
Upper and lower plate along the vein roadway with additional vein layout (circular transportation layout) - Black King Kong report
I. Introduction
In mining operations, the layout of stage transportation roadways is like the circulatory system of the human body, playing a vital role in mining efficiency. A reasonable roadway layout ensures efficient and safe transportation of ore, reduces transportation costs, and improves the overall economic benefits of the mine. With the continuous development of mining technology, various stage transportation roadway layouts have emerged. Among them, the layout of upper and lower roadways along the vein plus through-vein, also known as the ring-shaped transportation layout, occupies an important position in specific mining scenarios due to its unique advantages.
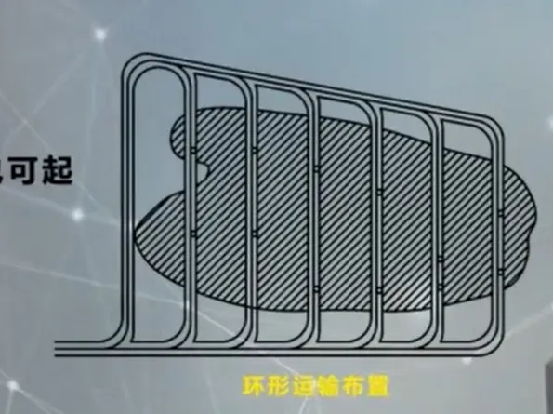
(Image from MOOC Northeastern University Underground Mining of Metal Deposits Xu Shuai, An Long )
II. Composition and Operation of Ring Transportation Layout
(1) Layout Details
The core of the ring transportation layout lies in its unique route layout, mainly consisting of heavy-duty lines, empty lines, and ring lines. The heavy-duty line is responsible for transporting ore-laden vehicles, serving as the key channel for transporting ore from the mining face to the unloading station. Its surface is usually specially treated to withstand the frequent rolling of heavy vehicles, ensuring smooth and safe transportation. The empty line is a dedicated route for empty vehicles returning to the loading point, running parallel to the heavy-duty line, reducing interference between empty and loaded vehicles, and improving transportation efficiency. The ring line is the hub of the entire layout. It not only serves as a loading line, providing space for ore loading, but also cleverly connects the empty line and the heavy-duty line, forming a highly efficient circular transportation system.
From a spatial layout perspective, the heavy-duty line and the empty line are generally arranged along the upper and lower sides of the ore body, basically parallel to the ore body strike. This arrangement facilitates ore loading and unloading and transportation, reducing detours and backtracking of the transportation route. The ring line encircles the heavy-duty line and the empty line, forming a closed ring structure. In actual mining operations, the various lines are interconnected through reasonably set switches and connecting passages to ensure that vehicles can smoothly switch between different lines. For example, at the loading point, the empty line is connected to the ring line via a switch. When an empty vehicle reaches the loading point, it can smoothly enter the ring line for loading operations; after loading, the loaded vehicle can then enter the heavy-duty line from the ring line via another switch and head towards the unloading station. This layout is like a carefully designed transportation network, with each line performing its own function while working closely together to ensure the efficient operation of ore transportation.
By referring to the provided image, we can have a more intuitive understanding of this layout. The image clearly shows the positional relationship between the heavy-duty line, the empty line, and the ring line, as well as their connection to the loading point and the unloading station. The heavy-duty line and the empty line are arranged in parallel straight lines, while the ring line encircles them, forming a nearly circular transportation channel. At the loading point, the empty vehicle enters the ring line from the empty line, and after loading, the loaded vehicle enters the heavy-duty line from the ring line. The entire process is clear at a glance. This layout not only improves transportation efficiency but also increases the flexibility and reliability of the transportation system, allowing ore to be transported from the mining face to the unloading station in the shortest time.
(2) Operational Process
The operation process of the ring transportation layout is rigorous and efficient, operating smoothly like a precise clock. Once the ore is mined at the mining face, the transportation process officially begins. First, the empty vehicle departing from the unloading station slowly drives towards the loading point along the empty line. During the journey, the driver must strictly abide by the transportation rules, maintaining a stable speed and safe distance to ensure that the empty vehicle can reach the loading point smoothly. In this process, the road conditions and signaling system of the empty line are crucial. Good road conditions can reduce vehicle wear and tear and malfunctions, while an accurate signaling system can guide the empty vehicle correctly, avoiding collisions and congestion.
Upon reaching the loading point, the empty vehicle enters the ring line. The ring line, serving as the loading line, is equipped with advanced loading equipment, such as loaders and belt conveyors. This equipment can quickly and efficiently load the ore from the mining face into the empty vehicle. During the loading process, the operators need to skillfully master the operation techniques of the loading equipment to ensure that the ore is evenly loaded into the vehicle, avoiding overloading or uneven loading. At the same time, strict monitoring of the loading process is necessary to ensure loading quality and safety. For example, cameras and sensors installed at the loading point monitor the loading situation in real-time. If any abnormality is detected, measures can be taken promptly to address it.
After loading is complete, the loaded vehicle enters the heavy-duty line from the ring line and begins its journey back to the unloading station. During the journey, due to the large amount of ore loaded, the vehicle's weight and inertia increase, so the driver needs to drive more cautiously. The heavy-duty line usually has special facilities, such as speed bumps and safety lanes, to deal with potential emergencies. When approaching the unloading station, the loaded vehicle needs to slowly enter the unloading area according to signal instructions. The unloading station is equipped with professional ore unloading equipment, such as tipplers and scraper conveyors, which can quickly and safely unload the ore from the vehicle. After the ore is unloaded, it undergoes further processing and treatment, eventually becoming usable resources. The empty vehicle, after unloading at the unloading station, re-enters the empty line to begin the next round of transportation cycle.
III. Advantages of Ring Transportation Layout
(1) Strong Production Capacity
In the large-scale mining of thick and extra-thick ore bodies, the ring transportation layout acts like a tireless and efficient transportation master, fully demonstrating its strong production capacity. This layout, through its unique route design, achieves efficient circular transportation of empty and loaded vehicles, greatly reducing waiting time and congestion during transportation. In the mining operation of a large mine, the mine uses a ring transportation layout to mine extra-thick ore bodies, with a throughput capacity of 150 - 300 ten thousand tons per year. The advanced loading equipment and efficient transportation lines work together closely, allowing ore to be continuously transported from the mining face to the unloading station. Multiple loading and unloading operations can be completed per hour. Compared to other transportation layouts, the transportation efficiency is increased several times. During peak periods, it can even achieve the feat of transporting thousands of tons of ore per hour. This strong production capacity provides a solid guarantee for the efficient mining of large-scale ore bodies, allowing the mine to mine a large amount of ore in a short period, meeting the market demand for mineral resources.
(2) Safe and Convenient Loading Experience
The characteristic feature of the through-vein loading system in a circular transportation layout is its excellent safety and convenience for loading operations. The through-vein roadways are arranged vertically or near-vertically to the ore body, allowing mine cars to be loaded directly within the through-vein roadways. This loading method avoids potential vehicle collisions and casualties that may occur during loading operations in narrow along-vein roadways. At a certain mine's loading site, operators only need to drive the mine car into the through-vein roadway for convenient loading operations. The through-vein roadway has a relatively spacious area, providing ample operating space for the ore loading equipment, making the loading process smoother. Operators can more flexibly control the ore loading equipment to accurately load the ore into the mine car, improving loading efficiency and quality. Moreover, through-vein loading can also reduce ore spillage and loss during transportation, further improving resource utilization.
(3) It also has mineral exploration functions
During the construction of transportation roadways in a circular transportation layout, it can also cleverly play a role in further exploration of the ore body. When advancing along-vein and through-vein roadways, construction personnel can directly observe the geological conditions of the ore body, such as the thickness, strike, dip, grade, and quality of the ore. This first-hand geological data is of great significance for in-depth understanding of the occurrence and variation patterns of the ore body. During the mining process at a certain mine, through the roadway construction of a circular transportation layout, a previously undiscovered branch of the ore body was discovered. Through further exploration and research of this branch ore body, it was determined to have high mining value. This not only increased the mine's resource reserves but also provided new impetus for the mine's sustainable development. The circular transportation layout can also provide a scientific basis for the selection and optimization of mining methods through exploration of ore bodies in different areas, making mining operations more reasonable and efficient.
4. Limitations of Circular Transportation Layout
Although the circular transportation layout shows many significant advantages in mining operations, its large excavation workload also brings a series of limitations that cannot be ignored. First, from the perspective of time cost, large-scale excavation projects require a lot of time. In a mining project at a certain mine, in order to build a circular transportation system, excavation work lasted for several years. During this period, the mining progress of the mine was greatly restricted, and the ore could not be mined and transported out in time, leading to delayed market supply and affecting the economic benefits of the enterprise. Long-term excavation work also increased the mine's management costs and operational risks, because various changes in geological conditions and technical problems may be encountered during the excavation process, requiring more manpower, material resources, and financial resources to solve.
Secondly, the large excavation workload directly leads to a significant increase in costs. During the excavation process, a large amount of manpower, equipment, and materials are required. In terms of labor costs, a large number of professional excavation workers need to be hired, and their wage expenses are a considerable expense. Equipment costs are also quite high, such as the purchase, leasing, and maintenance costs of excavation machines, loaders, and transportation vehicles, all requiring substantial capital investment. Material costs are equally important, such as explosives, detonators, steel, cement, and other materials required for excavation, which also account for a large part of the cost. According to statistics, in some mines that use a circular transportation layout, excavation costs account for as much as 30% - 40% Such high costs may be unbearable for some small mines or enterprises with tight funds, and may even affect the sustainable development of the mine.
In addition, the large excavation workload will also have a certain impact on the environment. A large amount of rock excavation will produce a large amount of waste residue and dust. The treatment of waste residue requires a large amount of land resources, and if not handled properly, it may also pollute the soil and water bodies. Dust emissions will affect air quality and harm the health of workers and surrounding residents. During the excavation process, it may also destroy the underground ecological balance and threaten the survival environment of some rare species.
5. Applicable Scenarios and Case Analysis
(1) Analysis of Applicable Conditions
The circular transportation layout has irreplaceable advantages in the mining of large-scale thick and extra-thick ore bodies. These ore bodies usually have abundant reserves, large mining scales, and extremely high requirements for transportation capacity. The strong production capacity of the circular transportation layout can meet the transportation needs of a large amount of ore under large-scale mining, ensuring that the ore can be transported from the mining area to the unloading station in a timely and efficient manner. In a mining project of an extra-thick ore body, the ore body thickness reaches hundreds of meters. After adopting a circular transportation layout, millions of tons of ore can be successfully transported annually, providing strong support for the efficient mining of the mine.
In several groups of mutually parallel ore bodies, the circular transportation layout can also perform excellently. Because the distance between parallel ore bodies is relatively close, through reasonable planning of the circular transportation system, interconnectivity of transportation lines between various ore bodies can be achieved. This not only reduces the repeated construction of transportation lines and lowers costs but also improves transportation efficiency. Through the connection of the circular line, empty and loaded vehicles can be flexibly allocated, making full use of transportation resources. At a certain mine with three groups of mutually parallel ore bodies, after adopting a circular transportation layout and optimizing the transportation lines, synergistic transportation between various ore bodies was achieved, and transportation efficiency increased by 30% or more.
(2) Actual Case Demonstration
Taking the Wulan Mine of China Railway Resources Xinxin Company as an example, the mine adopts a flat adit + inclined ramp development method, and the design adopts a main and auxiliary double inclined ramp trackless transportation scheme to achieve circular transportation with empty vehicles entering and loaded vehicles exiting. Before the circular transportation system was formed, the Wulan Mine relied solely on a single inclined ramp to maintain the underground ore transportation task, often causing underground traffic congestion and greatly restricting the improvement of transportation efficiency. As the underground development continued to extend, the main and auxiliary double inclined ramps were hardened, but due to insufficient concrete supply during the epidemic, the road surface hardening was delayed, resulting in difficulties in road dredging, poor drainage capacity, and serious damage to local road surfaces, making it easy to collide with roadway walls and pipelines.
In order to solve the transportation “ bottleneck ” problem, 2024 year, Xinxin Company increased the construction efforts of the transportation system. From 2023 year 5 month 10 day, Xinxin Company introduced a crushed stone processing and concrete mixing system from China; 2024 year 7 month, the “ all-weather production, full-series supporting, and full-process link was completed ” The concrete mixing station achieves the advanced level of similar stations in Mongolia, making up for the shortcomings of the Ulaan mine's inability to carry out normal concrete construction in winter. During peak mixing periods, the station provides approximately 100 cubic meters of mixed concrete per day, and is equipped with 4 concrete tank trucks, with a maximum transport distance of 10km , providing strong support for road hardening. 2024 In 2023, Xinxin Company adopted a new method of prefabricated concrete block paving, changing the traditional practice of directly pouring concrete on the road surface, which caused long traffic interruptions, thus minimizing the interference to transportation and accelerating the paving progress.
Currently, Xinxin Company's surface to 765m mid-section double-slope road circulating transportation system is fully formed, 765m The round-trip time for ore transportation from the mid-section to the surface is reduced from 60 minutes to 40 minutes. This not only reduces safety risks, but also gives full play to the efficiency of mechanized construction and automobile transportation, helping to reduce mining costs and laying a solid foundation for the steady development of the mine. The successful case of Ulaan Mine fully demonstrates the significant effect of circular transportation layout in solving transportation problems, improving transportation efficiency and reducing costs.
VI. Summary
The up and down levels along the vein roadway plus the vein layout (circular transportation layout) is an important form of stage transportation roadway in the mining field, occupying a unique position. With its strong production capacity, safe and convenient loading experience, and exploration function, it has become an ideal choice for large-scale thick and extra-thick ore bodies and several groups of parallel ore bodies. Xinxin Company of China Railway Resources successfully solved the transportation problem, improved transportation efficiency, and reduced costs by adopting the circular transportation layout in Ulaan Mine. “ bottleneck ” However, we cannot ignore its limitation of large excavation engineering volume, which not only increases time and economic costs, but also has a certain impact on the environment. In practical application, mining enterprises need to comprehensively consider various factors such as geological conditions, mining scale, and financial conditions, weigh the pros and cons, and cautiously choose whether to adopt the circular transportation layout.
Note: Part of the content of this article refers to MOOC Northeastern University Underground Mining of Metal Deposits Xu Shuai, An Long's courseware
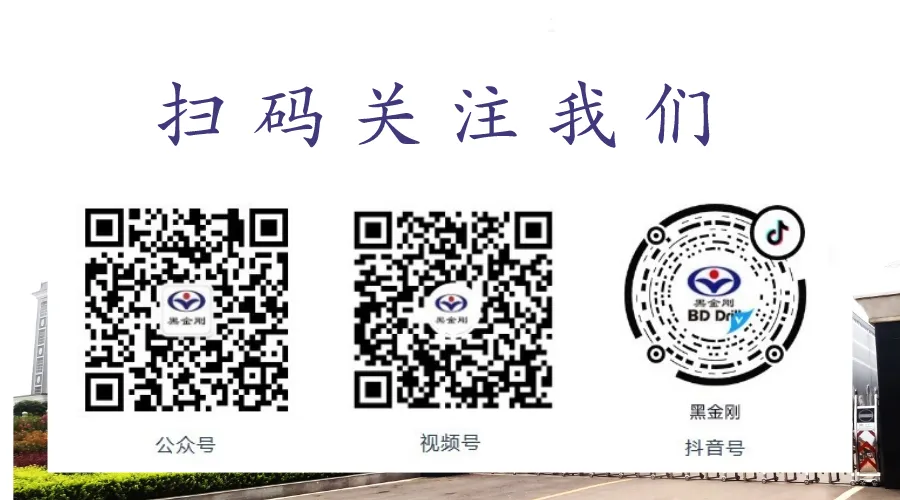