
Comprehensive Exploration of Applications and Choices - Black King Kong Report
Preface
In the field of mine mining, integrated development, as a unique and important development method, is increasingly attracting widespread attention. Integrated development refers to the process of comprehensively developing a coalfield by adopting any two or more development methods such as vertical shafts, inclined shafts, and adits. The essence of this development method is to closely combine the coal seam mining conditions of a specific mine and cleverly combine the advantages of different types of shafts to achieve efficient and safe mine mining.
In actual mine mining operations, a single type of shaft often has certain limitations and cannot fully meet the complex and changeable geological conditions and diversified mining needs. The emergence of integrated development methods effectively compensates for this deficiency. It can fully utilize the unique advantages of various types of shafts, flexibly select the most suitable type of shaft for combination according to different geological conditions and production technology requirements, and thus achieve efficient and safe mine mining.
For example, when encountering situations where the coal seam is buried deep, the topsoil layer is thick, and the hydrogeological conditions are complex, vertical shaft development, although having greater construction difficulty and higher cost, is an important choice due to its large hoisting capacity and strong adaptability to deep mining; while inclined shaft development has advantages such as simple construction, low cost, and high transportation efficiency in cases where the coal seam is shallowly buried, the topsoil layer is thin, and the geological conditions are relatively simple; adit development shows significant characteristics such as low construction difficulty, low cost, and simple ventilation and transportation systems when the terrain conditions are suitable, the coal seam is buried in mountainous areas, and the location is high. Through integrated development, we can organically combine the advantages of these different types of shafts to form the most suitable development plan for a specific mine.
It can be said that integrated development plays a pivotal role in mine mining and is one of the key factors in achieving sustainable development and improving economic efficiency of mines. It can not only improve mine production efficiency and resource recovery rate, reduce production costs and safety risks, but also better adapt to different geological conditions and market demands, laying a solid foundation for the long-term stable development of mines.
Application Examples of Integrated Development
In actual mine mining, the application of integrated development methods is extremely widespread, and various specific development forms have been derived based on different geological conditions and mining needs. The following will analyze several common integrated development methods through specific examples.
(1) Main Inclined Shaft - Auxiliary Vertical Shaft Development
Main Inclined Shaft - Auxiliary vertical shaft development methods have significant advantages in large and extra-large mines, and can fully utilize the advantages of large main and auxiliary hoisting capacities, simple systems, and large ventilation volumes. It is a development method with good technical and economic effects. Many main inclined shafts - Auxiliary vertical shaft development in mines is gradually formed after the expansion of production mines.
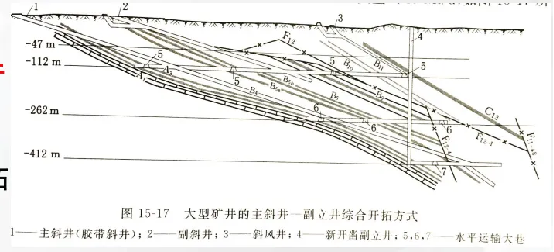
(Picture from MOOC China University of Mining and Technology Mining Engineering Tu Shihao, Fang Zhijun, Zheng Xigui, Wang Xufeng, Peng Hongge, Yuan Yong )
Taking a mine in a certain mining area as an example, the mine was originally developed with an inclined shaft. In the initial stage of mining, inclined shaft development, with its relatively simple construction and low initial investment, met the basic production needs of the mine. However, with the continuous increase in mining depth, the original inclined shaft development method gradually revealed problems in auxiliary hoisting and ventilation. Insufficient auxiliary hoisting capacity could not meet the large amount of equipment and material transportation required for deep mining; the ventilation route was too long, the ventilation resistance increased, resulting in poor ventilation in the mine, seriously affecting production efficiency and safety production.
To solve these problems, the mine built a new auxiliary vertical shaft in the deep part of the coalfield. The construction of the auxiliary vertical shaft effectively improved the auxiliary hoisting capacity, enabling the rapid and efficient transportation of personnel, equipment, and materials to the underground, while shortening the ventilation route, reducing ventilation resistance, and significantly improving underground ventilation conditions. The original inclined shaft continued to be used as the main shaft, equipped with a belt conveyor, giving full play to its high transportation capacity and efficiency, and realizing efficient coal transportation. Through this transformation, the mine successfully transformed into a main inclined shaft - Auxiliary vertical shaft development method not only solved the problems of deep mining, but also significantly improved the mine's production capacity and economic benefits.
For example, in another mining area, it was originally composed of multiple shallowly mined inclined shafts. With the advancement of mining, these inclined shafts gradually faced the needs of resource integration and deep mining. In order to achieve centralized mining and improve production efficiency, the mining area newly excavated or renovated the original inclined shaft shafts, equipped with belt conveyors, making them the main shafts and undertaking the main coal transportation tasks. At the same time, a new auxiliary vertical shaft was opened in the deep part, responsible for auxiliary hoisting and ventilation tasks. Through this method, the mining area successfully transformed from dispersed inclined shaft development to main inclined shaft - Auxiliary vertical shaft integrated development, effectively integrating resources and improving the overall efficiency of the mine.
(2) Main Vertical Shaft - Auxiliary Inclined Shaft Development
Main Vertical Shaft - Auxiliary inclined shaft development is suitable for mines mining coal seams that are not deeply buried, and its formation process has different starting points. In the development of coalfields in shallow parts, in order to reduce the amount of vertical shaft excavation, save mine construction investment, and speed up mine construction, some small mines will excavate a vertical shaft in the middle of the coalfield, mainly responsible for coal hoisting or mixed hoisting tasks. Vertical shafts have the advantages of fast hoisting speed and large hoisting capacity, which can meet the mine's coal hoisting needs. At the same time, an inclined shaft is opened from the coal seam outcrop downwards, undertaking auxiliary hoisting tasks and serving as a safety exit. The construction of inclined shafts is relatively simple, and the excavation speed is fast, which can be put into use in a short time, providing a guarantee for auxiliary transportation and personnel safety in the mine. This development method has a simple system, relatively small infrastructure construction and investment, and a short construction period, which can quickly yield results and is very suitable for small mines in shallow coalfields.
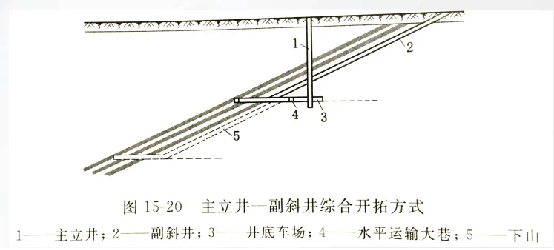
(Picture from MOOC China University of Mining and Technology Mining Engineering Tu Shihao, Fang Zhijun, Zheng Xigui, Wang Xufeng, Peng Hongge, Yuan Yong )
In large mines mining near-horizontal coal seams that are not deeply buried, vertical shaft development is sometimes used first. Vertical shaft development can meet the requirements of large mines for hoisting capacity and ventilation, but with the development of production, in order to further increase the auxiliary hoisting capacity and add mine safety exits, an auxiliary inclined shaft will be built. The addition of the auxiliary inclined shaft significantly enhances the mine's auxiliary hoisting capacity, better meeting the needs of large mines for equipment and material transportation, and also increases the mine's safety exits, improving mine safety. This forms the main vertical shaft - The development method of auxiliary inclined shafts fully utilizes the advantages of vertical shafts and inclined shafts, adapting to the production needs of large mines.
Some small mines originally developed with vertical shafts, after expanding their production capacity, may need to build a new auxiliary inclined shaft because the original hoisting system cannot meet the increased production needs. The construction of the auxiliary inclined shaft can share some of the hoisting tasks, complementing the original vertical shaft to meet the hoisting needs after the mine's production expansion. In this way, small mines can improve their production capacity and economic efficiency without large-scale vertical shaft renovation. 30m ,地质构造为 Ⅲ 类,断层发育,含可采煤层 6 层,煤层倾角在 10 - 20° 。The mine was built through multiple renovations and expansions based on small coal mine excavation. Three vertical shafts were used for development from the first level to the surface, and an inclined shaft was used to connect the second level to the first level. To increase the auxiliary transportation capacity of the second level, an auxiliary inclined shaft was added, forming a main vertical shaft - The development method of the auxiliary inclined shaft effectively solved the problem of auxiliary transportation in deep mining and ensured the continuous production of the mine.
(3) Adit - Inclined Shaft Development
Adit - Adit inclined shaft development has two basic forms: main adit auxiliary inclined shaft and main inclined shaft auxiliary adit, depending on the configuration of the main and auxiliary shafts. In main adit auxiliary inclined shaft development, the main adit generally has most of the functions of the auxiliary shaft, such as auxiliary transportation, ventilation, and personnel passage. Therefore, mines using main adit development can be classified as adit development to a certain extent. However, in some special cases, when the inclined length of the adit uphill section is very large and there are suitable terrain conditions, the adit uphill section will be divided into several levels, and an inclined shaft will be excavated at an appropriate location on the upper level. These inclined shafts mainly undertake the task of removing waste rock from the upper level excavation, removing the waste rock through the inclined shaft and discarding it in the upper mountainous area, and also undertake the task of personnel and material hoisting, playing a role similar to an auxiliary shaft. The coal mined underground is then transported down to the main adit and then transported out from the main adit. For example, in a mine area, due to the large inclined length of the adit uphill section, an inclined shaft was excavated at a suitable location to improve construction efficiency and transportation capacity. The existence of the inclined shaft makes the excavation work on the upper level smoother, waste rock can be removed in time, and the transportation of personnel and materials is more convenient, effectively improving the mine's production efficiency. - Auxiliary inclined shaft - Auxiliary adit - Auxiliary inclined shaft
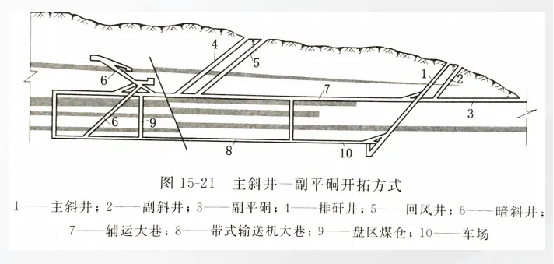
(Picture from MOOC China University of Mining and Technology Mining Engineering Tu Shihao, Fang Zhijun, Zheng Xigui, Wang Xufeng, Peng Hongge, Yuan Yong )
Some mines originally using adit development, when carrying out expansion and renovation to expand the mine type, will excavate a new auxiliary inclined shaft at an appropriate location to increase the mine's auxiliary hoisting capacity, thus forming a main adit - Auxiliary inclined shaft development method. This method fully utilizes the advantages of simple transportation and drainage systems of adits, and at the same time, by adding new auxiliary inclined shafts, it compensates for the shortcomings of adit development in auxiliary hoisting capacity, enabling the mine to adapt to the needs of expanded production.
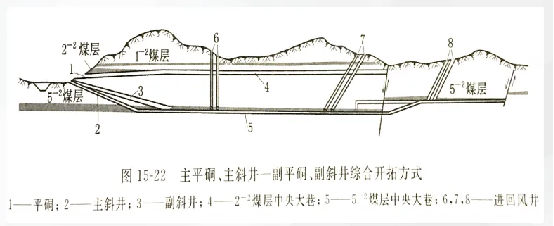
(Picture from MOOC China University of Mining and Technology Mining Engineering Tu Shihao, Fang Zhijun, Zheng Xigui, Wang Xufeng, Peng Hongge, Yuan Yong )
Main inclined shaft - Auxiliary adit development. For large mines mining shallow horizontal coal seams, if there are suitable coal seams and terrain conditions, an adit can be excavated as an auxiliary shaft, an inclined shaft can be excavated and equipped with a belt conveyor to be used as the main shaft. If conditions permit, it can be further equipped with a transportation roadway equipped with a belt conveyor to further improve transportation efficiency and achieve efficient coal transportation. Taking Yujialiang Coal Mine as an example, the mine was rebuilt on the basis of a small mine with a production capacity of 21 万 t/a and adopted a main inclined shaft - Auxiliary adit - Auxiliary inclined adit development method. The auxiliary inclined adit can be used for trackless rubber-tired vehicles, facilitating the transportation of personnel and materials. Through the application of this development method, Yujialiang Coal Mine successfully achieved a significant increase in production capacity, 2007 with an annual coal output exceeding 10 million tons, achieving good economic and social benefits.
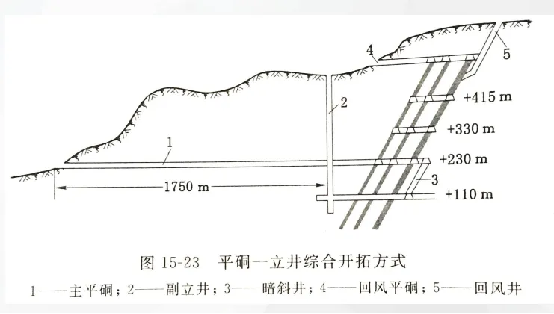
(Picture from MOOC China University of Mining and Technology Mining Engineering Tu Shihao, Fang Zhijun, Zheng Xigui, Wang Xufeng, Peng Hongge, Yuan Yong )
Selection Factors for Comprehensive Development
The selection of a comprehensive development method is a complex process that requires consideration of multiple factors to ensure that the chosen method meets the mine's production needs and achieves efficient, safe, and economical mining goals. The following will elaborate on three main aspects: geological and topographic conditions, production capacity needs, and economic factors.
(1) Geological and Topographic Conditions
Geological and topographic conditions are one of the important factors affecting the choice of comprehensive development methods. They directly relate to the layout of shafts and tunnels, construction difficulty, and mine safety production. Different coal seam dips, thicknesses, and burial depths will all have an important impact on the choice of shaft and tunnel forms.
For coal seams with smaller dips, inclined shaft development may be a more suitable choice. Because in this case, the construction of inclined shafts is relatively easy, and coal transportation can be easily achieved. For example, when the coal seam dip is between ' 8° - 25° ' the characteristics of gently inclined coal seams allow inclined shaft development to fully utilize its advantages, such as relatively low requirements for construction technology and equipment, short construction period, and low initial investment. Through reasonable design of the inclined shaft slope and hoisting system, efficient coal transportation can be achieved to meet the mine's production needs.
When the coal seam dip is larger, reaching ' 25° - 45° ' , it belongs to an inclined coal seam. At this time, vertical shaft development may be more advantageous. The vertical layout of the vertical shaft development shaft, high stability of the hoisting system, can withstand larger hoisting loads, suitable for deep, high-output mine mining. In this case, vertical shaft development can better solve the problems of coal hoisting and transportation, ensuring the safe production of the mine.
Seam thickness is also an important factor affecting the choice of development method. For thin coal seams, due to limited mining space, it is necessary to choose a development method that can adapt to small-space operations. In some suitable terrain conditions, inclined shaft development may be an ideal choice for thin coal seam mining. Inclined shaft development has low construction difficulty and cost, and can quickly achieve coal mining and transportation. For thick coal seams, due to abundant coal reserves, it is necessary to consider how to improve mining efficiency and resource recovery rate. Main inclined shaft - Auxiliary vertical shaft development methods may be more suitable in this case. The main inclined shaft is equipped with a belt conveyor to achieve efficient coal transportation, while the auxiliary vertical shaft is responsible for auxiliary hoisting and ventilation, ensuring normal mine production.
Burial depth also plays a key role in the choice of development method. When the coal seam is buried deep, vertical shaft development is usually the preferred choice because it can effectively solve the hoisting and ventilation problems of deep mining. For example, in mines where the thickness of the topsoil layer above some coal-bearing strata is large, or where the coal seam is buried deep, vertical shaft development, with its advantages of short shaft, fast hoisting speed, and large hoisting capacity, can meet the requirements of deep mining for coal hoisting and ventilation. For shallower coal seams, inclined shaft or inclined tunnel development may be more economical and practical. Inclined shaft development is simple and low-cost; inclined tunnel development has advantages such as a simple transportation system and low ventilation resistance, which can reduce mine construction and operating costs while meeting production needs.
In addition, geological structures such as faults and folds will also affect the development method. In areas with complex geological structures, it is necessary to choose the development method more cautiously to ensure the stability and safety of the shafts and tunnels. For example, in areas with developed faults, it may be necessary to avoid arranging shafts and tunnels near the faults, or to adopt special support measures to ensure the safety of the shafts and tunnels. In folded structural areas, the location and direction of shafts and tunnels need to be reasonably designed according to the morphology and trend of the folds to reduce the impact of geological structures on mining.
(II) Production Capacity Requirements
The size of the open-pit mine's production capacity is closely related to the comprehensive development method. Different production capacity requirements require the selection of different shaft and tunnel combinations to ensure smooth production.
For large open-pit mines, their production capacity is large, and the requirements for the transportation system are also higher. In this case, the main inclined shaft - Auxiliary vertical shaft development methods can often meet their production needs. The main inclined shaft is equipped with a belt conveyor, which has the characteristics of large transportation capacity and high efficiency, and can quickly transport a large amount of coal to the surface. The auxiliary vertical shaft is mainly responsible for auxiliary hoisting and ventilation tasks, ensuring the normal operation of the mine. Through this combination method, large open-pit mines can achieve efficient production and meet the market's large demand for coal.
Small open-pit mines have relatively small production capacity and relatively low requirements for development methods. Main vertical shaft - Auxiliary inclined shaft development methods may be more suitable in this case. The main vertical shaft has a fast hoisting speed and large hoisting capacity, which can meet the needs of small open-pit mines for coal hoisting. The construction of the auxiliary inclined shaft is relatively simple and the cost is low, which can share part of the hoisting task of the main vertical shaft to a certain extent, and can also serve as a safety exit to improve the safety of the mine.
Changes in production capacity will also affect the choice of development method. When an open-pit mine needs to expand its production capacity, it may be necessary to modify or adjust the existing development method. For example, some small mines that were originally developed using vertical shafts may, after expanding their production capacity, need to build a new auxiliary inclined shaft because the original hoisting system cannot meet the increased production needs. The construction of the auxiliary inclined shaft can share part of the hoisting task, complementing the existing vertical shaft to jointly meet the hoisting needs after the mine's production expansion.
(III) Economic Factor Considerations
Economic factors are an important aspect that cannot be ignored in the selection of comprehensive development methods; they directly relate to the mine's investment cost and economic benefits. When selecting a comprehensive development method, it is necessary to fully consider economic factors such as the amount of infrastructure construction, the construction period, ore loss and depletion, and equipment supply to maximize economic benefits.
The amount of infrastructure construction and the construction period are important factors affecting economic costs. Different development methods have different amounts of infrastructure construction and construction periods. For example, the shaft construction of vertical shaft development is difficult, requiring special construction equipment and technology, so the amount of infrastructure construction is large, the construction period is long, and the cost is relatively high. The construction of inclined shaft development and inclined tunnel development is relatively simple, the amount of infrastructure construction and the construction period are relatively short, and the cost is also low. When choosing a development method, it is necessary to consider these factors comprehensively according to the actual situation of the mine to reduce infrastructure costs.
Ore loss and depletion will also have a significant impact on economic benefits. Unreasonable development methods may lead to increased ore loss and depletion, thereby reducing ore recovery rate and quality, affecting the mine's economic benefits. Therefore, when choosing a development method, it is necessary to fully consider how to reduce ore loss and depletion. For example, reasonably designing the location and mining sequence of shafts and tunnels and using advanced mining technologies and equipment can effectively reduce ore loss and depletion and improve ore recovery rate and quality.
Equipment supply is also an important part of economic factor considerations. Different development methods require different types and specifications of equipment, and the procurement, installation, and maintenance costs of the equipment are also different. When choosing a development method, it is necessary to consider the equipment supply situation and cost, choose cost-effective equipment to reduce equipment costs, and consider the reliability and maintenance convenience of the equipment to ensure the normal operation of the equipment and reduce the impact of equipment failures on production.
Taking a certain mining area as an example, when choosing a development method, economic factors were fully considered. After detailed technical and economic demonstration, the mining area compared the amount of infrastructure construction, construction period, equipment cost, ore loss and depletion, etc., of different development methods. Finally, the main inclined shaft was selected. - Auxiliary vertical shaft development method, because this method has a relatively small amount of infrastructure construction, a shorter construction period, lower equipment costs, and can effectively reduce ore loss and depletion while meeting production capacity requirements. Through this choice, the mining area maximized its economic benefits and achieved a good return on investment.
Comprehensive Development Selection Principles
(I) Meeting Output and Quality Requirements
The primary selection principle of the comprehensive development method is to meet output and quality requirements; this is the key to ensuring the mine's economic benefits and market competitiveness. In the coal market, the output and quality of coal directly affect the company's sales and profits. A mine that can stably provide a large amount of high-quality coal can often occupy a dominant position in the market and obtain higher economic benefits.
Taking a certain large coal mine as an example, the coal mine fully considered the output and quality requirements of the mine when selecting the comprehensive development method. Through detailed exploration and analysis of geological conditions, it was determined to adopt the main inclined shaft - The development method uses a main inclined shaft and an auxiliary vertical shaft. The main inclined shaft is equipped with an advanced belt conveyor with high transportation capacity, meeting the transportation needs of large-scale coal mining. The auxiliary vertical shaft mainly undertakes auxiliary hoisting and ventilation tasks, ensuring the normal operation of the mine. This development method has significantly increased the coal output of the mine while ensuring coal quality. Through reasonable mining layout and production management, the mine can produce high-quality coal that meets market demand, enhancing product market competitiveness.
Meeting the requirements for output and quality also requires considering the type and use of coal. Different coal types and uses have different quality requirements. Therefore, when choosing a comprehensive development method, the mining process and transportation system should be reasonably determined based on the type and use of coal. For power coal, the calorific value, ash content, and sulfur content are mainly considered; for coking coal, the binding property and coking property are more important. Through reasonable selection of development methods and production management, coal products that meet the needs of different users can be produced, improving the mine's economic efficiency.
(II) Simplify the production system
Simplifying the production system is one of the important principles in choosing a comprehensive development method. A complex production system not only increases construction and operating costs but also increases the difficulty of production management and reduces production efficiency. Simplifying the production system can improve production efficiency, reduce costs, and create conditions for centralized production.
When choosing a comprehensive development method, it is necessary to fully consider how to simplify the production system. For example, reasonably determine the number, location, and function of shafts and tunnels, avoiding excessive shafts and tunnels and complex transportation routes. By optimizing the layout of shafts and tunnels, the transportation, hoisting, and ventilation of coal are smoother, reducing losses and delays in intermediate links. Using advanced technologies and equipment to achieve automation and intelligence in the production process can also effectively simplify the production system. Automated coal mining equipment, transportation equipment, and ventilation equipment can reduce manual operation, improving production efficiency and safety.
When choosing a comprehensive development method, a certain coal mine fully considered the principle of simplifying the production system. - The mine, through analysis of the geological conditions of the coalfield, determined the use of a main inclined shaft and an auxiliary vertical shaft development method, and reasonably arranged the location of shafts and tunnels. The main inclined shaft is mainly responsible for coal transportation, while the auxiliary vertical shaft is responsible for auxiliary hoisting and ventilation. Through this layout, the coal transportation route is simplified, and transportation efficiency is improved. The mine also uses advanced automated coal mining equipment and transportation equipment, achieving automated control of the production process, reducing manual operation, and further improving production efficiency.
(III) Ensure safe production
Ensuring safe production is the fundamental principle of choosing a comprehensive development method. Coal mine production is a high-risk industry. Accidents not only cause casualties and property losses but also seriously affect the company's reputation and development. Therefore, when choosing a comprehensive development method, relevant coal mine safety production regulations must be strictly followed, a complete ventilation system must be established, the amount of roadway maintenance must be reduced, and safe production in the mine must be ensured.
The ventilation system is an important guarantee for safe production in coal mines. When choosing a comprehensive development method, the ventilation system should be reasonably designed according to the mine's geological conditions and mining scale to ensure sufficient fresh air supply underground and exhaust harmful gases and dust. For example, for mines with high methane content, reasonable ventilation methods and equipment should be used to reduce methane concentration and prevent methane explosion accidents. Reasonable roadway layout, reducing roadway intersections and turns, can also reduce ventilation resistance and improve ventilation efficiency.
Reducing roadway maintenance is also an important measure to ensure safe production. Excessive roadway maintenance not only increases production costs but also affects the normal production of the mine. When choosing a comprehensive development method, the stability and maintenance difficulty of the roadway should be fully considered, and appropriate shaft and tunnel forms and support methods should be selected. For example, in areas with complex geological conditions, using a vertical shaft development method can reduce the exposure of roadways in complex geological conditions, reducing the difficulty of roadway maintenance. Using advanced support technologies and materials, such as anchor rod support and anchor cable support, can also improve roadway stability and reduce roadway maintenance.
(IV) Adapt to technical and equipment conditions
The choice of a comprehensive development method should be adapted to the current national technical level and equipment supply situation. With continuous technological advancements, coal mining technologies and equipment are constantly being updated. Choosing a comprehensive development method that can adapt to the current technical level and equipment supply can not only ensure the normal production of the mine but also create conditions for adopting new technologies and processes, promoting the sustainable development of the mining industry.
Under the current technical level, some advanced coal mining technologies and equipment have been widely used. For example, comprehensive mining technology, comprehensive excavation technology, and automated transportation equipment. - The main inclined shaft and auxiliary vertical shaft development method is widely used in large mines because the main inclined shaft can be equipped with a belt conveyor to achieve efficient coal transportation, which matches the current advanced transportation equipment. The auxiliary vertical shaft can use advanced hoisting equipment to meet the auxiliary hoisting needs of the mine.
The selection of a comprehensive development method also needs to consider the equipment supply situation and maintenance convenience. Some advanced equipment may require specific technical support and maintenance conditions. If the local equipment supply and maintenance capabilities are insufficient, it may affect the normal operation of the equipment. Therefore, when choosing a comprehensive development method, the local equipment supply and maintenance capabilities should be fully considered, and equipment and development methods suitable for local conditions should be selected.
Taking a newly built coal mine as an example, when choosing a comprehensive development method, the current technical level and equipment supply situation were fully considered. - The mine adopted a main inclined shaft and auxiliary vertical shaft development method and was equipped with advanced comprehensive mining equipment, belt conveyors, and automated ventilation equipment. The application of this equipment not only improved the mine's production efficiency and safety but also created conditions for adopting new technologies and processes. Because the equipment supply and maintenance capabilities in the region where the mine is located are strong, equipment repair and maintenance services can be provided in a timely manner, ensuring the normal operation of the equipment.
Summary
As a flexible and efficient development method, comprehensive development plays an irreplaceable role in mine mining. By organically combining various development methods, comprehensive development can fully utilize the advantages of different shaft and tunnel forms, adapt to complex and changeable geological conditions and diversified mining needs, and provide a strong guarantee for efficient and safe mining in the mine.
In practical applications, - main inclined shaft and auxiliary vertical shaft development, - main vertical shaft and auxiliary inclined shaft development, and flat roadway and inclined shaft development - have all shown their own characteristics and advantages. Main inclined shaft and auxiliary vertical shaft development - has performed well in large and extra-large mines, being able to fully utilize the advantages of large main and auxiliary hoisting capacity, simple system, and large ventilation volume; main vertical shaft and - Inclined shafts are suitable for mining coal seams that are not deep, with advantages such as a simple system, low infrastructure construction and investment, and a short construction period; adit - The inclined shaft development plays an important role in different terrains and coal seam conditions, depending on the configuration of the main and auxiliary shafts.
The selection of a comprehensive development method needs to comprehensively consider various aspects, including geological and topographic conditions, production capacity requirements, and economic factors. Geological and topographic conditions, such as coal seam dip angle, thickness, burial depth, and geological structure, directly affect the choice of well form; production capacity requirements determine the combination of well forms to meet the production requirements of mines of different scales; economic factors include infrastructure construction, construction period, ore loss and depletion, equipment supply, etc., to ensure that the selected development method can maximize economic benefits.
Meeting yield and quality requirements, simplifying the production system, ensuring safe production, and adapting to technical and equipment conditions are important principles for selecting a comprehensive development method.
(The article refers to MOOC China University of Mining and Technology Mining Engineering Tu Shihao, Fang Zhijun, Zheng Xigui, Wang Xufeng, Peng Hongge, and Yuan Yong's courseware )
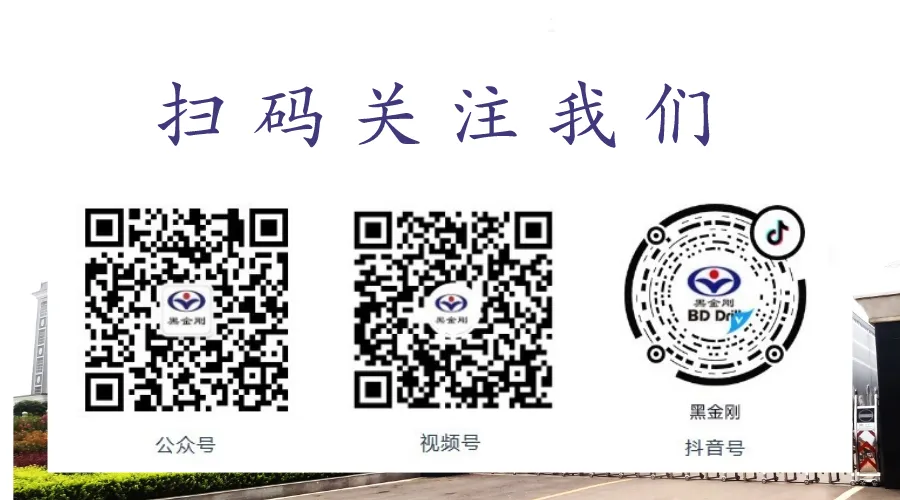