
Factors to consider when selecting the location of the main access roadway - Black King Kong Report
Introduction
In the field of mining engineering, the selection of the location for developing roadways is a crucial step, and its importance cannot be overstated. As the key passage connecting the underground mining area to the surface, the development roadway is a vital hub for the smooth operation of the entire mining operation. It not only bears the responsibility of transporting ore and waste rock, but also serves as an important support for numerous systems such as ventilation, drainage, and power supply. It has a profound impact on the efficiency, cost, safety, and sustainability of the entire mining operation.
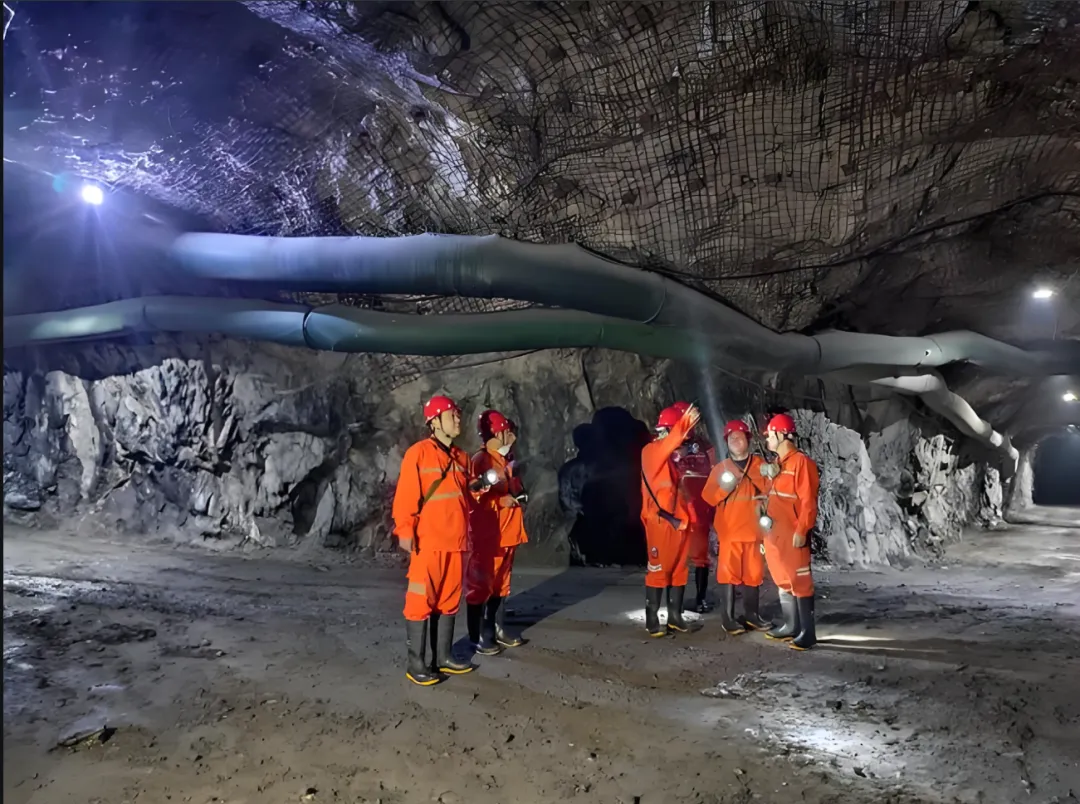
A suitably located development roadway can significantly reduce ore transportation costs, improve transportation efficiency, and reduce energy consumption. At the same time, it can also ensure good mine ventilation, reduce the concentration of harmful gases underground, and create a safe and comfortable working environment for personnel. However, if the location of the development roadway is improperly selected, it will lead to excessively long transportation routes and increased transportation difficulties, resulting in a significant increase in transportation costs and even potentially causing safety accidents, posing a serious threat to the normal production of the mine. Therefore, in the design and implementation of mining engineering, it is crucial to comprehensively consider various factors and accurately and scientifically select the location of the development roadway to ensure the efficient, safe, and economical operation of mining operations. This deserves our high attention and in-depth research.
Topography and Geology
The Influence of Mine Area Topography
Mine area topography varies greatly. Different terrains such as mountains, plains, and hills have significant limitations and requirements on the selection of development roadway locations. In mountainous terrain, factors such as the slope and undulation of the mountain, as well as the distribution of valleys and ridges, need to be carefully considered. For example, to effectively avoid threats to the development roadway from geological disasters such as landslides and debris flows, we must stay away from areas with unstable geological conditions. The rocks in these areas may be more fragmented, and the stability of the soil is poor. Once affected by factors such as heavy rainfall or earthquakes, landslides are likely to occur, posing a huge hidden danger to the safety of the roadway.
At the same time, when selecting the location of the development roadway in mountainous areas, the impact of topography on transportation routes must be fully considered. We should strive to ensure a smooth connection between the roadway and the surface transportation routes, reducing the changes in elevation and the number of bends during transportation, thereby reducing transportation costs and improving transportation efficiency. For example, when arranging the roadway exit in a valley area, it is necessary to ensure that there is sufficient space at the exit to arrange the marshalling yard and stockpile yard for the loading and transportation of ore. In plain areas, although the terrain is relatively flat and the construction difficulty is relatively small, factors such as groundwater level and soil bearing capacity must also be considered. If the groundwater level is too high, it may cause roadway waterlogging, affecting the stability and normal use of the roadway. Therefore, when selecting the roadway location, areas with lower groundwater levels and stronger soil bearing capacity should be selected to ensure the safety and stability of the roadway.
Geological Structure and Orebody Burial Conditions
Geological structure and orebody burial conditions are core factors affecting the layout of development roadways. Geological structures such as folds, faults, and joints can damage the integrity and stability of rocks, increasing the difficulty of roadway construction and maintenance. In folded areas, the bending and deformation of rock layers can lead to uneven stress on the rocks, easily causing rock fragmentation and collapse. Therefore, when laying out roadways, it is necessary to avoid stress concentration areas such as the axial parts of folds and choose to lay out roadways in relatively stable parts such as the flanks of folds.
Faults are more complex geological structures. They not only cause rock layers to move, but can also lead to rock fragmentation and groundwater gushing. If the development roadway crosses a fault, special support measures and waterproofing measures must be taken to ensure the safety of the roadway. For example, reinforced support can be used at the fault, such as increasing the number and length of anchor rods and anchor cables, or using concrete pouring to reinforce the roadway. At the same time, waterproofing work must be done to prevent groundwater from entering the roadway and affecting its normal use.
The depth, strike, and dip of the orebody directly determine the layout and direction of the development roadway. In order to minimize ore loss and depletion and improve mining efficiency, the layout of the roadway must closely match the shape and occurrence of the orebody. When the orebody is buried deep, a vertical shaft development method may be needed to ensure that the orebody can be reached smoothly. When the strike and dip of the orebody change, the layout of the roadway also needs to be adjusted accordingly to ensure that the ore can be effectively mined. In actual work, we need to conduct detailed geological exploration to obtain accurate geological structure and orebody burial information, use advanced technical means and scientific methods to optimize the design of the roadway layout plan, so as to ensure that the layout of the development roadway is both in line with geological conditions and meets the needs of mining production.
Production and Exploration
Mine Production Capacity and Service Life
Mine production capacity and service life play a crucial role in the selection of development roadway locations. Mines with different production capacities and service lives have significantly different requirements for development roadways.
Large, long-term mines typically have large production scales and long service lives. The layout of their development roadways must fully consider long-term stability and efficiency. The development roadways of such mines often need to handle a large amount of ore transportation, so the transportation distance should be minimized to reduce transportation costs. To achieve this goal, development roadways are usually located in the central part of the orebody, so that the transportation work of the ore is minimized. For example, in some large metal mines, vertical shafts are located in the center of the orebody, connected to various mining stages through staged stopes, forming an efficient transportation network, greatly improving the efficiency of ore transportation. At the same time, due to the long service life, the stability of the roadway is crucial, and it is necessary to choose areas with stable geological conditions and strong rocks to reduce the workload and cost of roadway maintenance. In some mining areas with complex geological conditions, advanced support technologies and monitoring methods will be used to ensure the safety and stability of the roadway during long-term use.
In contrast, small, short-term mines, due to their smaller production scale and shorter service life, can simplify the development system to some extent and reduce infrastructure costs. For some small mines with smaller reserves, a flank development method can be used, utilizing the terrain conditions on one side of the orebody to directly transport the ore to the surface, reducing the amount of engineering work for the development roadway. The layout of development roadways in small mines is relatively flexible and can be adjusted according to the actual situation to adapt to changes in the orebody and mining needs. However, while simplifying, the basic requirements of safety and production cannot be ignored. It is necessary to ensure that the roadway can meet the basic functions of ventilation and drainage.
The Role of Ore Deposit Exploration Degree
The degree of ore deposit exploration is an important basis for determining the location of the development roadway. It is directly related to our understanding of the shape, scale, occurrence, and geological structure of the orebody.
When exploration is insufficient, there are many uncertainties in our understanding of the ore body, which makes it very difficult to determine the location of the development roadway. In this case, in order to reduce risks, we need to reserve some adjustment space. For example, when the exploration of the ore body boundary is not accurate enough, the layout of the development roadway should not be too close to the ore body boundary, so as to avoid the inability to use the roadway or the need for a large amount of transformation due to changes in the ore body discovered in the subsequent mining process. The distance between the roadway and the ore body boundary can be appropriately increased, or some temporary development roadways can be used. After the exploration work is further deepened and a more accurate understanding of the ore body is obtained, the permanent roadway can be arranged. In some early exploration mines, due to limited understanding of the deep part of the ore body, a simple inclined shaft development method was first adopted. As the exploration deepens, the development system is optimized and improved based on new geological data.
When the exploration level is too high, although we have a very detailed understanding of the ore body information, it may also lead to increased development costs due to excessive pursuit of accuracy. When determining the location of the development roadway, we should comprehensively consider the relationship between exploration cost and development cost, and avoid resource waste caused by excessive exploration. For example, in some mining areas where a large amount of exploration work has been carried out, although every detail of the ore body is known, when choosing the location of the development roadway, we should still proceed from an economically reasonable perspective and not simply choose a high-cost scheme to meet the accuracy of exploration. Under the premise of ensuring safe production and efficient mining, we should make full use of the existing exploration results and choose the optimal location for the development roadway. In short, the degree of ore deposit exploration and the determination of the development roadway location are interrelated and mutually influential. We should find a balance between the two to achieve the sustainable development of the mine.
Environment and Safety
Rock Properties and Hydrogeology
Rock properties and hydrogeological conditions are important factors that cannot be ignored in the selection of the location of the development roadway. Different rock properties, such as soft rock and hard rock, have a significant impact on the stability and construction difficulty of the roadway. Soft rock has low strength, large deformation, and easy weathering. It is easy to cause roadway deformation and collapse when advancing roadways in soft rock, which brings great challenges to construction and later maintenance. In some soft rock formations rich in clay minerals, after the roadway is excavated, due to the expansibility of the rock, the surrounding rock pressure of the roadway will increase, and the roadway section will shrink, seriously affecting the normal use of the roadway. Therefore, when arranging development roadways in soft rock areas, special support methods need to be adopted, such as increasing support strength and using shrinkable support, to improve the stability of the roadway. At the same time, the monitoring of the surrounding rock of the roadway should be strengthened to find and deal with roadway deformation problems in time.
Although hard rock has higher strength, in the case of well-developed joints and fissures, it will also reduce the integrity and stability of the rock and increase the construction difficulty. When advancing roadways in hard rock, problems such as rock breakage and collapse may be encountered. Appropriate blasting parameters and construction methods need to be adopted to reduce the damage to the rock. In some hard rock mining areas with dense joints and fissures, smooth blasting technology can effectively control the impact of blasting on the surrounding rock and reduce the degree of rock breakage. In addition, appropriate excavation equipment should be selected according to the properties of the rock to improve construction efficiency.
The existence of groundwater will also have an adverse impact on roadway stability. Groundwater may soften the rock, reduce the strength of the rock, and increase the risk of roadway collapse. Groundwater may also cause roadway water accumulation, affecting construction progress and personnel safety. In areas with high groundwater levels, water gushing may occur during roadway construction. If not handled in time, it will cause the roadway to be flooded, equipment damage, and even endanger the safety of personnel. Therefore, when selecting the location of the development roadway, it is necessary to fully understand the hydrogeological conditions of the mining area and adopt effective waterproof and drainage measures. Facilities such as waterproof gates and drainage pump stations can be set up to ensure the safety of the roadway during construction and use.
Ground Hazards and Flood Levels
Ground hazards and flood levels are important external factors affecting the safety of development roadways. Ground hazards such as slope landslides, collapses, and avalanches may directly destroy development roadways and related facilities, causing serious casualties and property losses. In mountain mining, the stability of the mountain body is crucial. If the development roadway is located in an unstable area of the slope, once a landslide or other hazard occurs, the roadway will be buried, leading to mine shutdown. In order to avoid the impact of these hazards, when selecting the location of the development roadway, a detailed survey of the topography and geomorphology of the mining area should be carried out to assess the possibility of ground hazards. Sections prone to landslides and collapses should be avoided, and areas with stable geological conditions should be selected for roadway layout. Retaining walls and slope protection facilities should be set up around the roadway exit to enhance resistance to ground hazards.
Ensuring that the elevation of the shaft and roadway exit is more than 3m above the highest historical flood level is an important measure to ensure the safety of the development roadway. If the elevation of the shaft and roadway exit is lower than the highest flood level, the roadway may be submerged in the event of a flood, leading to equipment damage, ore loss, and even gas explosions in the mine. In some mining areas near rivers, the threat of floods is particularly serious. To meet this requirement, when carrying out mine planning, it is necessary to fully collect local hydrological data and accurately determine the highest historical flood level. When designing the shaft and roadway exit, the elevation should be reasonably determined according to the highest flood level, and corresponding flood control measures should be adopted, such as building flood control dykes and setting up drainage channels, to ensure that flood water will not backflow into the roadway. At the same time, flood control facilities should be regularly inspected and maintained to ensure that they can play their role at critical moments.
Other Key Factors
Avoid Ore Crushing and Leave Safety Ore Pillars
Avoiding ore crushing at the shaft (or adit) location is a necessary requirement for reasonable resource utilization and ensuring the sustainable development of the mine. If the shaft (or adit) crushes ore, it will lead to the inability to mine part of the ore body, resulting in resource waste. In some mines with limited ore reserves, ore crushing may shorten the service life of the mine, increase mining costs, and reduce economic benefits. In order to avoid ore crushing, we should use accurate geological exploration to determine the accurate boundaries and scope of the ore body, and use advanced three-dimensional modeling technology to visually display the shape and spatial location of the ore body, thus providing a scientific basis for the selection of the development roadway location. During the design process, we must strictly follow the normative requirements to ensure that the shaft (or adit) is located outside the safe distance of the ore body.
However, under certain special circumstances, when the shaft (or adit) cannot completely avoid the ore body, it is necessary to leave safety ore pillars. The setting of safety ore pillars must follow strict principles to ensure that they can effectively support the roof, prevent surrounding rock movement and collapse, and ensure the safe production of the mine. The shape and size of the safety ore pillars should be determined comprehensively based on factors such as the thickness, dip angle, rock properties, and mining depth of the ore body. Generally speaking, the width and height of the safety ore pillars must meet a certain safety factor to ensure their stability throughout the mining process.
Common methods for calculating the dimensions of safety pillars include empirical formulas and numerical simulation. Empirical formulas are summarized from extensive engineering practices and have certain reference value. The minimum width of a safety pillar can be calculated using specific formulas based on the thickness of the ore body and the rock strength coefficient. Numerical simulation uses computer software to simulate the mining process, analyzing the stress and displacement changes of the surrounding rock under different safety pillar dimensions to determine the optimal size. Numerical simulation allows for a visual understanding of the stress and deformation trends of the safety pillar during mining, providing a more accurate basis for its design. In practice, we usually combine the two methods for mutual verification to ensure that the safety pillar design is both safe, reliable, and economically feasible.
Industrial Site and Utilization of Existing Facilities
The mine entrance requires a sufficient industrial site, which is a fundamental condition for normal mine production and operation. A sufficient industrial site provides space for various buildings, marshalling yards, and stockyards, ensuring a smooth mine production process. Within the industrial site, it is necessary to construct buildings such as concentrators, repair shops, and warehouses to meet the needs of ore processing, equipment maintenance, and material storage. The marshalling yard is a key facility for ensuring efficient and orderly transportation of ore and equipment; it enables vehicle scheduling, grouping, and loading and unloading operations. Stockyards are used for temporary storage of ore, waste rock, and other materials, facilitating subsequent processing and transportation. Insufficient industrial space can lead to crowded building layouts and the inability to use marshalling yards and stockyards properly, thus affecting mine production efficiency and safety. In some small mines, due to narrow industrial sites, the distance between the concentrator and the warehouse is too close, resulting in narrow transportation channels and difficult vehicle passage, not only reducing transportation efficiency but also increasing safety hazards. Therefore, when choosing the location of the mine entrance, the needs of the industrial site must be fully considered to ensure sufficient space to meet the production and operational needs of the mine.
When reconstructing or expanding a mine, making full use of existing facilities can significantly reduce infrastructure costs, shorten construction time, and improve the mine's economic efficiency. Existing mine shafts, buildings, and structures, after years of use and maintenance, already have a certain foundation and conditions. If these facilities can be used rationally, the amount of engineering and investment in new facilities can be reduced. Extending or modifying existing mine shafts can avoid the huge costs and risks of re-excavating shafts. Utilizing existing buildings as offices or warehouses can also save on the cost and time of constructing new buildings. To better utilize existing facilities, a comprehensive assessment and inspection of these facilities is needed to understand their structural condition, performance, and safety hazards. Based on the assessment results, a reasonable utilization plan should be developed, and necessary modifications and upgrades should be made to the existing facilities to meet new production requirements. When utilizing existing mine shafts, the support, ventilation, and drainage systems of the shafts should be inspected and maintained to ensure their safety and reliability. At the same time, the cross-sectional dimensions, slope, etc., of the shafts should be optimized in combination with new mining processes and equipment to improve the transportation capacity and efficiency of the shafts. In short, the rational utilization of existing facilities is an important measure to achieve resource conservation and efficiency improvement in mine reconstruction and expansion.
Summary
In summary, selecting the location of the main access roadway is a complex and crucial decision-making process that requires comprehensive consideration of numerous factors. From the mine area's topography, geological structure, and ore body burial conditions, to the mine's production capacity and service life of the roadways, and the exploration level of the ore deposit, each factor has a significant impact on the location selection of the access roadway. Factors such as rock properties and hydrogeological conditions, ground hazards and flood levels, and other factors such as avoiding ore pressure, leaving safety pillars, industrial sites, and utilizing existing facilities, should not be overlooked.
Note: Part of the article refers to the courseware of "Underground Mining of Metal Deposits" by Xu Shuai and An Long from Northeastern University's online course.
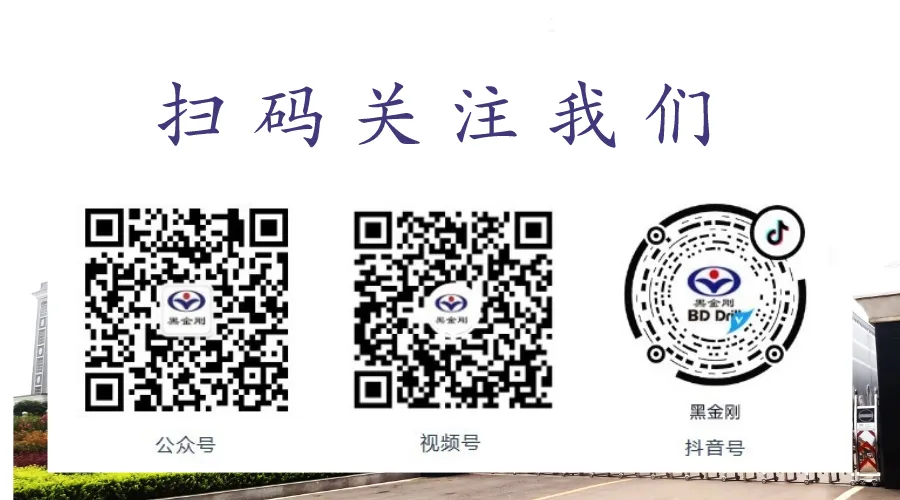