




Main and auxiliary shafts (drifts) site selection for coal mines - Black Diamond Report
Preface
As a crucial passage connecting the surface and underground, the rationality of the shaft's location plays a vital role in coal mining activities. Once the shaft's location is determined and construction is completed, it is difficult to change it during the long service life of the mine. Therefore, scientifically and accurately selecting the shaft's location from the outset is a crucial part of the preliminary planning of coal mining.
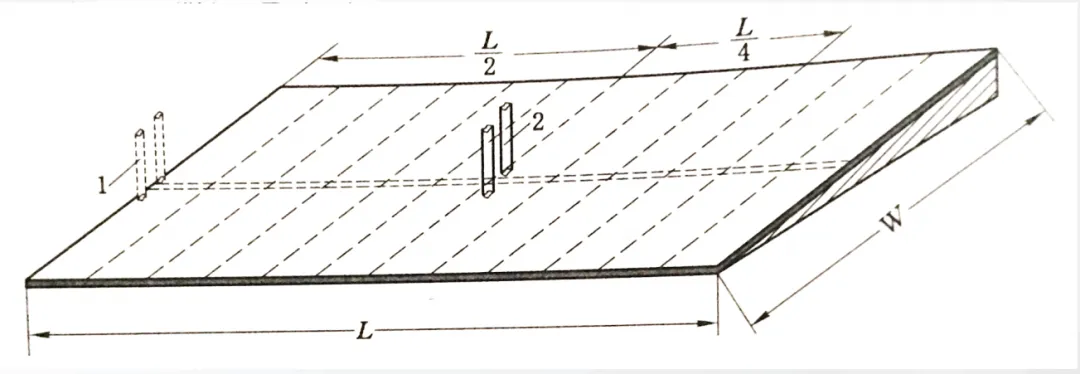
(Image from China University of Mining and Technology, Mukke, Mining Engineering, Tu Shihao, Fang Zhijun, Zheng Xigui, Wang Xufeng, Peng Hongge, Yuan Yong)
From the perspective of mining efficiency, a reasonable shaft location can greatly optimize underground transportation routes. If the shaft is located in the center of the mining area, the transportation workload along the coal seam trend will be minimized, and transportation costs will also be reduced. This not only means a shorter transportation time but also allows coal to be transported from the mining face to the surface faster, reducing the coal's stay time underground, making the entire mining process more compact and efficient. At the same time, this location can also make the air distribution more balanced, shorten the ventilation route, and reduce the ventilation resistance. Good ventilation conditions can provide a safer and more comfortable working environment for underground workers, avoiding safety hazards such as gas accumulation due to poor ventilation, thus ensuring the smooth progress of mining work.
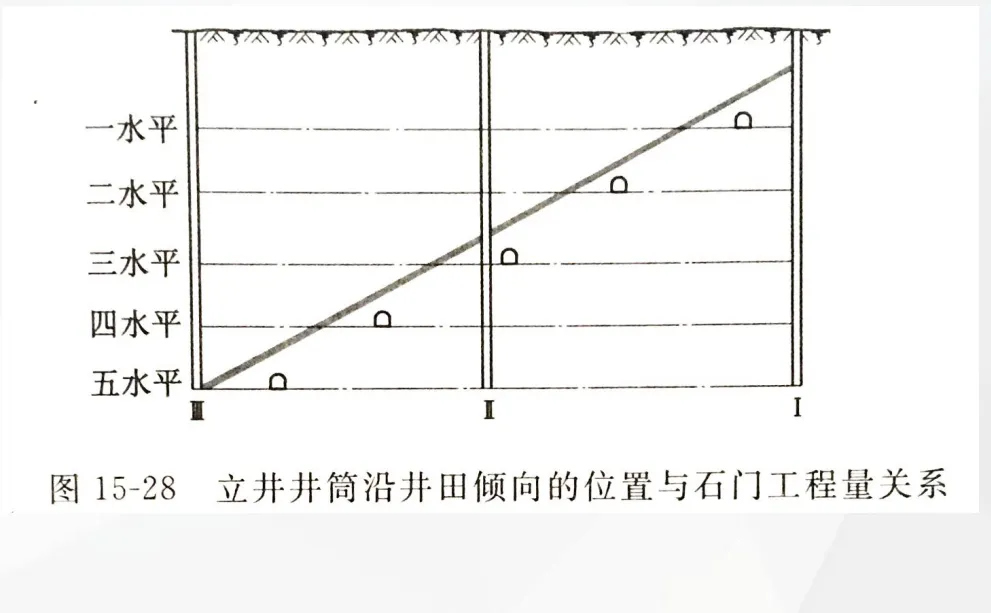
(Image from China University of Mining and Technology, Mukke, Mining Engineering, Tu Shihao, Fang Zhijun, Zheng Xigui, Wang Xufeng, Peng Hongge, Yuan Yong)
In terms of cost control, the shaft location is directly related to the amount of roadway engineering, underground transportation workload, and roadway maintenance workload. If the location is not chosen properly, it may be necessary to excavate longer roadways, increasing support costs, and maintenance costs will remain high in the later stages. A reasonable location can effectively reduce these unnecessary expenses, reduce initial investment and operating costs, and improve the economic benefits of coal mining.
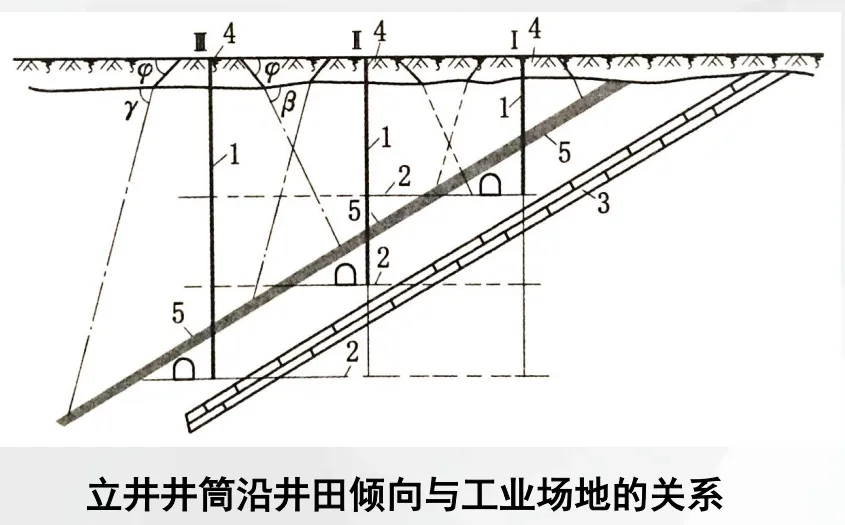
(Image from China University of Mining and Technology, Mukke, Mining Engineering, Tu Shihao, Fang Zhijun, Zheng Xigui, Wang Xufeng, Peng Hongge, Yuan Yong)
In addition, the shaft location also has a profound impact on mine safety and sustainable development. A suitable location can reduce coal pillar loss, avoid excessive damage to mineable coal seams, facilitate the full exploitation of resources, and extend the service life of the mine. At the same time, the setting of safety exits, the convenience of emergency rescue, etc., are also closely related to the shaft location. A scientific and reasonable shaft location can buy valuable time for personnel evacuation and rescue in emergencies, maximizing the protection of personnel safety and minimizing property losses.
Along the trend layout
In coal mining, the layout along the trend of the mining area is one of the key considerations in determining the shaft location. Placing the shaft in the center of the mining area for bilateral mining has many significant advantages and is of great significance to the efficient operation of the entire coal mining process.
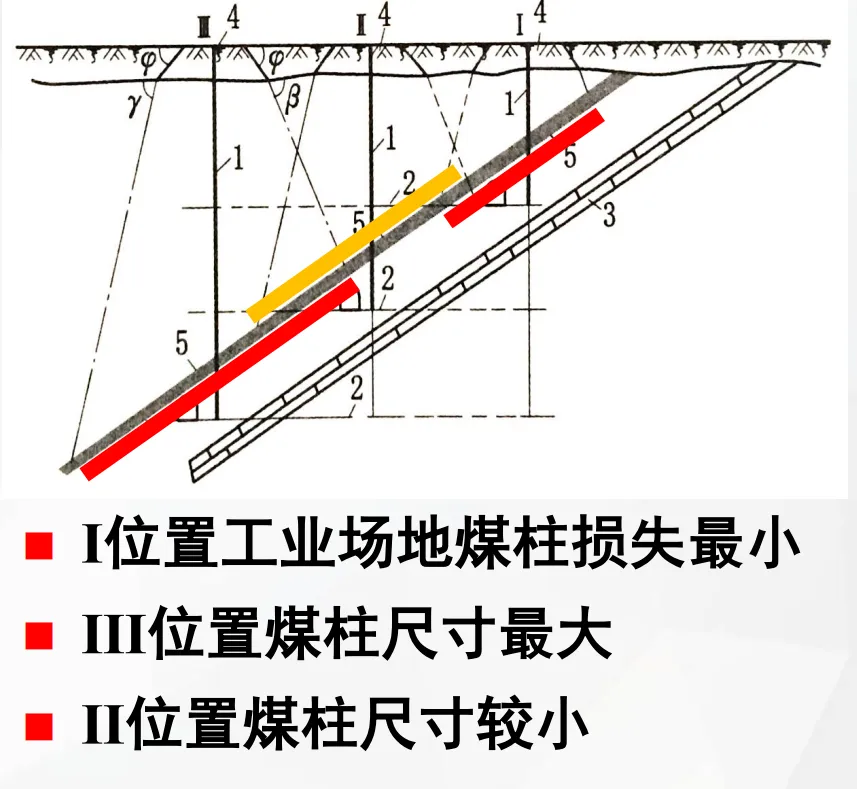
Optimization of transportation costs
When the shaft is located in the center of the mining area, the coal transportation route can be optimally configured. Taking a large coal mine as an example, when the trend length of the mining area reaches 10 kilometers, if the shaft is located at the boundary, the coal transportation distance can be as long as 10 kilometers; while if it is located in the center of the mining area, the maximum transportation distance is shortened to 5 kilometers. The shorter transportation distance not only means a significant reduction in coal transportation time but also reduces the energy consumption of transportation equipment, as well as the wear and tear and maintenance costs of transportation equipment. Through bilateral mining, coal can be transported from both sides of the mining area to the central shaft. This two-way transportation mode greatly improves transportation efficiency, reduces the investment and operating costs of transportation equipment, and thus reduces the cost of coal mining, making coal mines more competitive in the market.
Improvement of the ventilation system
Bilateral mining has a positive effect on the ventilation system. Because the shaft is located in the center of the mining area, the ventilation route is shortened. Taking the above-mentioned coal mine as an example, the ventilation route can be shortened from the original maximum of 10 kilometers to about 5 kilometers. A shorter ventilation route means a significant reduction in ventilation resistance. After the ventilation resistance is reduced, the energy consumption of ventilation equipment is reduced, and the operating costs are also reduced. Moreover, bilateral mining makes the air distribution more balanced, avoiding the uneven air distribution that may occur in unilateral mining, ensuring that all operating areas underground have a sufficient and stable supply of fresh air, creating a safer and more comfortable working environment for underground workers, effectively reducing safety hazards such as gas accumulation caused by poor ventilation, and ensuring the safety and stability of coal mine production.
Advantages of mining succession
In terms of mining succession, the advantages of bilateral mining are obvious. Through bilateral mining, the output of both wings of the mining area can be balanced. Still taking this coal mine as an example, during the long-term mining process, the difference in output between the two wings can be controlled within a very small range. This balanced output makes the service life and completion time of the two wings relatively close, avoiding the situation where one wing is mined too early and the other wing has excessive mining pressure in the later stage. When one wing is nearing the end of mining, the other wing can smoothly take over, ensuring stable mine output, reducing the difficulty of transition between mining levels, making the entire mining process more coherent, and providing a strong guarantee for the sustainable mining of the coal mine.
Dip consideration
Stone gate engineering and overburden problems
In the process of vertical shaft development, the choice of shaft location along the dip of the mining area has a key impact on the amount of stone gate engineering and overburden. From the perspective of stone gate engineering, when the shaft is located in the middle of the mining area dip, the total amount of stone gate engineering and the transportation workload in the stone gate are minimized, and the initial stone gate engineering is also relatively small. Taking a mining area as an example, if the shaft is located in the middle of the mining area dip, the total length of the stone gate can be controlled at around 500 meters; while if it is located at the upper and lower boundaries of the mining area, the total length of the stone gate may increase to 800-1000 meters. Longer stone gates not only require more manpower and material resources for excavation but also require a lot of funds and energy in subsequent maintenance.
The impact of shaft location on overburden cannot be ignored. When the shaft is located in the middle of the mining area dip, the size of the industrial site coal pillar is relatively small, which can effectively reduce the loss of coal resources. In mines mining steeply inclined coal seams, because the loss of industrial site coal pillars increases with the increase of the coal seam dip angle, vertical shafts are often located closer to the upper boundary of the mining area to reduce coal pillar loss. In a steeply inclined coal seam mine with a coal seam dip angle of 60°, if the shaft is located closer to the upper boundary of the mining area, coal pillar loss can be reduced by about 20%, which is of great significance to the full utilization of coal resources and the sustainable development of the mine.
Relevance of the first level mining
The shaft location along the dip is closely related to the first level mining. A suitable location can create many favorable conditions for the first level mining. When the shaft location is conducive to the first level mining, it can make the mining range of the first level more reasonable, reducing blind spots and resource waste caused by improper shaft location. In a mine using vertical shaft development, a reasonable shaft location increases the mining range of the first level by 10%, increasing the recoverable reserves and extending the service life of the first level.
A suitable shaft location can simplify the mining system of the first level and reduce mining costs. If the shaft location is unreasonable, it may be necessary to set up a complex auxiliary hoisting system or ventilation system to meet the mining needs of the first level, which will undoubtedly increase the mining cost and management difficulty. A reasonable shaft location can make the hoisting and ventilation systems more efficient, reducing equipment investment and operating costs. In some mines, by optimizing the shaft location along the dip, the equipment investment cost of the first level mining was reduced by 15%, and the operating cost was reduced by 10%, greatly improving the economic benefits of the mine.
Multi-dimensional comprehensive decision-making
Strata and industrial square factors
The reasonable location of the shaft passing through the strata plays a decisive role in the safety and stability of the entire mine construction and operation. When selecting the shaft location, a comprehensive and in-depth investigation and analysis of the geological structure, lithology, and hydrogeology of the strata must be carried out. If the strata through which the shaft passes have unfavorable geological areas such as faults, fractured zones, or quicksand layers, during the shaft construction process, serious accidents such as collapse and water inrush may occur, which will not only delay the construction period but also greatly increase the construction cost, and even threaten the life safety of construction personnel. In the construction of a certain coal mine, due to insufficiently detailed investigation of the strata, a large fault was encountered during shaft construction, causing the shaft to deform, and multiple reinforcements and repairs had to be carried out, delaying the construction period for a year and increasing the cost by tens of millions of yuan.
The reasonable location of the ground industrial square should not be ignored either. It is an important carrier of the mine's ground production system and administrative management system and needs sufficient space to arrange the mine's ground production system and its industrial buildings and structures. The industrial square should have good engineering geological conditions, avoiding unfavorable sections such as landslides, rockfalls, and caves, to ensure the safety and stability of the buildings. At the same time, it should facilitate mine power supply, water supply, and transportation, and have convenient locations for the construction of residential areas and gangue disposal facilities nearby. When choosing the location of the industrial square, a certain coal mine fully considered the terrain and transportation conditions and arranged it near the highway and power source, which not only facilitated the transportation of coal and the power supply of equipment but also reduced construction costs and improved production efficiency.
Application of the scheme comparison method
In the actual determination of the shaft location, multiple schemes are usually proposed in combination with the choice of mining method, and then the scheme comparison method is used for screening and determination. The key to the scheme comparison method lies in a comprehensive and systematic technical and economic analysis of each scheme. In terms of technology, it is necessary to consider factors such as the amount of shaft and roadway engineering, construction difficulty, rationality of the ventilation system, and convenience of the transportation route. In a coal mine with a strike length of 8 kilometers and a dip length of 2 kilometers, two shaft location schemes were proposed. Scheme 1 has a shaft and roadway engineering volume of 10,000 meters, a high construction difficulty, and a long ventilation route; Scheme 2 has a shaft and roadway engineering volume of 8,000 meters, a relatively low construction difficulty, and a shorter ventilation route. Through comparison, Scheme 2 has a greater technical advantage.
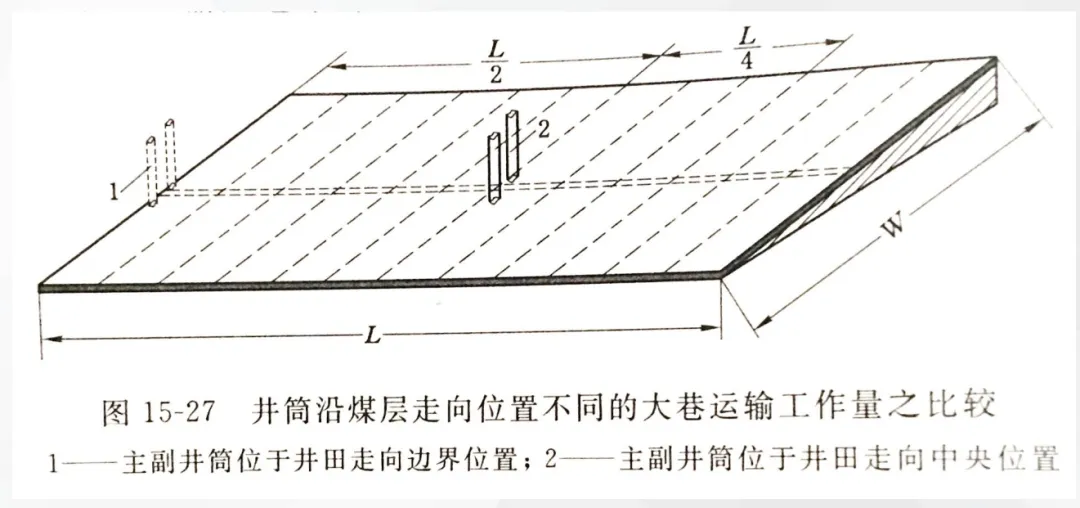
In terms of economics, construction investment, operating costs, coal resource recovery rate, etc., should be considered. Taking the above-mentioned coal mine as an example, the construction investment of Scheme 1 is 100 million yuan, the annual operating cost is 5 million yuan, and the coal resource recovery rate is 80%; the construction investment of Scheme 2 is 80 million yuan, the annual operating cost is 4 million yuan, and the coal resource recovery rate is 85%. Comprehensive economic analysis shows that Scheme 2 performs better in cost control and resource utilization. Through a comprehensive comparison of multiple schemes in terms of technology and economics, weighing the pros and cons, the final determination of a technically feasible and economically reasonable shaft location scheme lays a solid foundation for the efficient and safe mining of the coal mine.
Summary
The site selection of the main shaft and auxiliary shaft (tunnel) of a coal mine is a complex and crucial decision-making process that requires in-depth analysis and comprehensive consideration from multiple dimensions. When laying out along the strike, placing the shaft in the center of the mining area for bilateral mining can effectively reduce transportation costs, optimize the ventilation system, and provide strong support for mining succession. In terms of dip consideration, the amount of stone gate engineering, the problem of overlying coal pressure, and the relationship with the first-level mining should be fully considered to achieve efficient resource utilization and simplification of the mining system.
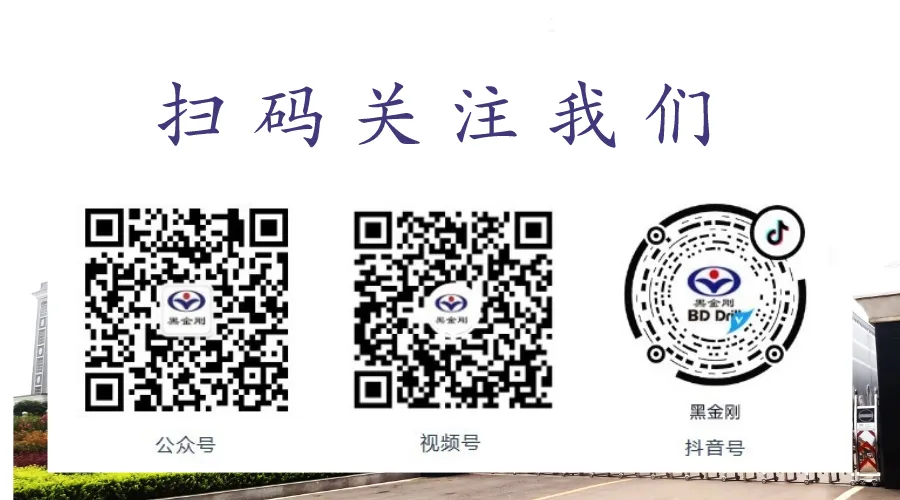