
Mining Area Production Capacity - Black King Kong Report
Preface
In the grand scheme of mining production, the production capacity of mining sections plays a pivotal role and is a key factor in measuring mine efficiency and planning. It is like the “ power engine ” ” of mine operation, directly determining the output scale of the mine per unit of time and having a profound impact on the mine's economic efficiency. If a mine is compared to a complex ecosystem, the production capacity of the mining section is the core pillar, supporting the stable operation and development of the entire mine. From the perspective of resource utilization, reasonable and efficient mining section production capacity can ensure that mineral resources are fully and reasonably developed, avoiding resource waste and idleness, so that every precious mineral resource can exert its maximum value. In today's increasingly fierce market competition, mining section production capacity has become a key competitive advantage for mines to establish themselves and develop in the market. Mines with higher production capacity can be more resilient to market fluctuations, respond promptly to market demand, provide sufficient mineral product supply, and thus win market share and customer trust. Therefore, in-depth exploration of the calculation methods of mining section production capacity is of vital significance to the scientific planning and efficient operation of mining production. It will provide a solid theoretical basis and practical guidance for the sustainable development of mines.
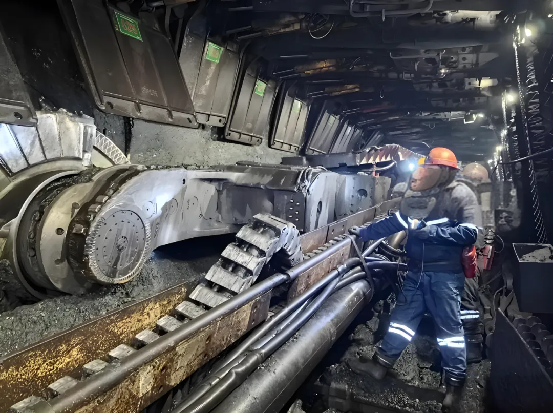
Basic Data and Formula
As an important component of mining section production capacity, the calculation of working face production capacity relies on a key formula: A₀ = L·V₀·m·γ·C₀ . This formula is like a precise key that unlocks the mystery of working face production capacity. Each parameter carries a unique meaning, weaving together the calculation system of working face production capacity.
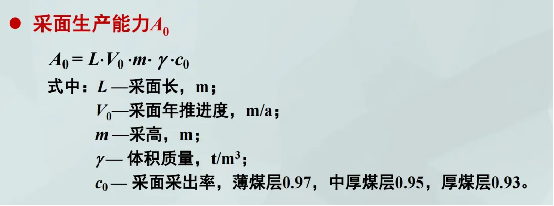
(Image from MOOC China University of Mining and Technology Mining Engineering Tu Shihao, Fang Zhijun, Zheng Xigui, Wang Xufeng, Peng Hongge, Yuan Yong )
Working face length L (Unit: m ), refers to the length of the coal mining working face. It is the basic spatial scale of working face production. Just like the length of a field, the longer the length, under the same planting and management conditions, the theoretically higher the output may be. In actual coal mining operations, the working face length is restricted by various factors such as geological conditions, mining technology, and equipment matching. For example, in areas with complex geological structures and many faults, the working face length may be limited to ensure the safety and stability of mining.
Annual advance rate of working face V₀ (Unit: m/a ), reflects the distance the coal mining working face advances in one year. This parameter is like the speed of a car; the faster the speed, the farther the distance traveled in a certain amount of time. The annual advance rate of the working face directly affects the amount of coal mined. It is closely related to the coal mining process, equipment performance, and the workers' operating proficiency. Using advanced fully mechanized mining equipment and efficient coal mining processes can improve the annual advance rate of the working face and thus increase the production capacity of the working face.
Mining height m (Unit: m ), indicates the thickness of the coal seam mined at one time. It is similar to the height of crops that farmers plant and harvest each time. The size of the mining height not only determines the amount of coal mined in a single mining operation but is also closely related to top-coal management and mining costs. In thick coal seam mining, reasonably determining the mining height is crucial for improving resource recovery rate and ensuring mining safety. If the mining height is too large, it may lead to increased top-coal pressure, increasing the difficulty and risk of top-coal management; conversely, if the mining height is too small, it will reduce resource utilization.
Bulk density γ (Unit: t/m³ ), that is, the density of coal, which reflects the mass of coal per unit volume. This is like substances with different densities, with different masses under the same volume. The density of coal is a relatively stable physical parameter, but it will vary due to differences in coal type, origin, and coal quality. When calculating the production capacity of a working face, accurately obtaining the density data of coal is one of the keys to ensuring the accuracy of the calculation results.
Working face extraction rate C₀ , is an important indicator for measuring the efficiency of coal resource mining. The extraction rate of thin coal seams is generally 0.97 , medium-thick coal seams is 0.95 , and thick coal seams is 0.93 . It reflects the ratio of the actual amount of coal mined to the coal seam reserves during the mining process, like the harvest ratio of farmers harvesting crops. The higher the extraction rate, the more fully the coal resources are utilized, and the less waste there is. Improving the working face extraction rate requires comprehensive consideration of mining technology, top-coal management, and backfilling processes, and it can be achieved by optimizing mining schemes and strengthening production management.
These parameters are interrelated and influence each other, jointly determining the production capacity of the working face. In actual mining production, it is necessary to accurately determine the values of these parameters based on specific geological conditions, mining technology, and equipment conditions to scientifically and reasonably calculate the production capacity of the working face, providing solid data support for the production planning and decision-making of the mining section.
Number of simultaneously mined working faces in the mining section
Determining the number of simultaneously mined working faces in a mining section is like arranging the meshing of gears in a precise mechanical clock. It is a crucial and rigorous step that has a profound impact on the production capacity of the mining section, like the foundation stone to a tall building. Under different coal seam conditions, relevant regulations have clearly defined the limits for the number of simultaneously mined working faces in a mining section. These regulations stem from a deep consideration of safe production, reasonable resource utilization, and efficient mining.
Coal Mine Safety Regulations 2016 Article 48 of the edition clearly stipulates that: In one mining section, at most 1 retreating working faces and 2 advancing working faces can operate simultaneously on one wing of the same coal seam; for double-wing mining or multi-seam mining in one mining section, at most 2 retreating working faces and 4 Multiple development faces operate simultaneously; it is strictly prohibited to arrange another coal mining face within the coal mining face for simultaneous operation. These regulations are like a solid safety line, ensuring the orderly and safe production of the mining area. In actual coal mining operations, adhering to these regulations is a basic prerequisite for ensuring personnel safety and smooth production. For example, in a mining area of a certain coal mine, the number of simultaneously operating faces is strictly controlled according to regulations, allowing the ventilation system to operate stably, and the methane concentration is effectively controlled, thus avoiding safety hazards such as poor ventilation and methane accumulation caused by too many faces.
For gently inclined coal seams, fully mechanized mining and ordinary mining generally have 1-2 simultaneously operating faces. Fully mechanized mining technology, with its highly mechanized and automated features, such as the collaborative operation of advanced coal cutters, scraper conveyors, and hydraulic supports, can achieve efficient coal mining. In this case, 1-2 simultaneously operating faces can fully utilize equipment efficiency while ensuring safe and stable production. Although ordinary mining technology has a relatively low degree of mechanization, with reasonable face layout and personnel organization, 1-2 simultaneously operating faces can also achieve good production results.
When blasting in steeply inclined coal seams, it is also 1-2 simultaneously operating faces. The mining conditions of steeply inclined coal seams are more complex, with a large coal seam dip angle, high difficulty in top management, and many challenges in coal transportation. In this case, strictly controlling the number of simultaneously operating faces can better cope with safety risks during the mining process and ensure smooth production. For example, in the mining of steeply inclined coal seams, reducing the number of simultaneously operating faces can reduce the risk of top collapse and facilitate the adoption of effective support measures and coal transportation schemes.
The limitation on the number of simultaneously operating faces in a mining area has a direct and significant impact on the mining area's production capacity. On the one hand, an appropriate number of simultaneously operating faces can ensure the continuity and stability of mining area production, avoiding excessive dispersion of equipment, manpower, and resources due to too many faces, thereby improving production efficiency. For example, when there are too many simultaneously operating faces, there may be difficulties in equipment allocation, personnel shortages, and increased pressure on ventilation and transportation systems, which in turn will affect production capacity. On the other hand, a reasonable number of simultaneously operating faces can also fully utilize the advantages of various coal mining technologies and equipment, achieving efficient coal resource mining. If the number of simultaneously operating faces is too small, the production capacity of the equipment may not be fully utilized, leading to resource waste and low production efficiency.
In the actual mining area production planning, relevant regulations must be strictly followed, comprehensively considering coal seam conditions, coal mining technology, equipment capacity, and safety factors, etc., to scientifically and reasonably determine the number of simultaneously operating faces in the mining area to achieve the maximization of mining area production capacity and the goal of safe production. For example, in the mining area design of a certain large coal mine, through a detailed analysis of coal seam occurrence conditions, geological structures, and coal mining technology, the number of simultaneously operating faces was reasonably determined, and advanced fully mechanized mining equipment and efficient coal mining technology were used, resulting in a significant increase in mining area production capacity while ensuring safe and stable production.
Comprehensive Calculation of Mining Area Production Capacity

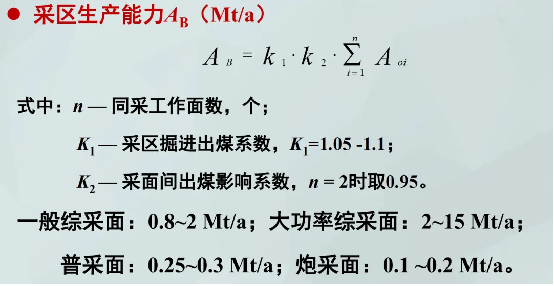
(Image from MOOC China University of Mining and Technology Mining Engineering Tu Shihao, Fang Zhijun, Zheng Xigui, Wang Xufeng, Peng Hongge, Yuan Yong )
In this formula, k1 represents the coal output coefficient of the mining area, and the value range is usually between 1.05 - 1.1 It reflects the coal output during the mining process and is a quantitative reflection of the relationship between mining work and coal output. Mining work is not only to open up new coal mining space, but also involves a certain amount of coal output. The existence of the mining area coal output coefficient allows us to fully consider the contribution of mining work to coal output when calculating the mining area production capacity. In the production of a certain coal mine mining area, through detailed statistics and analysis of mining work, the mining area's coal output coefficient was determined to be 1.08 . This means that when calculating the mining area production capacity, the coal output from mining work will be calculated and considered according to this coefficient.
k2 is the coal output influence coefficient between faces. When the number of simultaneously operating faces n = 2 generally takes 0.95 . This coefficient reveals the mutual influence on coal output when multiple coal mining faces operate simultaneously. In actual coal mining operations, when multiple faces are producing simultaneously, due to limitations in equipment allocation, personnel cooperation, and the carrying capacity of the transportation system, the coal output of each face is not a simple superposition. The introduction of the coal output influence coefficient between faces can more accurately reflect this actual situation and make the calculation of mining area production capacity closer to actual production. For example, in a mining area with two fully mechanized mining faces operating simultaneously, due to certain mutual influences between the two faces in equipment use and coal transportation, by using 0.95 coal output influence coefficient, the actual coal output capacity of the two faces working together can be reasonably calculated.

is the basic data for calculating mining area production capacity; it directly reflects the production capacity of each coal mining face. The output of faces with different coal mining technologies has significant differences. Generally, the output range of fully mechanized mining faces is between 0.8 - 2 Mt/a and the output of high-power fully mechanized mining faces can reach 2 - 15 Mt/a , the output of ordinary mining faces is 0.25 - 0.3 Mt/a , and the output of blasting faces is 0.1 - 0.2 Mt/a . In a mining area of a large coal mine, high-power fully mechanized mining equipment was equipped, and the output of its fully mechanized mining face was as high as 8 Mt/a . In another small coal mine, the output of the face using ordinary mining technology was stable at 0.28 Mt/a or so.
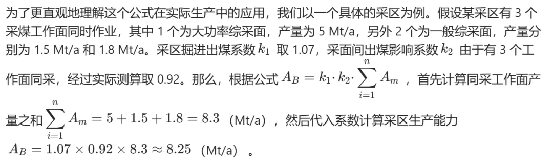
In actual production, the calculation of mining area production capacity is not static but needs to be dynamically adjusted according to the actual situation. Factors such as changes in geological conditions, equipment upgrades and renovations, optimization of coal mining processes, and improvement of personnel operating skills will all affect the mining area's production capacity. Therefore, in daily production management, it is necessary to closely monitor changes in these factors and adjust the calculation parameters of the mining area's production capacity in a timely manner to ensure the accuracy and reliability of the calculation results. For example, when a mining area encounters an area with complex geological structures during mining, and the advancement speed of the coal mining working face is affected, it is necessary to re-evaluate the output of the working face and adjust the calculation of the mining area's production capacity accordingly.

Comparison of Production Capacity of Different Coal Mining Methods
In the field of coal mining, coal mining technology is like the “ brain ” of mine production, and its technological level and operation methods play a decisive role in the production capacity of the mining area. Different coal mining methods show significant differences in production capacity.
The production capacity range of a general fully mechanized mining face is usually between 0.8 - 2 Mt/a It uses a comprehensive mechanized coal mining process, integrating coal mining machines, scraper conveyors, and hydraulic supports, etc., to achieve mechanized operations for the main processes of coal mining, such as coal breaking, loading, transportation, support, and goaf treatment. This process is suitable for areas with relatively stable coal seam conditions and relatively simple geological structures. In a fully mechanized mining face of a certain coal mine, the coal seam thickness is stable at 2 - 3 meters, the geological structure is simple, and a general fully mechanized mining process is used, equipped with advanced coal mining machines and scraper conveyors. Its annual production capacity is stable at 1.5 Mt/a or so.
The production capacity of a high-power fully mechanized mining face is even more considerable, reaching 2 - 15 Mt/a . High-power fully mechanized equipment further improves the power and performance of general fully mechanized equipment, such as high-power coal mining machines, scraper conveyors, and high-strength hydraulic supports. These equipment have stronger rock-breaking capabilities, higher cutting speeds, and greater transportation capacity, enabling them to adapt to more complex geological conditions and larger-scale coal mining. In some large coal mines of the Shenhua Group, using high-power fully mechanized equipment in mining areas with relatively thick coal seams and relatively stable geological conditions, the annual production capacity of the fully mechanized mining face is as high as 8 - 10 Mt/a , greatly improving coal mining efficiency and output.
The production capacity of ordinary mining faces is relatively low, at 0.25 - 0.3 Mt/a . The ordinary mechanized coal mining process mainly uses coal mining machines, flexible chain plate conveyors, and friction-type metal supports and metal roof beams. Although it has achieved mechanization of coal dropping and loading processes, it still requires a lot of manual operation in aspects such as roof support and goaf treatment. This process is suitable for areas with thinner coal seams, more complex geological conditions, and unsuitable for large-scale mechanized mining. In some small coal mines, due to the thin coal seams and complex geological structures, the ordinary mining process is used. Although the production capacity is limited, it can flexibly adjust the mining method according to the actual situation to ensure coal mining.
The production capacity range of blasting mining faces is 0.1 - 0.2 Mt/a , which is the lowest among several coal mining processes. The blasting mining process uses blasting to drop coal, and then manually or mechanically loads and transports coal. In terms of support, single pillars are generally used for on-site support. This process has low equipment requirements and a relatively simple process, but it has high labor intensity, low production efficiency, and high safety risks. In some small coal mines with small reserves and poor mining conditions, blasting mining may be used, but with the development of the coal industry and the improvement of safety standards, the application range of blasting mining is gradually shrinking.
The differences in production capacity among different coal mining methods mainly stem from factors such as the degree of equipment mechanization, rock-breaking ability, cutting speed, and adaptability to geological conditions. General fully mechanized mining faces and high-power fully mechanized mining faces, with their high degree of mechanization and advanced equipment, can achieve efficient coal mining and are suitable for large-scale, modern coal mine production; while ordinary mining faces and blasting mining faces, due to their lower degree of mechanization, have relatively limited production efficiency and capacity, and are more suitable for use in some special geological conditions or small-scale mining.
In actual coal mining, coal mining enterprises need to comprehensively consider various factors such as their own geological conditions, resource reserves, equipment investment capacity, and safety production requirements to choose the appropriate coal mining method to maximize the mining area's production capacity and optimize economic benefits. For example, in large coal mines with good coal seam conditions and abundant resources, high-power fully mechanized mining processes are prioritized to fully utilize the advantages of equipment and improve coal output and enterprise economic benefits; while in some small coal mines with complex geological conditions and large coal seam thickness variations, ordinary mining or blasting mining processes may be more adaptable and economical.
Summary
The precise calculation of mining area production capacity is like drawing a precise navigation map for mine production, which is a core element for the efficient, safe, and sustainable development of mines. Through an in-depth analysis of the parameters in the working face production capacity formula A₀ = L·V₀·m·γ·C₀ , we have clarified the decisive role of factors such as working face length, annual working face advancement rate, mining height, volume mass, and working face extraction rate on working face production capacity. These parameters are intertwined and together constitute the basis for calculating working face production capacity. Every subtle change in them may have a significant impact on the production capacity of the working face.
The strict limitation of the number of simultaneously operating working faces in a mining area is an important line of defense for ensuring mine safety production and rational resource utilization. The relevant regulations of the 2016 version of the "Coal Mine Safety Regulations" clearly define the limits on the number of simultaneously operating working faces in a mining area. Under different coal seam conditions, such as gently inclined coal seams and steeply inclined coal seams, there are clear requirements for the number of simultaneously operating working faces. These regulations not only ensure the orderly progress of mining area production but also avoid safety hazards and resource waste caused by too many working faces.
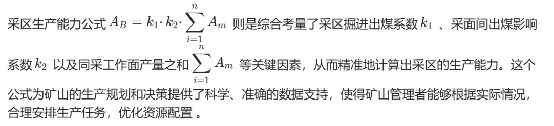
The huge difference in production capacity among different coal mining methods also provides an important reference for mine production process selection. General fully mechanized mining faces, high-power fully mechanized mining faces, ordinary mining faces, and blasting mining faces each have their applicable scenarios and production capacity characteristics. In actual coal mining, coal mining enterprises need to comprehensively consider various factors such as geological conditions, resource reserves, equipment investment capacity, and safety production requirements to carefully select the appropriate coal mining method to maximize the mining area's production capacity and optimize economic benefits.
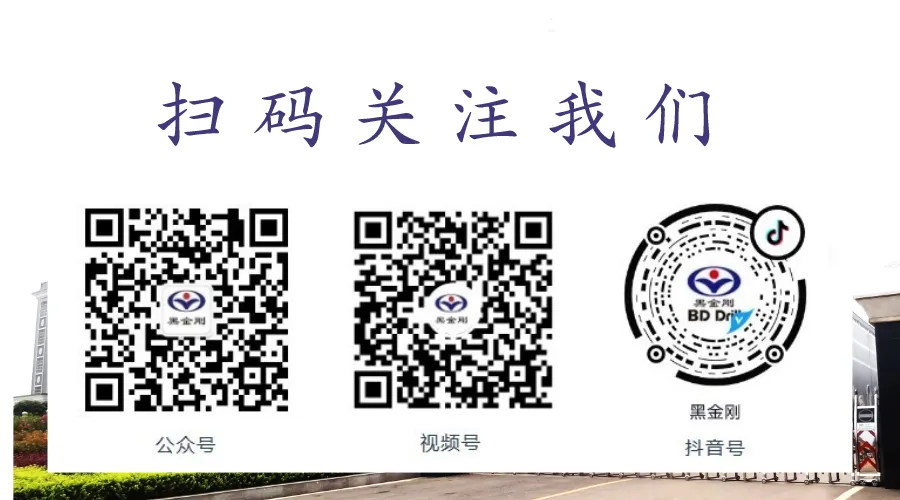
Reference: MOOC China University of Mining and Technology Mining Engineering Course materials by Tu Shihao, Fang Zhijun, Zheng Xigui, Wang Xufeng, Peng Hongge, and Yuan Yong )