
Choosing the Location of a Subsidiary Shaft in Mining - Black King Kong Report
I. Introduction
In the entire system of mining operations, the sub-shaft plays an indispensable and important role. It is not only a crucial passage for personnel, equipment, and materials to enter and exit the mine, but also undertakes key tasks such as ventilation and drainage. The proper functioning of its features is directly related to the safety, efficiency, and cost of mining operations. The selection of the sub-shaft location is undoubtedly the core element determining whether it can fully function. A reasonable sub-shaft location can minimize transportation distances, reduce energy consumption, improve operational efficiency, and effectively avoid various safety risks; conversely, an inappropriate location choice may lead to a series of problems, such as soaring infrastructure costs, low production efficiency, and frequent safety hazards, having a profound negative impact on the overall mining efficiency. Therefore, in-depth exploration of sub-shaft location selection has important practical significance.
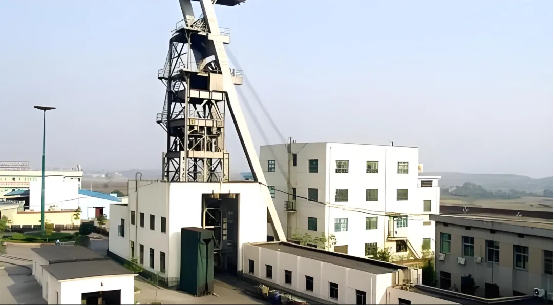
II. Factors Influencing Sub-Shaft Location Selection
(1) Geological Conditions
Geological conditions are the primary consideration in sub-shaft location selection. It is like the sub-shaft's " stable foundation ” ", directly restricting the safety and economy of the sub-shaft. In terms of geological structure, unfavorable geological structures such as faults and folds will seriously affect the stability of the well walls, increasing construction difficulty and risk. Therefore, the sub-shaft location should avoid these areas as much as possible. If it cannot be completely avoided, special support measures must be adopted, increasing engineering costs. Rock stability is also crucial. Hard, intact rocks can provide good surrounding rock conditions for the sub-shaft, reducing the possibility of well wall collapse; while loose, fragmented rocks require more complex support structures and are prone to safety problems during operation. The distribution of aquifers should not be overlooked. If the sub-shaft location passes through water-rich strata, it will lead to increased water inflow, not only increasing drainage costs but also potentially causing water inrush accidents, threatening the safety of underground operations. Therefore, when selecting the sub-shaft location, detailed geological surveys must be conducted to fully understand the geological conditions and thus avoid potential risks.
(2) Mining Methods
Different mining methods have different requirements for sub-shaft location. The adaptability of the sub-shaft location to the mining method is the key to improving mining efficiency. When using the filling method for mining, frequent transportation of filling materials is required. In this case, the sub-shaft location should be as close as possible to the filling operation area to shorten the transportation distance and improve filling efficiency. For caving mining, since the goaf will gradually collapse, the sub-shaft location should be away from the area that may be affected by the collapse to avoid damage to the sub-shaft structure due to goaf collapse. In addition, the underground roadway layout and working face advance direction determined by the mining method will also affect the choice of sub-shaft location. Only by making the sub-shaft location adaptable to the mining method can the entire mining system operate efficiently, reducing unnecessary energy consumption and time waste.
(3) Surface Conditions
The influence of surface conditions on sub-shaft location selection should not be underestimated and requires comprehensive consideration. In terms of topography and geomorphology, if the ground is steep, it will increase the construction difficulty and cost of the sub-shaft wellhead and related facilities, while flat and open terrain is more conducive to the layout of industrial sites. The industrial site layout requires the sub-shaft location to maintain a reasonable distance and convenient connection with surface ore dressing plants, warehouses, offices, and other facilities to facilitate material transportation and production management. External transportation conditions are also crucial. The sub-shaft location should be close to transportation hubs such as highways, railways, or ports to facilitate the transportation of equipment and materials and the transportation of ore, reducing transportation costs. Only by comprehensively considering these surface factors can the sub-shaft location selection be more reasonable, achieving coordinated and efficient operation between surface and underground operations.
(4) Ventilation System Correlation
The selection of the sub-shaft location is closely related to the construction of the ventilation system, and the type of main shaft largely determines the layout of the ventilation system, thus affecting the setting of the sub-shaft. When the main shaft is a skip shaft, a large amount of dust will be generated during the unloading of ore at the wellhead. If it is used as an intake shaft, the dust will be brought underground, polluting the underground air, endangering the health of the operating personnel, and affecting the normal operation of equipment. Therefore, the skip shaft cannot be used as an intake shaft, which requires the special design of a sub-shaft and ventilation shaft to ensure the supply of fresh air underground and the discharge of foul air. In this case, the location of the sub-shaft needs to consider the coordination with the ventilation shaft to ensure a reasonable and smooth ventilation path and improve ventilation efficiency.
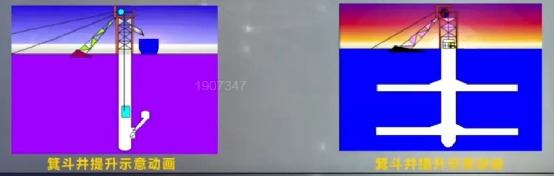
When the main shaft is a cage shaft, the dust generated during its operation is relatively small, and it can also serve as an intake shaft. In this case, another sub-shaft is arranged as a ventilation shaft, which forms a complete ventilation system with the cage shaft. As a ventilation shaft, the location of the sub-shaft should enable the airflow to form an effective circulation underground, covering all operating areas, and ensuring that the air volume and air speed at various locations underground meet the safety regulations. Therefore, the location of the sub-shaft needs to be reasonably planned in combination with the location of the cage shaft and the distribution of underground working faces to achieve good ventilation effects.
III. Sub-Shaft Location Arrangement Methods
(1) Centralized Arrangement
Centralized arrangement refers to the centralized arrangement of the sub-shaft and other main shaft and ventilation shaft facilities in the same area or adjacent locations. This arrangement method has many advantages. In terms of infrastructure engineering, centralized arrangement can reduce the length of connecting roadways between shafts, thereby reducing infrastructure costs and construction time. In terms of management, various shaft facilities are concentrated together, which is convenient for unified management and scheduling, reducing the coordination difficulty between departments and helping to improve management efficiency. In terms of drainage, centralized arrangement allows the underground drainage system to be centrally constructed and operated, facilitating the centralized treatment of mine water and reducing drainage costs.
However, centralized arrangement also has some disadvantages. Due to the concentration of various facilities, once a safety accident such as a fire occurs, the fire is easy to spread, increasing the severity of the accident. At the same time, the dust generated by the main shaft or other facilities will also accumulate in the concentrated area, which is detrimental to the working environment and personnel health.
(2) Decentralized Arrangement
Decentralized arrangement is to arrange the sub-shaft and other shaft facilities in different suitable locations according to the terrain, geological conditions, and mining operation needs of the mine. This arrangement method is suitable for mines with complex terrain and variable geological conditions. In terms of adapting to complex terrain, decentralized arrangement allows each shaft facility to choose the most suitable terrain location according to its functional needs, avoiding the impact of terrain restrictions on the construction and operation of facilities. In terms of reducing mutual interference, different shaft facilities will generate different noises, vibrations, etc., during operation. Decentralized arrangement can effectively reduce the interference of these factors on each other and improve the operational stability of each facility.
However, decentralized arrangement also brings some problems. Due to the decentralized facilities, the management scope is expanded, increasing the management difficulty and requiring more manpower and material resources for coordination and monitoring. At the same time, decentralized arrangement will increase the length of connecting roadways between facilities and the amount of infrastructure engineering, leading to increased infrastructure costs.
IV. Case Analysis of Sub-Shaft Location Selection
(1) Houzhuang Iron Mine: Lessons Learned
The selection of the auxiliary shaft location at Houzhuang Iron Mine had some issues, which brought many adverse effects to the mine's production and operation. The most prominent issue was the increased length of the gate. Due to the improper selection of the auxiliary shaft location, the distance from the auxiliary shaft to each mining area was too long. This not only increased the transportation distance of ore and materials, prolonged the transportation time, and reduced transportation efficiency, but also increased transportation costs and energy consumption.
In addition, the unreasonable design of the bottom of the shaft was also a major problem. The layout of the bottom shaft yard did not match the location of the auxiliary shaft, leading to difficulties in vehicle scheduling and frequent congestion, seriously affecting the smooth transportation underground. This not only reduced mining efficiency but also potentially affected the normal production progress of the mining area due to transportation problems. These problems ultimately reflected in economic efficiency, increasing the mine's production costs, reducing profit margins, and posing significant challenges to production management, serving as a warning to other mines regarding the selection of auxiliary shaft locations.
(II) A Successful Case: Exemplary Inspiration
A large domestic copper mine achieved remarkable success in the selection of its auxiliary shaft location, providing valuable experience for the industry. When selecting the auxiliary shaft location, the copper mine fully considered various factors, including geological conditions, mining technology, ground facility layout, and ventilation systems. Through detailed geological surveys, they chose a location with good rock stability and few aquifers, reducing safety risks during construction and operation.
At the same time, the auxiliary shaft location is compatible with the staged open-pit mining method used by the mine, and its proximity to the main mining area shortens the ore transportation distance, greatly improving mining efficiency. In terms of ventilation, combining the characteristics of the main shaft as a cage shaft that can also serve as an intake shaft, the auxiliary shaft is reasonably arranged as a ventilation shaft, forming a highly efficient ventilation system and ensuring a safe and comfortable underground working environment.
In addition, the auxiliary shaft's location is close to the surface concentrator and railway transportation, facilitating ore transportation and processing. Through this series of reasonable choices, the copper mine not only reduced infrastructure and operating costs but also improved mining efficiency and production safety, achieving good economic and social benefits and becoming a successful model for auxiliary shaft location selection.
V. Process and Methods for Auxiliary Shaft Location Selection
(I) Preliminary Survey
The preliminary survey is the foundation of auxiliary shaft location selection. Only through accurate assessment can accurate data support be provided for subsequent decision-making. Geological survey is the core content of the preliminary survey. It is necessary to thoroughly ascertain the mine's geological structure, rock properties, aquifer distribution, fault fracture zones, etc. First-hand geological data should be obtained through drilling and geophysical exploration to provide a basis for judging the geological feasibility of the auxiliary shaft location.
Topographic surveying involves precise measurement of the mine's surface topography, geomorphology, and elevation changes, creating detailed topographic maps to provide topographic data for the layout of the auxiliary shaft shaft mouth and surface facilities. At the same time, it is necessary to investigate the distribution of buildings, roads, rivers, and underground pipelines and cables on the ground to avoid conflicts between the auxiliary shaft location and these facilities. Only by doing a good job in the preliminary survey can we fully understand the geological and surface conditions of the mine and lay a solid foundation for the reasonable selection of the auxiliary shaft location.
(II) Multiple Scheme Design
Based on the preliminary survey, multiple auxiliary shaft location selection schemes need to be developed for comprehensive consideration. When designing the schemes, the advantages and disadvantages of different locations in terms of geological conditions, mining technology adaptability, ground facility layout, ventilation effects, infrastructure costs, and operating costs should be fully considered. For example, one scheme may have superior geological conditions but is far from the mining area, resulting in higher transportation costs; another scheme may be close to the mining area but has relatively complex geological conditions and greater construction difficulties.
By comprehensively analyzing and comparing the technical feasibility, economic rationality, and safety reliability of multiple schemes, the advantages and disadvantages of each scheme can be identified, providing sufficient basis for subsequent comprehensive evaluation and decision-making.
(III) Comprehensive Evaluation and Decision-Making
Comprehensive evaluation and decision-making are key links in the selection of auxiliary shaft locations, requiring the use of scientific methods for decision-making. The analytic hierarchy process (AHP) is a commonly used method. It stratifies various influencing factors in the selection of auxiliary shaft locations, constructs judgment matrices, calculates the weights of various factors, and then ranks different schemes. The fuzzy comprehensive evaluation method is suitable for handling factors that are difficult to quantify accurately, such as environmental impact and management difficulty. By establishing a fuzzy evaluation model, a comprehensive evaluation of the schemes is conducted.
In the comprehensive evaluation process, various factors such as technology, economy, safety, and environment should be fully considered, combined with the actual situation and long-term development plan of the mine, to conduct a comprehensive and objective evaluation of each scheme. Finally, based on the evaluation results, the optimal auxiliary shaft location scheme is selected to ensure that it meets the various requirements of mine production and achieves the unity of economic benefits, social benefits, and environmental benefits.
VI. Summary
The selection of the auxiliary shaft location is a crucial decision in mining engineering. It is comprehensively affected by various factors such as geological conditions, mining technology, ground conditions, and ventilation system correlation. Reasonable layout methods (centralized or decentralized layout) each have their applicable scenarios and advantages and disadvantages, and need to be selected according to the specific situation of the mine.
The process of auxiliary shaft location selection includes preliminary survey, multiple scheme design, and comprehensive evaluation and decision-making. Each link is indispensable, and scientific decision-making methods are the key to ensuring the rationality of the selection.
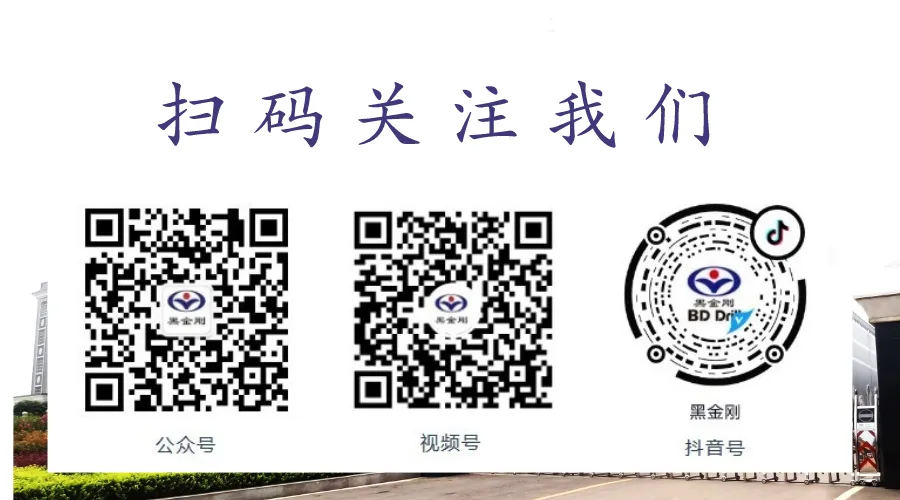