
Selection of the wellbore vertical orebody strike position - Black King Kong broadcast
Preface
In the field of mining engineering, shafts serve as crucial passageways connecting the surface and underground ore bodies. Their location selection is fundamental to the entire mining operation, akin to the cornerstone of a building. Determining the shaft's vertical position relative to the ore body's trend is not a simple matter of site selection, but a comprehensive decision-making process. Its rationality is closely related to core elements such as mining efficiency, cost control, and operational safety.
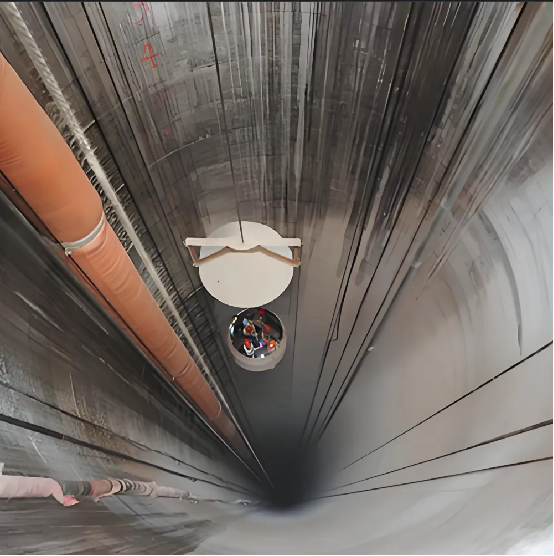
From the perspective of mining efficiency, a proper shaft location can create a more efficient underground transportation system. For example, at a certain metal mine, due to the shaft's location being offset from the ore body's center in early planning, the ore transportation routes were lengthy and complex, resulting in a significant increase in energy consumption of transportation equipment and extremely low transportation efficiency. After re-optimizing the shaft location, the transportation distance was significantly shortened, and transportation efficiency increased by nearly 30% , resulting in a qualitative leap in the overall mining efficiency of the mine. This fully demonstrates that a reasonable shaft position vertically aligned with the ore body's trend can greatly optimize the transportation process, reduce the turnover time of ore underground, and thus provide strong support for efficient mining.
In terms of cost control, the shaft location directly affects both construction costs and operating costs. The choice of shaft location determines the length and difficulty of the mine shaft engineering. If the shaft location is inappropriate, longer tunnels may need to be excavated, increasing the difficulty of support, which will undoubtedly significantly increase the construction investment. At the same time, during subsequent operations, transportation costs, ventilation costs, etc., will remain high due to the unreasonable shaft location. Conversely, scientifically selecting the shaft location can effectively shorten the tunnel length, reduce support costs, and optimize the ventilation system, reducing energy consumption, thereby achieving effective control of life-cycle costs.
Safety is paramount. As a passageway for personnel, equipment, and materials, the shaft's location is crucial to the overall safety of the mine. If the shaft is located in a geologically unstable area, such as near a fault or an area significantly affected by mining activities, it is very easy to cause shaft deformation and collapse during mining, seriously threatening the safety of personnel and mine property. In addition, the shaft location must also consider its relative position to surface buildings and structures to avoid damaging surface facilities during mining and causing secondary disasters.
Key Concept Analysis
(1) Surface Movement Zone and Protection Zone
The formation of the surface movement zone originates from underground mining activities. When the ore body is mined, the surrounding rock mass, which was originally in equilibrium, loses its support, and the stress redistributes, causing the rock mass to move and deform. This deformation is transmitted upwards, ultimately causing surface movement and subsidence, forming the surface movement zone. Determining its range is a complex process that requires consideration of multiple factors. Geological conditions are one of the key factors, including the mechanical properties of rocks and geological structures. Different rock mechanical properties determine their deformation characteristics and degree of damage under mining influence. For example, hard rocks may exhibit smaller deformations in the initial stages of mining, but as mining progresses, once their strength limit is reached, sudden collapse may occur, causing the surface movement range to expand rapidly; while weak rocks may produce larger deformations in the initial stages of mining, and the surface movement range is relatively easier to determine. Geological structures such as faults and folds change the integrity and stress transmission path of the rock mass, making the range and morphology of the surface movement zone more complex. Mining methods also have a significant impact on the range of the surface movement zone. Different mining methods, such as open-pit mining, backfilling mining, and caving mining, have different degrees and methods of rock damage. After the goaf is formed in open-pit mining, if it is not dealt with in time, as the goaf expands, the stability of the rock mass gradually decreases, and the range of the surface movement zone will continue to expand; backfilling mining effectively supports the rock mass by filling the goaf with materials, reducing rock deformation and movement, thereby limiting the range of the surface movement zone; caving mining artificially causes the overlying strata to collapse to control ground pressure and handle the goaf, and this method usually leads to a larger range of surface movement.
The protection zone refers to a safety distance area of a certain width set outside the surface movement boundary to ensure the safety of shafts and surrounding structures and buildings within the surface movement zone. Its role is crucial; it is an important defense line for ensuring safe mining production and the stability of ground facilities. From a safety perspective, the protection zone can effectively prevent damage to shafts and surrounding structures and buildings caused by surface movement. During surface movement, ground subsidence, cracks, and tilting may occur, which may seriously damage shafts and ground facilities, affecting normal mine production and personnel safety. The existence of the protection zone can, to a certain extent, buffer the impact of surface movement and provide safety protection for shafts and ground facilities. From the perspective of production continuity, the setting of the protection zone helps maintain the stability of mine production. If shafts and surrounding structures and buildings are damaged by surface movement, it may take a lot of time and money to repair, and may even lead to interruptions in mine production. The reasonable setting of the protection zone can reduce this risk, ensure the smooth progress of mine production, and improve production efficiency.
(2) Protection Level Classification
The classification of protection levels is the result of comprehensive consideration of multiple factors, including the use, service life, and protection requirements of buildings and structures. Use is one of the important bases for classifying protection levels. For buildings and structures that play a key role in mine production, such as hoisting shafts, derricks, and hoisting machine rooms, they are directly related to ore hoisting and transportation. Once damaged, they will lead to the stagnation of the entire mine production, so their protection level is usually higher; while some secondary buildings and structures, such as temporary warehouses and simple sheds, have a relatively small impact on mine production, and their protection level is relatively lower. Service life is also an important factor. Buildings and structures with a long service life need to ensure their safety and stability during their use, so they need to be given a higher protection level; while temporary facilities with a shorter service life can have a lower protection level due to their limited use time. Protection requirements are determined based on the importance of buildings and structures and the consequences that may arise if they are damaged. For buildings and structures that may cause major casualties or significant economic losses, strict protection requirements must be put forward, and accordingly, a higher protection level must be assigned.
In actual classification, there are two protection levels: I level protection and Ⅱ level protection. I Level protection targets structures and buildings that, if damaged by rock and soil movement, would lead to production halts or potentially cause major casualties and significant losses. Hoisting shafts, headframes, and hoisting machine rooms are core facilities for mine production; their safety directly determines whether the mine can operate normally. If these facilities are damaged by rock and soil movement, ore cannot be hoisted normally, and the entire mine production will be paralyzed, potentially triggering serious safety accidents and endangering personnel. Power plants, central substations, central repair shops, central compressor stations, and main fan rooms provide key support for mine production, including electricity, equipment maintenance, compressed air, and ventilation. Their normal operation is the basic guarantee for mine production. Damage would severely affect mine production and may even trigger a series of secondary disasters. Stations, railway main line embankments, and cableway loading stations are important components of the mine transportation system, playing a key role in the transportation of ore and materials. Damage would lead to transportation interruptions, affecting the mine's economic benefits. Reservoirs, water towers, chimneys, permanent multi-story public buildings, and residential buildings are related to the lives of mine personnel and the operation of basic facilities. Damage would significantly impact the lives of personnel and the normal order of the mine. Therefore, these buildings and structures are included in I level protection scope.
Ⅱ Level protection covers all buildings and structures except those under I level protection. Shafts without hoisting equipment, such as ventilation shafts and filling shafts, although less important than hoisting shafts, are also indispensable parts of mine production. They play an important role in ventilation and filling, and therefore require a certain degree of protection. Other secondary shafts and some auxiliary buildings and structures, such as small warehouses and ordinary production workshops, have a relatively small impact on mine production, but their protection from serious damage by rock and soil movement is still necessary to maintain the basic order of mine production, so they are classified as Ⅱ level protection.
Location Selection Principles
(1) Safety Principle
The safety principle occupies a core position in the selection of shaft locations perpendicular to the ore body's strike, serving as the primary guideline for ensuring the safe and stable operation of mine production activities. From a geomechanical perspective, after underground ore body mining, the original stress equilibrium state of the surrounding rock mass is disrupted, triggering a series of complex mechanical responses. As the goaf expands, the overlying strata, under the action of self-weight and tectonic stress, will gradually undergo deformation, displacement, and failure. This failure propagates upwards to the surface, forming a surface movement zone. Within the surface movement zone, the ground will exhibit various complex deformation phenomena, such as subsidence, cracks, and tilting. These deformations not only cause direct physical damage to ground buildings and structures but also alter the engineering properties of the underground soil and rock mass, increasing the risk of geological disasters. If the shaft is located within the surface movement zone, during mining, the shaft will be subjected to uneven pressure and deformation from the surrounding soil and rock mass. This uneven action may cause excessive stress on the shaft walls, leading to cracking, deformation, and other damage. Once the shaft is damaged, its function as a passage for personnel, equipment, and materials will be severely affected, or even completely lost. This will not only hinder normal mining operations, leading to production interruptions, but also pose a significant threat to the lives of underground personnel, increasing rescue difficulty and risk.
To effectively mitigate these risks, shafts and surrounding structures and buildings must be located outside the surface movement boundary. The establishment of a protection zone is one of the important measures to ensure safety, providing a safe buffer zone for shafts and ground facilities. The determination of the safety distance is closely related to the protection level, with different protection levels having different safety distance requirements. I Buildings and structures under level protection, due to their extremely high importance to mine production and safety, require a larger safety distance to ensure their safety if damaged, resulting in serious consequences. Hoisting shafts, headframes, and hoisting machine rooms are key facilities for mine production, directly related to ore hoisting and transportation. Problems would paralyze the entire mine's production and potentially trigger serious safety accidents. Therefore, their safety distance from the surface movement boundary is set at 20 meters. This is derived from extensive engineering practice and scientific research, effectively resisting the influence of surface movement and ensuring the safe and stable operation of these facilities. For special geographical environments such as rivers and lakes, considering their sensitivity to surface movement and the potential for serious disasters such as floods and dam breaks if damaged, the safety distance is increased to 50 meters to minimize risks. Ⅱ Buildings and structures under level protection, although relatively less important, cannot be ignored. Shafts without hoisting equipment, such as ventilation shafts and filling shafts, play an important role in mine ventilation and filling, and are necessary components for ensuring normal mine production. To ensure that these shafts are not seriously damaged by surface movement, their safety distance from the surface movement boundary is set at 10 meters. This distance setting considers the importance of these shafts while balancing economic and practical feasibility, meeting certain safety requirements while reasonably controlling engineering costs.
(2) Economic Reasonableness Principle
The principle of economic reasonableness is another key factor to be considered in the selection of shaft locations perpendicular to the ore body's strike. It runs through the entire life cycle of mine construction and production, directly relating to the economic benefits and sustainable development capabilities of mining enterprises. From the initial infrastructure investment in mine construction to the control of production costs during operation and the efficiency of resource recovery and utilization, the principle of economic reasonableness plays a vital role.
In terms of infrastructure investment, the closer the shaft location is to the ore body, the shorter the length of the stope. The stope is a horizontal roadway connecting the shaft and the ore body, and its length directly affects the overall engineering volume and cost of the shaft and roadway engineering. Taking a large metal mine as an example, in the early shaft site planning, due to the failure to fully consider the proximity to the ore body, the stope length was excessively long. This not only increased the amount of rock excavation during excavation but also required more support materials and equipment to ensure the stability of the stope. According to statistics, the infrastructure investment increased by tens of millions of yuan due to the excessively long stope. In subsequent expansion and renovation projects, by re-optimizing the shaft location to be closer to the ore body, the stope length was significantly shortened. 30% The new shaft location reduced rock excavation by approximately and support costs by 20% The above measures effectively saved infrastructure funds. From the perspective of long-term operating costs, the shortened length of the haulage ways resulted in a significant reduction in transportation costs. In the mining process, ore needs to be transported through the haulage ways to the shaft and then hoisted to the surface. Increasing the length of the haulage ways will lead to longer transportation distances, and the energy consumption of transportation equipment will increase accordingly. At the same time, longer transportation distances also mean that more transportation equipment and manpower are needed to ensure timely ore transportation. This not only increases energy consumption costs but also increases equipment maintenance and labor costs. Conversely, the shaft location closer to the ore body shortens the transportation distance, improves the operating efficiency of transportation equipment, and reduces energy consumption. According to calculations, after shortening the transportation distance, the mine's annual transportation costs have been reduced by millions of yuan. The improvement in transportation efficiency also allows ore to be transported from underground to the surface faster, reducing the ore's residence time underground and improving the overall production efficiency of the mine. This means that in the same amount of time, the mine can mine and transport more ore, increasing output and further improving economic efficiency.
A reasonable shaft location can also improve resource recovery efficiency. When the shaft is close to the ore body, mining operations can more easily carry out comprehensive mining of the ore body, reducing ore losses due to inconvenient mining. In some complex ore body mining, if the shaft location is improper, some ore bodies may be difficult to mine, resulting in resource waste. A reasonable shaft location allows mining equipment to be closer to the ore body, facilitating the use of advanced mining technologies and processes to improve ore recovery rates. This not only increases the mine's resource reserves and extends the mine's service life but also reduces economic losses due to resource waste, laying a solid foundation for the sustainable development of mining enterprises in the long run.
Selected Methods and Steps
(1) Delineating the Surface Movement Zone
Delineating the surface movement zone is the crucial first step in determining the vertical ore body strike position of the shaft; its accuracy directly affects the safety and rationality of subsequent shaft location selection. This process mainly relies on the abundant geological information provided by geological cross-sections and longitudinal sections.
Geological cross-sections clearly show the ore body's vertical occurrence, including its thickness, dip angle, and contact relationship with surrounding strata. Through detailed analysis of this information, the impact range and extent of underground mining activities on different strata can be preliminarily determined. When the ore body dip is steep, the mining impact may extend upward along the ore body dip over a large range; the thicker the ore body, the greater the support impact on the overlying strata after the goaf is formed, leading to a wider range of surface movement. The cross-section also reflects the distribution of geological structures such as faults and folds. Faults destroy the integrity of the rock mass, making it easier for mining impacts to propagate along the fault direction, thus expanding the range of the surface movement zone; fold structures change the stress state of the strata, and during mining, strata in folded areas are more prone to deformation and destruction, requiring special attention when delineating the surface movement zone.
Geological longitudinal sections focus on showing the horizontal changes of the ore body and its relative position to the surface. Through longitudinal sections, the strike length and burial depth changes of the ore body can be understood. For ore bodies with long strike lengths, the superimposed impact of mining in different sections on surface movement needs to be considered; changes in burial depth will affect the extent to which mining impacts are transmitted to the surface, and mining of shallower ore bodies is more likely to cause significant surface movement. Longitudinal sections can also help determine the undulation of the surface topography. In areas with significant topographic undulation, surface deformation is more likely to be uneven under mining impacts, increasing the complexity of delineating the surface movement zone.
In the actual delineation process, relevant mining experience formulas and engineering analogy data are usually used, combined with the information provided by geological sections, to determine the boundary of the surface movement zone. For a specific mine, based on its mining method and ore properties, reference is made to surface movement observation data from similar mines to determine the corresponding movement angle parameters. Then, with the boundary of the ore body as the basis, according to the size of the movement angle, the boundary line of the surface movement zone is drawn upward and outward on the geological section. Through a comprehensive analysis of multiple geological cross-sections and longitudinal sections, the boundaries of the surface movement zones determined by different sections are integrated to accurately delineate the entire mining area's surface movement zone.
(2) Determining the Safe Distance and Location
After delineating the surface movement zone, the safe distance needs to be determined based on the protection level, and then, combined with the ore body location and topography, the shaft location is accurately selected. This process comprehensively considers multiple factors and weighs the pros and cons, which is crucial for ensuring the safety and economic rationality of mining production.
The protection level is an important basis for determining the safe distance; buildings and structures with different protection levels correspond to different safe distance requirements. For I level protected buildings and structures, such as hoisting shafts, derricks, hoisting machine rooms, power plants, and central substations, because they have a core position in mining production, once damaged, production will stop, and may even cause serious casualties and major economic losses, so a larger safety distance needs to be set. According to relevant standards and regulations, their safety distance from the surface movement boundary is usually 20 meters. This is because the importance of these facilities determines that sufficient safety buffer space must be provided to minimize the risk of damage caused by surface movement. For special geographical environments such as rivers and lakes, considering the serious disasters such as floods and dam breaks that may be caused by surface movement damage, the safety distance is further increased to 50 meters, reflecting the high importance and strict protection of these key areas.
Ⅱ level protected buildings and structures, such as shafts without hoisting equipment (ventilation shafts, filling shafts, etc.) and other secondary facilities, although their importance is relatively low, are also indispensable parts of mining production. To ensure that these facilities are not seriously damaged by surface movement to a certain extent, the safety distance from the surface movement boundary is set to 10 meters. This distance meets certain safety requirements while considering economic costs and the feasibility of actual operations, reasonably controlling engineering investment while ensuring the basic production order of the mine.
After determining the safe distance, the ore body location and topographic factors need to be considered comprehensively to select the shaft location. From the perspective of the ore body location, the shaft should be as close as possible to the ore body to shorten the length of the haulage ways and reduce transportation costs. As mentioned in the previous text, through calculation, it was found that the correct positions of the main and auxiliary shafts of Houzhuang Iron Mine should be moved vertically toward the ore body strike direction by 137m,这样 5 stages, the length of the haulage ways can be reduced by 685m。按每立方米掘进成本 153 Meta-calculation can save a significant amount of investment, while also reducing the underground transportation cost per ton of ore, decreasing the walking distance for underground workers, and bringing long-term economic benefits. However, while being close to the ore body, it is also necessary to ensure that the shaft is at a safe distance to avoid threats from surface movement.
Topographic factors are also not to be ignored. Areas with flat and open terrain are conducive to shaft construction and the arrangement of ground facilities, reducing construction difficulty and cost. Under such topographic conditions, the transportation of construction equipment and materials is more convenient, and the foundation treatment of ground buildings is relatively simple. However, areas with complex and undulating terrain may increase the difficulty and cost of shaft construction, such as requiring a large amount of earthwork to level the site, and will also place higher demands on the stability of ground facilities. When selecting shaft locations in mountainous areas, the stability of the mountain body must be considered, avoiding the construction of shafts in areas prone to geological disasters such as landslides and debris flows. The impact of topography on ventilation and drainage systems must also be considered to ensure the normal operation of various production systems in the mine.
Case Analysis
Taking Houzhuang Iron Mine as an example, there are some typical problems in the selection of shaft location, which fully highlight the importance of the rationality of the shaft's vertical ore body strike position selection. Houzhuang Iron Mine is located in Jinling City, Shandong Province, 1979 Year, the geological and hydrological report was submitted by the geological survey team, 1983 Year, the design was carried out by Shandong Metallurgical Design Institute, 1985 Year, the infrastructure construction began, 1992 Year, it was basically completed and put into production. The mineable reserves within the design scope are 1467.2 ten thousand t ,annual ore production 50 ten thousand t ,service life 29 years, investment 5000 ten thousand yuan.
Through years of production practice, it has been found that the location of the main and auxiliary shafts is unreasonable. According to relevant regulations, after calculating the moving zone and collapse zone, it is known that the correct position of the main and auxiliary shafts should be moved vertically towards the ore body strike direction from the existing position 137m (This is based on the calculation of unfilled goaf. If the calculation is based on the filling mining method used in the design, the position of the main and auxiliary shafts can be moved further towards the ore body). The current location has led to a series of negative consequences. From the perspective of infrastructure construction cost, due to the improper location of the shaft, 5 stages of horizontal ( -100m、-160m、-220m、-280m、-340m ) the length of the stope increased, a total of more than 685m。按每立方米掘进成本 153 meters of stope length were excavated. Based on a cost of 122.62 ten thousand yuan, the additional investment is
This undoubtedly increased the initial construction investment of the mine and occupied a large amount of capital resources. In terms of operating costs, the increased stope length has significantly increased the underground transportation cost per ton of ore. The longer transportation distance means that more energy needs to be consumed to drive transportation equipment, such as the power consumption of electric locomotives and the wear and tear of mine cars, which will increase accordingly, resulting in a significant increase in the transportation cost per ton of ore. Moreover, underground workers need to walk longer distances to complete production operations, which not only reduces work efficiency but also increases the labor intensity of workers. In the long run, this has an adverse impact on the economic benefits of the mine.
Summary
The selection of the shaft's vertical ore body strike position is a systematic and complex engineering project, covering multiple key links from conceptual understanding to practical operation. The concepts of the surface moving zone and protection zone are the basis for understanding the entire site selection process. The formation mechanism of the surface moving zone and the important role of the protection zone are closely related to the safety of the shaft location. The division of protection levels provides a clear basis for determining the safety distance. Different protection levels correspond to different safety distance requirements, which is an important principle for ensuring the safety of mine production.
In terms of location selection principles, the safety principle is always the primary consideration. The shaft and surrounding structures and buildings must be away from the surface moving zone to avoid damage from surface movement. The setting of the protection zone and the strict implementation of the safety distance are to ensure the safe and stable operation of mine production. The principle of economic rationality is equally important, and it runs through the entire process of mine construction and production. The shaft location close to the ore body can effectively reduce the length of the stope, reduce transportation costs, improve resource recovery efficiency, and thus bring significant economic benefits to mining enterprises.
Selection methods and steps are specific means to achieve scientific site selection. By delineating the surface moving zone through geological cross-sections and longitudinal sections, the scope and boundary of surface movement can be accurately grasped. According to the protection level, the safety distance is determined, and the shaft location is selected in combination with the ore body location and topographic factors. This process requires comprehensive consideration of multiple factors, weighing the pros and cons to achieve the optimal site selection effect. The case of Houzhuang Iron Mine fully demonstrates the serious consequences of unreasonable selection of the shaft's vertical ore body strike position. From the increase in infrastructure construction costs to the increase in operating costs, it has had an adverse impact on the economic benefits of the mine, which further highlights the importance of scientific site selection.
Note: Part of the content of this article refers to MOOC Northeastern University Underground Mining of Metal Deposits Xu Shuai, An Long's courseware
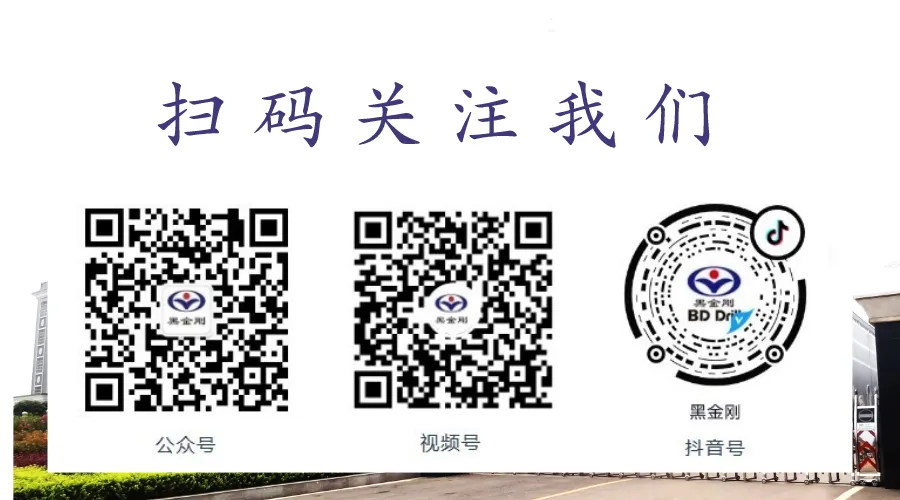