smoothly while preventing the ore from sliding too fast and impacting the equipment. At the same time, the surface of the chute uses special wear-resistant materials to reduce friction between the ore and the chute, reducing chute wear and extending the service life of the equipment. Moreover, to prevent ore blockage in the chute, the width and height of the chute are also reasonably designed according to the maximum size of the ore to ensure that the ore can pass smoothly.
The active chute provides a more flexible path selection for ore transportation. Its angle and position can be adjusted according to actual production needs, ensuring the ore accurately falls into the designated position of the belt conveyor. In the ore loading operation of a certain copper mine, when it is necessary to adjust the ore transportation direction or position, the operator can change the angle and position of the active chute through remote control or on-site manual operation. When changing the transportation route of the belt conveyor or performing equipment maintenance, the operator can adjust the active chute to a suitable position, allowing the ore to be smoothly transported to the backup equipment, ensuring the continuity of the ore loading operation. This flexible adjustment method improves the adaptability of the ore loading system to different production situations and ensures the smooth progress of production.
As the core equipment for long-distance ore transportation, the belt conveyor, with its powerful conveying capacity and high transportation efficiency, quickly and stably transports ore to the weighing hopper. Its conveyor belt uses high-strength, wear-resistant rubber material, capable of withstanding the weight of a large amount of ore and long-term friction. During operation, the drive motor equipped with the belt conveyor provides strong power, driving the conveyor belt to rotate continuously through the roller, achieving continuous ore conveying. To ensure the safe and stable operation of the belt conveyor, the system is also equipped with a series of protective devices, such as conveyor belt tensioning devices, anti-deviation devices, and overload protection devices. These devices can monitor the operating status of the belt conveyor in real time. When an abnormal situation occurs, measures are taken in time to adjust or shut down for protection, avoiding equipment damage and production accidents. For example, when the conveyor belt becomes slack, the tensioning device automatically adjusts the tension of the conveyor belt to ensure normal operation; when the conveyor belt deviates, the anti-deviation device promptly adjusts the position of the conveyor belt to prevent conveyor belt wear and ore spillage.
The weighing hopper, as a key metering link in the ore loading system, uses a high-precision metering device to measure the weight of ore entering it in real time and accurately. Its working principle is based on advanced sensor technology and metering algorithms, accurately calculating the weight of the ore by measuring the pressure of the ore on the bottom of the hopper. In the weighing hopper of a certain copper mine, an advanced pressure-magnetic force meter is used as the metering sensor. This sensor has the advantages of high precision, good stability, and fast response speed. It can measure the ore weight in real time and transmit the data to the control system. When the ore weight reaches the set skip loading capacity, the weighing hopper automatically controls the discharge device to accurately load the ore into the skip. At the same time, the weighing hopper is also equipped with automatic calibration and fault diagnosis functions. It can regularly calibrate the metering device to ensure metering accuracy; when a fault occurs, it can promptly issue an alarm and perform fault diagnosis, providing a basis for equipment maintenance.
The support timbers provide a stable support structure for the entire ore loading system, ensuring that each piece of equipment remains stable during operation and preventing equipment shaking or displacement from affecting the accuracy and safety of the ore loading operation. They are usually made of high-strength wood or steel and have sufficient strength and stability. In the ore loading system of a certain copper mine, the support timbers are reasonably arranged and designed according to the weight and force of each equipment to ensure that they can withstand the weight of the equipment and various forces generated during operation. A firm connection method, such as bolt connection or welding, is used between the support timbers and the equipment to ensure a tight and reliable connection between the equipment and the support timbers. Moreover, to prevent the support timbers from rotting or rusting in the humid underground environment, the support timbers are treated with anti-corrosion measures, extending their service life.
Summary
The underground loading chamber and its skip hoisting ore loading system are key links in ore hoisting in mining engineering, having a profound impact on mining efficiency and cost. In practical applications, different types of skip hoisting ore loading systems have their own characteristics, and mines with and without underground crushing stations also have significant differences in ore loading equipment and processes. Taking the metering hopper single-skip ore loading system of a certain copper mine as an example, it vividly demonstrates the collaborative operation mechanism of each component of the ore loading system.
Note: Part of the article refers to MOOC Northeastern University Underground Mining of Metal Deposits, Xu Shuai, An Long's courseware
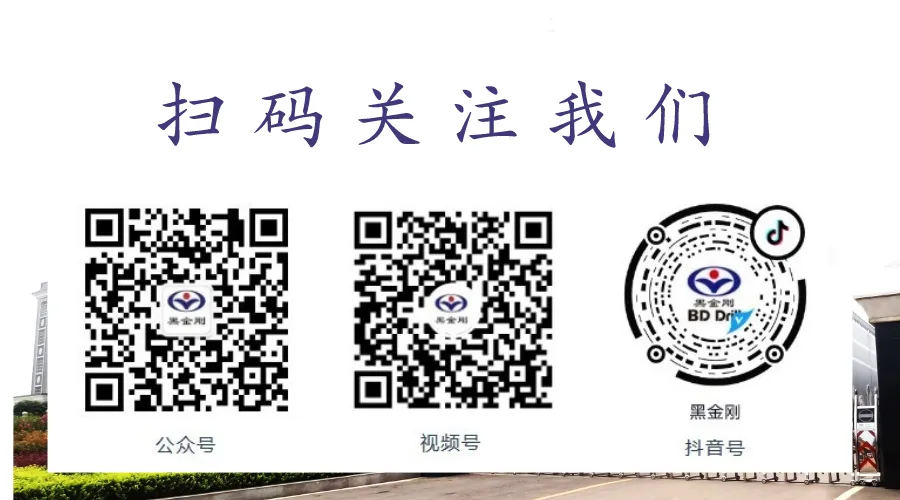
Previous Page