
Detailed Explanation of Security Mine Pillars - Black King Kong Report
Preface
In mining operations, safety pillars are a crucial concept. They refer to the sufficient pillars left behind to protect shafts, structures, and buildings when, due to specific limitations, they must be located within the surface subsidence zone. Safety pillars bear the significant responsibility of protecting surface buildings, shafts, and other important facilities. Their existence is of great importance. They effectively prevent surface subsidence and deformation caused by underground mining, thus avoiding threats to the surrounding environment and personnel safety, laying a solid foundation for the safe and stable production of the mine.
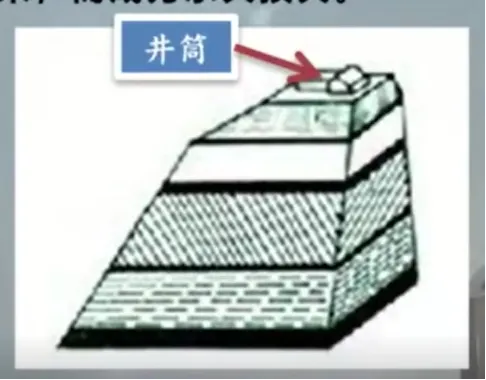
(Image from MOOC, Northeastern University Underground Mining of Metal Deposits, Xu Shuai, An Long )
Urgent Need to Define Safety Pillars
In actual mining operations, a series of special geological conditions and complex engineering backgrounds are often encountered, making the definition of safety pillars an extremely urgent task. When shafts are inevitably located within the surface subsidence zone, they face the risk of tilting, deformation, or even collapse under the influence of underground mining activities. As crucial passages in mining operations, shafts are responsible for transporting personnel, ore, equipment, and materials. If problems occur, the entire mine's production will be halted, posing a serious threat to personnel safety. If important facilities such as rivers or railways pass over or along the edge of the ore deposit, surface movement and deformation caused by ore deposit mining may lead to river diversions, railway track distortions, etc., which will not only damage the surrounding ecological environment but also affect the safety and normal operation of transportation, resulting in immeasurable economic losses and social impacts. Therefore, to ensure the safety of these important facilities and the smooth progress of mining operations, defining safety pillars is particularly necessary, playing an irreplaceable role in maintaining the safety and stability of mine production.
Delineation Process
Clarify Safety Distance, Define Protection Range
When defining safety pillars, the primary task is to determine the safety distance based on the importance of the protected object and relevant standards. The determination of this safety distance is crucial; it directly relates to the safety of the protected object during the mining process. For important buildings such as residential buildings and hospitals, due to their high population density, if affected by mining, serious casualties and property losses may occur, so a larger safety distance needs to be set; for relatively less important ancillary facilities, the safety distance requirements are relatively lower. After determining the safety distance, the protection area should be drawn around the protected object on the geological plan. This process requires precise measurement and drawing to ensure the accuracy of the protection area, laying a solid foundation for subsequent work.
Draw Key Cross-sections, Analyze Geological Details
To gain an in-depth understanding of the ore body and the specific conditions of each stratum, it is necessary to draw cross-sectional geological maps perpendicular to the ore body strike and longitudinal geological maps parallel to the ore body strike. The cross-sectional geological map clearly shows the shape, thickness, and relationship with surrounding strata of the ore body in the vertical direction; the longitudinal geological map shows the extension and geological structure of the ore body in the horizontal direction. During the drawing process, the thickness, dip angle, and geological structure of the ore body and each stratum should be accurately marked. Through the analysis of this information, the geological conditions can be better understood, providing detailed data support for determining the boundaries of the safety pillars. For example, the dip angle of the ore body will affect the direction and range of rock movement, thus having an important impact on the delineation of safety pillars.
Determine Boundary Range Based on Movement Angle
On the cross-section and longitudinal section, draw the movement boundary line downward according to the movement angle of the ore body and each stratum. The movement angle refers to the angle at which the rock moves due to mining activities. It is a key parameter for determining the boundary of the safety pillar. Different rock types and geological conditions will lead to differences in the movement angle, so it needs to be accurately determined according to the actual situation. By drawing the movement boundary line, the intersection points of the movement line with the top and bottom of the ore body can be obtained. These intersection points determine the key positions of the safety pillar boundary line. Connecting these intersection points can preliminarily determine the boundary range of the safety pillar in the strike and dip directions.
Precise Positioning, Delineating Pillar Range
Combining the boundary lines in the strike and dip directions, the safety pillar range of the top and bottom of the ore body can be accurately determined. In this process, various factors need to be considered comprehensively to ensure that the range of the safety pillar meets the protection requirements while minimizing the loss of ore resources. If the shaft is located in the ore body, in addition to leaving the safety pillar near the shaft, it is also necessary to leave the safety pillar for the road or railway leading to the shaft. This is because roads and railways play an important role in mine transportation and need to ensure their safety and stability during mining. When delineating these special safety pillars, the relationship with surrounding facilities should be fully considered, and reasonable planning and design should be carried out to ensure the safe and efficient operation of the entire mining system.
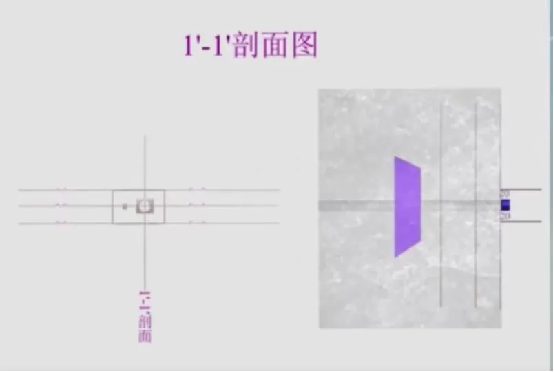
Influencing Factors “ Behind-the-Scenes Players ”
The delineation of safety pillars is not a simple process but is affected by a variety of factors, which are like behind-the-scenes “ manipulators ” , determining the scientific and rationality of the safety pillar delineation.
The importance of the protected object is the primary consideration. For those protected objects related to public safety, social stability, and important infrastructure, such as large residential areas, important transportation hubs (railways, expressways, etc.), and lifeline projects (water, electricity, and gas supply facilities, etc.), high attention must be paid. Once these facilities are damaged, serious social problems and economic losses will be caused. Therefore, when delineating safety pillars, a more sufficient protection range should be left for them to minimize the potential impact of mining activities. Conversely, for some secondary and temporary facilities, the requirements for safety distance and protection range are relatively lower.
Rock properties also affect the delineation of safety pillars. Different types of rocks have significant differences in mechanical properties, which directly relates to the stability of the rocks during mining. For example, hard rocks, such as granite and quartzite, have strong compressive and shear strengths and are not easily deformed or damaged during mining, and their angle of movement is relatively large. This means that when delineating safety pillars, the size of the pillars can be appropriately reduced, thereby reducing the loss of ore resources. However, weak rocks, such as shale and mudstone, have low strength and are easily deformed and collapsed under mining disturbances, with a smaller angle of movement. To ensure the safety of protected objects under such rock conditions, it is necessary to increase the size of the safety pillars to provide sufficient support and protection. The development of rock joints and fissures should not be ignored. Joints and fissures weaken the integrity and strength of the rock, increasing the possibility of rock movement and damage. In areas with dense joints and fissures, safety pillars need to be delineated more cautiously, and it may be necessary to expand the pillar range or adopt special support measures to prevent rock instability.
The occurrence of ore bodies is one of the key factors affecting the delineation of safety pillars. Parameters such as the dip angle, thickness, and shape of the ore body will affect the rock movement and deformation during mining. When the dip angle of the ore body is small, the rock movement caused by mining is mainly concentrated above the ore body, and the delineation of safety pillars is relatively simple; while when the dip angle of the ore body is large, the range of rock movement will extend in the direction of the dip of the ore body, which requires increasing the size of the safety pillars in the dip direction to ensure the safety of the protected objects. The thicker the ore body, the greater the disturbance to the surrounding rocks during mining, and correspondingly, the size of the safety pillars also needs to be increased. In addition, the complexity of the ore body shape will also affect the delineation of safety pillars. For ore bodies with regular shapes, the delineation work is relatively easy; while for ore bodies with irregular shapes, branches, and pinching out, more detailed analysis and research are needed to accurately determine the boundaries of the safety pillars.
Mining plans and the delineation of safety pillars are also closely related. Different mining methods, such as open-pit mining and underground mining (room and pillar method, filling method, caving method, etc.), have different ways of rock damage and movement, which will inevitably affect the delineation of safety pillars. For example, when using the caving method for mining, because it will cause large-scale rock collapse and movement, larger safety pillars are needed to protect surface facilities; while when using the filling method for mining, it can effectively control rock movement, and the size of the safety pillars can be relatively reduced. The mining sequence will also affect the delineation of safety pillars. A reasonable mining sequence can reduce mutual interference during mining and reduce the risk of damage to safety pillars. In some cases, it may be necessary to mine areas far from the protected objects first and then deal with the ore body near the safety pillars to ensure the stability of the safety pillars during mining.
Case Analysis: The Collision of Theory and Practice
Xinda Gold Mine Shaft Safety Pillar Delineation
In the development process of Xinda Gold Mine, serious problems were encountered after entering the deep mining stage. The original design used 65° rock movement angle to delineate the shaft safety pillars. With the increase in mining depth, the limitations of this traditional method have become increasingly prominent. A large amount of high-quality ore body was delineated within the safety pillars and could not be mined, resulting in a huge waste of resources. In order to break this deadlock, relevant personnel started from the key issue of controlling the range of rock movement and introduced the critical loose body pillar theory. The core of this theory is to control the movement range of the overlying strata through specific methods, thus providing a new idea for re-delineating the shaft safety pillars. According to this theory, technical personnel re-delineated the shaft safety pillars. In the actual operation process, various factors such as the geological conditions of the mine, the occurrence state of the ore body, and the mining technology were fully considered. Subsequently, using FLAC 3D numerical simulation software, the impact of mining the optimized ore body on the stability of the shaft was simulated and analyzed. The simulation results were satisfactory. The shaft deformation was mainly concentrated in the vertical settlement, and the horizontal displacement was small, indicating that the shaft bears relatively large pressure in the vertical direction, but the overall stability is still within the controllable range; the stress disturbance range after ore excavation did not affect the vicinity of the shaft, indicating that the shaft is in a relatively stable state, and the new safety pillar delineation scheme effectively guarantees the safety of the shaft. Through this practice, Xinda Gold Mine successfully solved the problem of excessive delineation of traditional safety pillars, created favorable conditions for the mining of deep ore bodies, improved resource recovery rate, reduced mining costs, and achieved significant economic and social benefits.
Based on 3dmine Software for Open-pit to Underground Safety Pillar Delineation
Against the backdrop of the continuous development of modern mining technology, 3dmine software-based open-pit to underground safety pillar delineation methods have emerged, providing more scientific and accurate solutions for mining.
Determining the safe subsidence zone is the first step. For different protected objects, technical personnel need to carefully review the relevant standards and specifications to determine the accurate location and length of the safe subsidence zone. The determination of the safe subsidence zone is crucial, as it directly relates to the accuracy and reliability of the subsequent safety pillar delineation. The safe subsidence zone is an arc-shaped curve formed according to the outer contour of the protected object, and its length is usually no less than 5 times the distance between the safe subsidence zone and the protected object, to ensure that the protected object is within the safe range even under the most unfavorable conditions.
Fitting the safe subsidence zone with the surface including the open-pit dtm is a key step. This step requires as many points on the subsidence zone as possible to fall on the surface dtm at least 90 % of the points must achieve accurate fitting. Through this fitting operation, the safe subsidence zone can be made to fit the actual terrain of the surface more closely, providing more accurate basic data for subsequent analysis and calculation. In the fitting process, professional algorithms and technical means need to be used to process and analyze a large amount of data to ensure the accuracy and effectiveness of the fitting.
Extract the fitting curve and extend it downwards according to the rock movement angle θ to a height of 2h , obtaining the derived curve, where h For segmented height. This process requires precise calculation and rigorous operation to ensure the accuracy of the derived curve. Rock movement angle θ Determination requires consideration of various factors, such as the mechanical properties of the rock and geological structures. Through a comprehensive analysis of these factors, a reasonable rock movement angle is determined, ensuring that the derived curve accurately reflects the movement trend of the rock during the mining process.
in 3dmine Software, based on the derived curve and the fitting curve, quickly generates dtm surface, and it is numbered as m , m The initial value is 1。 3dmine Software has powerful data processing and modeling capabilities, enabling the quick and accurate generation of dtm surface. The generated dtm surface provides an intuitive and clear model for subsequent analysis and calculation, facilitating further operations by technicians.
Based on elevation ' h0-mh ' cutting dtm surface forms h0-mh horizontal profile line, h0 is the average elevation of the ground surface. By cutting the dtm surface, horizontal profile lines of different elevations can be obtained. These profile lines can show the shape and range of the safety pillar at different depths. By analyzing these profile lines, more information about the safety pillar can be obtained, providing detailed data support for subsequent work.
Determine whether the profile line penetrates 'm' No. dtm surface is an important judgment step. If it has penetrated, the profile line and the overflow boundary are combined to form a new fitting curve, let m = m+1 , and return to step 4 , in step 5 , the new fitting curve and the derived curve of the new fitting curve together form dtm surface, other steps are performed sequentially; if the profile line does not penetrate dtm surface, then proceed to the next step. This process requires continuous judgment and adjustment to ensure that the final safety pillar boundary is accurate and reasonable. In actual operation, technicians need to have rich experience and keen judgment, and flexibly adjust the operation steps according to the specific situation.
By deleting redundant points and T-junctions ' h0-mh ' The horizontal profile line is trimmed, and the theoretical boundary of the safety pillar at each level is derived using the trimmed plane curve. This step can make the boundary of the safety pillar more precise and reasonable, avoiding unnecessary errors and deviations. During the trimming process, professional graphic processing technology needs to be used to carefully process the horizontal profile line to ensure the accuracy of the boundary.
Based on the actual engineering layout, the long-term mining plan, and the principles of simplicity and ease of construction, the theoretical boundary of the safety pillar is optimized to obtain a more reasonable safety pillar boundary. The actual engineering layout includes development projects and preparation projects, and the long-term mining plan considers the long-term development goals of the mine. By comprehensively considering these factors, the delineation of the safety pillar can better meet the needs of actual production, improving the efficiency and safety of mine mining. During the optimization process, close communication and cooperation with relevant departments are required, fully listening to the opinions of all parties to ensure that the final safety pillar boundary meets both safety requirements and is convenient for construction and production.
This method of delineating open-pit to underground safety pillars based on 3dmine software closely integrates software technology, theoretical analysis, and actual engineering. Compared with the traditional method of directly deriving the safety pillar boundary based on the rock movement angle, it has obvious advantages. The safety pillar boundary obtained is smoother and simpler, making it easier for construction personnel to carry out retention construction, and it is also conducive to improving the resource recovery rate of the safety pillar, providing strong support for the sustainable development of the mine.
Summary
The delineation of safety pillars is a complex and systematic project that has a profound impact on the safety, resource recovery rate, and economic benefits of mine mining. From the perspective of the necessity of delineation, it is a key measure to protect important surface facilities, maintain the ecological environment, and ensure the sustainable mining of mines. In the delineation process, from clarifying the safety distance and protection range, to drawing geological cross-sections to analyze geological conditions, and then determining the boundary based on the movement angle and accurately delineating the range of the pillars, each step is closely linked, and any mistake in any link may lead to unreasonable delineation of safety pillars, thus causing safety hazards or resource waste. Many factors affect the delineation of safety pillars. The importance of the protected object determines the level of safety protection, the rock characteristics and orebody occurrence are the geological basis, and the mining plan affects the delineation scheme from the perspective of engineering implementation. These factors are intertwined, requiring comprehensive and integrated consideration during the delineation process.
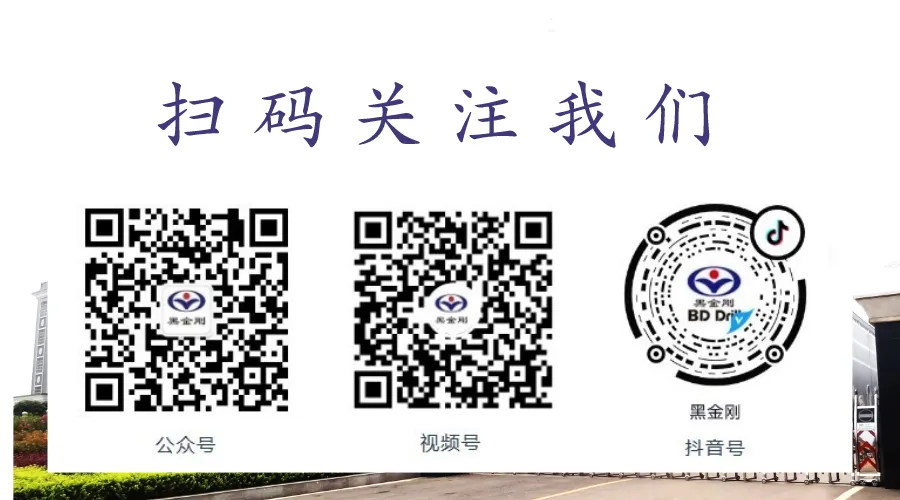