
Classification of Wellfield Development Methods——Black King Kong Broadcast
Preface
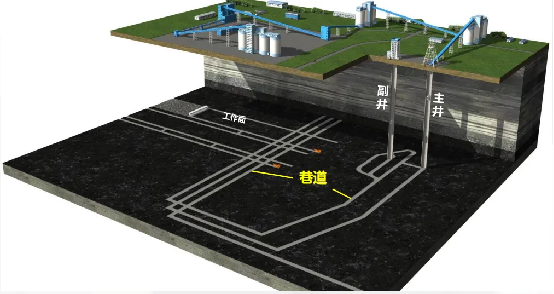
(Image from MOOC China University of Mining and Technology Mining Engineering Tu Shihao, Fang Zhijun, Zheng Xigui, Wang Xufeng, Peng Hongge, Yuan Yong )
In the field of mining engineering, the layout of mine workings is the cornerstone, playing a decisive role in the efficient, safe, and sustainable advancement of the entire mining operation. In essence, the layout of mine workings refers to the arrangement of the main roadways within the mining area. These main roadways, including shafts, stone gates, horizontals, and main haulage ways, collectively form a network of passages from the surface to the ore body, serving as the key infrastructure for the extraction of mineral resources. A reasonable layout of mine workings can significantly improve mining efficiency, effectively reduce production costs, and provide a solid guarantee for safe production. Different mine working layouts have their own characteristics due to differences in geological conditions, topography, ore body occurrence, and mining techniques. Therefore, in-depth understanding and accurate selection of suitable mine working layouts are important issues facing mining engineers, having profound implications for ensuring the economic and social benefits of mines. Next, this article will comprehensively and in-depth discuss the classification of mine working layouts and analyze the unique features and applicable scenarios of various layouts.
Main Roadways
Shaft Types
• Vertical Shaft Vertical shaft development utilizes vertical roadways to access the underground from the surface, then reaching the ore body through a series of roadways. Its advantages include high hoisting system stability, ability to withstand large hoisting loads, suitability for deep and high-output mines, relatively simple shaft maintenance, small land occupation, and less susceptibility to geological changes. However, vertical shaft development also has significant drawbacks: high shaft construction difficulty, requiring special equipment and technology, long construction period, high cost, slow hoisting speed, low transportation efficiency, long ventilation routes, high resistance, and high cost. When the thickness of the topsoil layer above the coal-bearing strata is large, or the coal seam is buried deep, vertical shaft development is generally adopted; mines with high hoisting capacity requirements and limited land space also often adopt vertical shaft development. For example, in some deep coal mining operations, due to the deep burial of coal seams, vertical shaft development can effectively achieve the exploitation of deep resources.
• Inclined Shaft Inclined shaft development utilizes inclined roadways to access the underground from the surface, and reaches the coal seam through a series of roadways. Its advantages include relatively simple shaft construction, low equipment and technology requirements, short construction period, low cost, the hoisting system can use continuous transportation equipment such as belt conveyors, high transportation efficiency, short ventilation routes, low resistance, and low cost. However, inclined shaft development has high shaft maintenance difficulty, requiring regular maintenance and reinforcement, the hoisting load is less affected by the inclination angle, it is not suitable for deep and high-output mines, the shaft occupies a large land area, and greatly affects the layout of ground facilities. Currently, inclined shaft development is mainly suitable for mines with shallow coal seam burial depth, thin topsoil layer, and relatively simple geological conditions; mines with high transportation efficiency requirements and less land space restrictions also often adopt inclined shaft development. With the development of powerful belt conveyors, the applicable range of inclined shaft development is continuously expanding.
• Adit Adit development utilizes horizontal roadways to access the coal seam from the surface for mining, and is the simplest and most economical mine development method. It has the lowest construction difficulty, lowest cost, and shortest period, the transportation system can use gravity flow transportation, high efficiency, low cost, the ventilation system is the simplest, the resistance is the smallest, and the cost is the lowest. However, the applicable range of adit development is greatly limited by topographic conditions, and can only be used when topographic conditions are suitable, and once the shaft is damaged, it is difficult to repair. It is mainly suitable for mines where topographic conditions are suitable, coal seams are buried in mountainous areas, and the coal seam is located at a high position, with conditions to directly enter the coal seam using an adit. For example, in some mountainous areas, when the coal seam is located at a high position and there is suitable terrain, adit development can demonstrate its unique advantages.
• Combination Combination development uses two or more basic shaft types (vertical shaft, inclined shaft, adit) to develop the mining area. This development method can fully utilize the advantages of various shaft types, flexibly combining shaft types according to different geological and production technology conditions, and has strong adaptability. However, combination development has high construction difficulty, requiring coordination of the construction of various shaft types, complex construction organization and management, high cost, and requires more investment and resources. According to different geological and production technology conditions, combination development can have adit — inclined shaft, vertical shaft — inclined shaft, vertical shaft — adit and vertical shaft — inclined shaft — adit, etc., mainly suitable for mines with complex geological conditions where a single shaft type cannot meet production requirements.
Number of Levels
• Single Level Single-level development only sets up one mining level in the mining area, using this level to mine all coal seams in the mining area. The advantages of this development method are a relatively simple development system, low initial investment, short well construction period, and relatively convenient production management. However, it also has limitations. When the mining area is large and the coal seam depth varies greatly, it may not be able to effectively meet mining needs, leading to reduced mining efficiency. Single-level development is generally suitable for mines with small mining areas, relatively stable coal seam occurrence, and small depth variations. For example, in some small coal mines, with limited mining areas, single-level development can achieve efficient mining.
• Double Level Double-level development sets up two mining levels in the mining area, respectively mining coal seams at different elevations or in different areas. Its advantages include the ability to reasonably arrange the mining of the two levels according to the coal seam occurrence conditions and mining sequence, improving mining efficiency, and being more adaptable to situations with large mining areas and certain variations in coal seam depth. However, double-level development has a relatively large development workload, high investment, long well construction period, and requires coordination of the mining relationship between the two levels, making production management relatively complex. It is suitable for mines with large mining area strike length and certain differences in coal seam depth, and can better adapt to the mining requirements of different coal seams.
• Multiple Levels Multi-level development involves establishing three or more mining levels within a coalfield. This approach allows for more precise division of the coalfield, adapting to complex geological conditions and the mining needs of different coal seams, thereby improving coal resource recovery rates. However, multi-level development is a massive undertaking, requiring substantial investment, extended construction periods, and more complex transportation, ventilation, and drainage systems between levels, leading to extremely challenging production management. It is typically suitable for large mines with extensive coalfields, complex coal seam distribution, and significant mining depths. For instance, some extra-large coal mines, due to their vast coalfields and complex coal seam conditions, require multi-level development to achieve efficient resource extraction.
Main roadway layout
• Coal seam layout In the coal seam layout, main roadways are arranged within the mining level, in each mineable coal seam, or in the underlying strata of the coal seam. Each coal seam has its own independently laid-out mining area, with the different coal seams connected by main stoppings. For each mining area, the preparatory work is relatively small, and only one main stopping is opened between the main roadways of each coal seam, with the stopping development work generally not being extensive; when constructing the mine shaft, development preparation is first carried out in the upper coal seam, with a smaller initial workload; if the main roadways of each coal seam are excavated along the coal seam, the construction speed is faster, and the initial investment is lower. However, the total development and maintenance workload is large because main roadways are arranged in each coal seam; maintaining roadways laid along coal seams is difficult, with high maintenance costs and significant coal pillar losses. In the early days of the People's Republic of China, when coal seam roadway support technology was not advanced, this method was suitable for medium-sized and small mines with large inter-seam spacing, short coalfield strike lengths, and short service lives.
• Centralized layout In a centralized layout, only one or a pair of centralized main roadways are arranged within the mining level, connecting the various coal seams using mining area stoppings. This layout has a smaller amount of main roadway work; the main roadways are generally arranged in the underlying strata of the coal group or in the lowermost coal seam with strong rock, making maintenance easier; the production area is more concentrated, which helps improve underground transportation efficiency; since the coal seams are connected by mining area stoppings, preparation and mining of several coal seams can be carried out simultaneously, allowing for more flexible mining sequences and higher mining intensity. However, before the mine is put into production, main stoppings, centralized transportation main roadways, and mining area stoppings must be excavated. When the coal-bearing strata are thick, the initial mine construction workload is large, and the construction period is long; each mining area needs to excavate mining area stoppings, and when the inter-seam spacing is large, the total length of the mining area stoppings is large. Therefore, this layout is suitable for mines with long coalfield strike lengths, long service lives, a large number of coal seams, and small inter-seam spacing.
• Grouped centralized layout In a grouped centralized layout, the coal seams are divided into several groups, with a centralized main roadway excavated for each group. Within each group, the coal seams are connected by mining area stoppings, and the grouped centralized main roadways are connected by main stoppings or divisional stoppings. This layout has a smaller total roadway workload; production is more concentrated, and the main roadways are easy to maintain. The disadvantage is that the total length of the stoppings is longer. It is suitable for mines with many mineable coal seams and varying inter-seam spacing. In particular, due to the requirements of shaft layout, when the bottom of the shaft is located in the upper or middle part of the coal seam group, using a grouped layout reduces the initial workload and shortens the construction period.
Preparation methods
• Uphill method The uphill preparation method refers to the location of the mining area uphill above the mining level, with coal transported downwards. Underground water can flow into the sump at the bottom of the shaft by gravity along the mining area uphill. This drainage method results in a relatively simple drainage system, eliminating the need for complex drainage equipment and facilities, resulting in extremely low energy consumption. This not only reduces equipment operating costs but also reduces the risk of drainage problems due to equipment malfunctions. In terms of transportation, coal transportation is smoother and more efficient. During excavation, upward excavation makes ventilation relatively easy, facilitating the removal of harmful gases. However, the uphill preparation method is significantly affected by the coal seam dip angle; for coal seams with steeper dip angles, the mining difficulty increases. It is suitable for areas with relatively small coal seam dip angles and relatively simple geological conditions.
• Downhill method In the downhill preparation method, the mining area downhill is located below the mining level, with coal transported upwards. The direction of water flow is opposite to the mining direction. Temporary sumps need to be set up in each section to collect water, and small pumps must also be installed to pump the water from the temporary sumps section by section to the main roadway, and then from the main roadway to the sump at the bottom of the shaft. This process not only requires substantial equipment investment for purchasing small pumps and related drainage pipes, but the operation and maintenance of small pumps also require significant manpower, material resources, and financial resources. In terms of transportation, upward coal transportation requires overcoming gravity, resulting in higher transportation costs. During excavation, ventilation is more difficult, and the removal of harmful gases is challenging. However, the downhill preparation method allows for the full exploitation of deep coal resources. It is suitable for mines where there are mineable resources in the deep coal seams and there is a demand for deep resource extraction.
• Uphill and downhill method The uphill and downhill preparation method combines the characteristics of the uphill and downhill methods, simultaneously arranging mining area uphills and mining area downhills. This method can more flexibly adapt to different coal seam conditions and improve coal resource recovery rates. In terms of ventilation, drainage, and transportation, the advantages of uphill and downhill methods can be rationally utilized according to the actual situation. However, the roadway layout of the uphill and downhill preparation method is more complex, requiring coordination of the mining relationship between uphill and downhill, resulting in greater management difficulty. It is suitable for mines with complex coal seam conditions, where there are areas suitable for uphill mining and areas suitable for downhill mining.
Ventilation methods
• Central parallel method Intake and return air shafts are arranged in parallel within the central industrial area. The bottoms of the two shafts can be excavated to the first level, or the return air shaft can only be excavated to the return air level to prevent air leakage from the production level shaft bottom yard to the return air shaft. The initial development workload is small, the investment is low, and the production is fast; the ground buildings are concentrated, which is convenient for management; the two shafts are concentrated, which is beneficial for excavation and shaft deepening; there are few safety coal pillars in the shaft, which is easy to achieve mine reversal. However, the ventilation route is a return type, with a long air route and large resistance. When the coalfield strike length is long, the difference in air resistance between the remote mining area and the central mining area is large, which may lead to insufficient air volume in the remote mining area; the intake and return air shafts are close to each other, with large air leakage at the bottom of the shaft, easily causing short-circuiting of the airflow; there are few safety exits, only two; the industrial area is easily affected by the noise of the main ventilation fan and the pollution of the return air flow. It is suitable for mines with a coalfield strike length of less than 4km , a large coal seam dip angle, deep burial depth, and no serious gas or spontaneous combustion problems.
• Central separated method The intake airway is located in the industrial square at the center of the seam's strike and dip direction, while the return airway is generally located in the central part of the upper boundary of the mining area along the strike, with the bottom of the return airway higher than that of the intake airway. This offers good safety; the ventilation resistance is smaller than that of the central parallel system, with less air leakage inside the mine, which is beneficial for the management of gas and spontaneous combustion; the industrial square is not affected by the noise of the main ventilation fan or polluted by the return airflow. However, it requires an additional airway site, occupying more land and coal; the airflow route underground is a return type, with a long airflow route and large ventilation resistance. Suitable for mines with seam strike length less than 4km ,with a small coal seam dip angle, shallow burial depth, and serious gas and spontaneous combustion problems.
• Diagonal Two-Wing System The intake airway is generally located in the center of the seam's strike, with one exhaust airway excavated near the boundaries of both wings along the strike in the upper part of the mining area or in the center of the mining area of both wings. If there is only one return airway, and the intake and return airways are located on both wings of the mining area, it is called a single-wing diagonal system. The airflow route underground is a straight type, with a short airflow route and small ventilation resistance; there is little air leakage inside the mine; the air resistance between different mining areas is relatively balanced, making it easy to distribute air as needed; the total air pressure of the mine is stable, and the load of the main ventilation fan is relatively stable; there are multiple safety exits, and the disaster resistance is strong; the industrial square is not affected by return air pollution or the noise of the main ventilation fan. However, the initial investment is large, and the construction period is long; management is decentralized; and a large amount of coal is compressed in the shaft safety coal pillar. Suitable for mines with seam strike length greater than 4km ,requiring large air volume, easy coal spontaneous combustion, and coal and gas outbursts.
• Zonal Diagonal System The intake airway is located in the center of the seam's strike, with a return airway excavated at the upper boundary of each mining area, without a total return airway. Each mining area does not affect each other, making it easy to adjust the air volume; the construction period is short; the initial investment is low, and the coal output is fast; there are multiple safety exits, and the disaster resistance is strong; the intake and return air routes are short, and the ventilation resistance is small. However, there are many airways, occupying more land and coal; the main ventilation fans are decentralized, and management is complex; the service range of the airway and the main ventilation fan is small, and frequent replacements are needed; it is difficult to reverse the mine air. Suitable for mines where, due to shallow coal seam burial or large coal seam weathering zones and surface undulations, it is impossible to excavate a shallow total return airway. When mining the first level, only a zonal system can be used. In addition, this ventilation method can also be used for mines with long seam strike length, multi-seam mining, or mines with long seam strike length, large output, large air volume requirements, easy coal spontaneous combustion, and coal and gas outbursts.
• Hybrid System A hybrid arrangement of central and diagonal systems, with at least 3 intake and exhaust airways, including hybrid systems such as central parallel and two-wing diagonal, central boundary and two-wing diagonal, and central parallel and central boundary. This is beneficial for the phased construction of the mine, saving investment, speeding up coal output, and improving efficiency; there are many return airways, with large ventilation capacity; the layout is flexible and adaptable. However, multiple fans work together, the ventilation network is complex, and the management is difficult. Suitable for the reconstruction and deep mining of old mines with long seam strike length, multi-seam and multi-shaft mines, and large mines with large mining area, large output, large air volume requirements, or zonal mining.
Summary
As a key link in mining engineering, the choice of mining area development method directly affects the mine's production efficiency, safety, and economic benefits. From the perspective of shaft types, vertical shafts, inclined shafts, adits, and integrated development each have their own advantages and disadvantages, and need to be accurately chosen based on factors such as coal seam burial depth, geological conditions, and topography. The determination of the number of levels should fully consider the mining area range, coal seam occurrence, and mining technology. Single-level, double-level, and multi-level development are suitable for different mine conditions. The three forms of inter-seam, centralized, and group-centralized roadway layouts also have different applicable scenarios due to factors such as the distance between coal seams and the length of the mining area strike. The uphill, downhill, and up-and-downhill methods in preparation, and the central parallel, central split, two-wing diagonal, zonal diagonal, and hybrid methods in ventilation, also need to be reasonably selected based on specific geological conditions, mine scale, and ventilation requirements.
(The article refers to MOOC China University of Mining and Technology Mining Engineering the courseware of Tu Shihao, Fang Zhijun, Zheng Xigui, Wang Xufeng, Peng Hongge, and Yuan Yong )
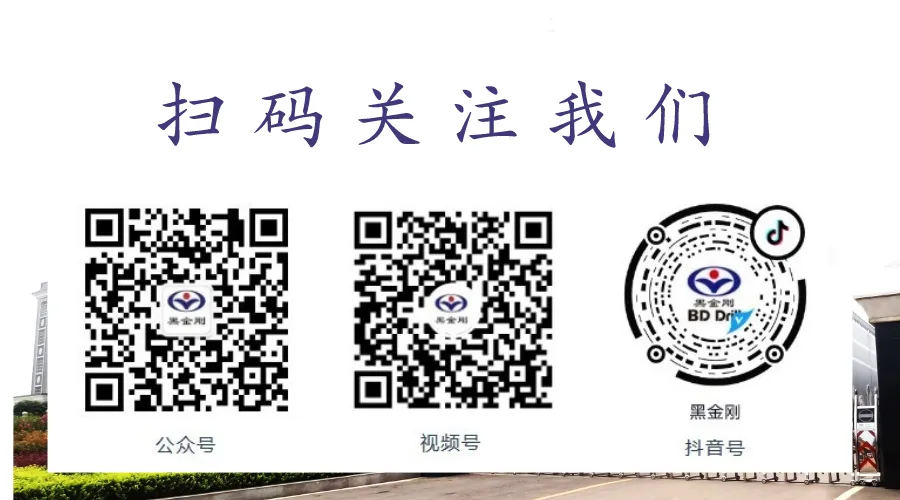
Previous Page